Manitowoc updates Grove TMS9000-2 truck crane with more power and faster setup
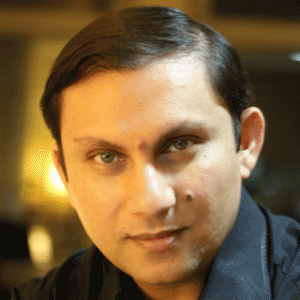
Repowered with new Cummins X12 engine offering an extra 25bhp, updated model also has changes to outrigger design and placement to enhance setup

Manitowoc has updated its 115 USt capacity Grove TMS9000-2 truck-mounted crane with a new engine that increases its power output by 25bhp and has given the model a series of design improvements that enhance operator comfort, reduce machine weight and improve the setup process.
JJ Grace, product manager for truck-mounted cranes at Manitowoc, said: “We updated the Cummins engine from the ISX to the new X12 engine. With the new engine we increased the horsepower to 475bhp, while ensuring compliance with the latest on-highway emissions standards.”
According to a statement from Manitowoc, Grove used the engine repower to introduce a host of additional improvements, “all made in direct response to customer feedback”. The outriggers have undergone a series of modifications for faster and simpler job-site setup. The rear outrigger box has been raised by around 12.7cm to improve the departure angle to 18°, while the front outrigger jacks have been raised 8.89cm to improve ground clearance. This also makes sliding outrigger mats underneath easier.
Manitowoc adds that there is now an extra 7.62cm of outrigger stroke, while the outrigger pad size has been increased from 50.8cm to 61cm.
“Our outrigger improvements can play a big part in making the crane more user-friendly and elevating the overall operating experience. That was a change made in response to customer suggestions and will serve to enhance their trust and confidence in our machines even further,” Grace said.
Manitowoc said that the Grove TMS9000-2 already had the lowest GVW in its class and the latest models are now even lighter at 36.4t the basic configuration. Thanks to the new carrier and engine, almost 453.5kg of excess weight has been trimmed.
The truck crane’s load charts remain unaffected, due to the 11-51.5m six-section MegaformTM boom and its single telescopic cylinder with fully hydraulic Twin-LockTM pinning system. Manitowoc added that its fully automated laser-welding process leaves just one weld seam on the boom, rather than the previous three, to produce a higher-quality, stronger and lighter design.
Grace added: “After we launched the original TMS9000-2 at CONEXPO in 2017, its high level of flexibility quickly won over a large and appreciative customer base. Their use varies greatly from region to region, whether in oil fields or HVAC installations, so we provided a wide range of packages to suit those different needs and markets. Now, with these new modifications — many of which only came about because of Manitowoc’s belief in, and enthusiasm for, the Voice of the Customer product development process — we have enhanced their appeal to a wider array of individual operators, too.”