Tyre technology on the right track
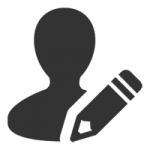
Trends in tyre manufacturing indicate a push towards greater efficiency

Tyres are a significant portion of the operating cost for any company owning a fleet of heavy commercial vehicles, and their importance cannot be overstated. Well-maintained tyres from reputed brands do not only save on fuel costs, they also minimise the risk of accidents or downtime caused by flats or punctures. While it’s important for fleet owners to be well-informed on all aspects of tyre care, it’s also worth examining how manufacturers are working to improve the efficiency and durability of tyres, while also ensuring they are produced in a sustainable way.
Tyre design primarily revolves around three broad elements – tyre geometry, structural architecture and constituent materials – explains Dr Seshu Bhagavathula, chief technology officer at India-based Apollo Tyres. Although the basic function of any tyre is to move loads, the requirements it needs to fulfil differ greatly according to application, and this determines its success, he says.
“The making of a tyre, therefore, begins with detailed market research to understand customer requirements, which become inputs for R&D to create the product. Tyre design involves both virtual and physical simulation tools to build and ensure the necessary product attributes. Different applications call for different tyre characteristics to meet stringent requirements of traction, durability, safety, comfort and so on.”
For city bus applications, for instance, tyres are designed to limit abrasion caused by frequent starts and stops, and are built with protective sidewalls that can resist kerb damage. A long-haul truck or bus tyre, however, needs to be designed for high-speed running with low heat development.
“An off-road truck tyre, on the other hand, requires patterns which provide sufficient traction in various underfoot conditions together with robust materials and construction,” Bhagavathula says.
Apart from pattern, other considerations need to be taken into account for off-road tyres, says Toshifumi Yuze, senior general manager at Sumitomo Rubber Middle East. “Two important features for off-road tyres are a durable casing and an anti-cut/chip durable tread compound. A cut/chip durable compound helps to prevent excessive chipping on the tread from continued running on gravel or stones. A normal on-road tyre tread would not last on these kind of surfaces.”
Naturally, customers also have different expectations from the tyres they buy, depending on the application and usage, points out Bhagavathula. A fleet owner whose vehicles run on highways would expect fuel efficiency and better tyre life, whereas a heavy load application would call for rigidity in structure for durability and safety.
Technological advances
With the global shift towards sustainability becoming evident across all industries, tyre manufacturers are also catching up, and tyres are not only becoming more efficient, they are also being produced in a greener manner.
“Advanced technology is now being used in the tyre industry to lower the rolling resistance and reduce the weight of the tyres. All these efforts reap benefits for the customers, like increased fuel efficiency, reduced CO2 emissions and lower noise,” says Raghavendra Sanga, head of product communication and marketing at UAE-based tyre distributor ZAFCO.
To reduce rolling resistance, materials like polymer fillers are used to modify tyre properties, Bhagavathula notes. In addition, Apollo Tyres is working on new types of carbon black and material formulation, improved steel ply line geometry and tread pattern design.
Meanwhile, Sumitomo, in its efforts to increase the sustainability of its tyres, began working on the development of a fossil-free tyre over a decade ago, containing no material derived from coal or crude oil, says Yuze. When the company introduced the 97% fossil resource-free Enasave 97 tyre in 2008, its last challenge on the quest to 100% was to replace the petroleum-based chemicals – such as rubber antioxidants, vulcanisation accelerators and carbon black – that constituted the remaining 3%.
“Focusing its R&D efforts on overcoming this challenge, Sumitomo Rubber Industries developed technologies that use special catalysts to synthesise rubber antioxidants and vulcanisation accelerators from plant-derived biomass materials. At the same time, we succeeded in producing carbon black from plant-derived oil.”
The firm’s efforts eventually bore fruit, and a 100% fossil resource-free tyre was achieved. In November 2013, the Enasave 100 was launched. In addition to using only non-fossil resource-derived materials, the tyre also delivers a 19% improvement in wear durability compared with the company’s conventional products.
Another trend becoming visible in the tyre industry is a much greater degree of automation in the manufacturing process, notes Jignesh Parekh, managing director at Jaspa, the UAE dealer of Longmarch tyres. While production at tyre factories five to ten years ago had a significant manual aspect and a fair amount of human involvement, this isn’t the case anymore, he says, “from the inflow of material to the tyres coming out of the machinery, being put into storage, and out of the storage into the container”.
The almost non-existent human element ensures there is no contamination, Parekh adds. “We’re seeing factories which are totally temperature-controlled and totally isolated.”
Aside from the push towards sustainability, tyre-makers are also working on delivering better mileage and longevity. ZAFCO has been gearing its efforts towards delivering tyres that not only offer better fuel efficiency and mileage but can also withstand multiple retreads, Sanga says. “All this leads to lower operating costs, which is what every fleet operator is looking for these days.”
In addition, ZAFCO provides regular training to end users on tyre care and maintenance, in a bid to promote awareness, as well as offering after-sales services such as fleet inspections and scrap tyre analysis.
Apollo Tyres is working on studying contact patch behaviour so as to enhance performance, Bhagavathula says. “Vehicle interaction with the road is through the contact tyres make with the road. Hence, contact patch behaviour invariably becomes a subject of detailed research for us. To have the best performance derived out of the tyre, it is important that the designed contact patch behaviour matches with the one that would result in actual application.”
Apart from focusing on the design aspects, Apollo Tyres also works closely with customers to ensure proper wheel alignments and tyre maintenance and inflation pressures – factors that also affect tyre behaviour. “This way we ensure that the products we design give the best mileage in the identified application.”
New opportunities
With all the technological advancements in tyre production, where are manufacturers seeing opportunities for new products?
“There is always room for improvement, and we keep a close eye on capitalising on any opportunity that comes up,” Sanga says. “While complying with the industry standards and regulations, we keep looking into adding features in our tyre range, such as high load-carrying capacity for construction and commercial purposes, and conversion of tube-type tyres into tubeless to contain heat.”
Moreover, the industry as a whole could also see a potential shift away from pneumatic tyres to airless ones not too long from now, Yuze says. “Imagine a situation where one will not have to bother about checking pressure in tyres. A lot of work is being done in this direction, and this will be a game-changer for sure.”
As the automotive sector sees more and more electronics incorporated into vehicles, it would not be surprising to see this carry over into the tyre segment as well.
“Electronics in tyres that enable the tyre to communicate with the vehicle or user is a promising field we are actively pursuing,” Bhagavathula says. “While it can be an enhanced version of the already existing tyre pressure monitoring system for the customer, this can also provide performance input to the design engineer and would help us in product improvement.”
Parekh echoes Bhagavathula’s comments about electronics in tyres gradually becoming more prevalent. “We’re now entering the generation of intelligent tyres. There are tyres available which are self-inflating. They will have sensors inside the tyre, and the moment their inflation goes beyond a certain point, they will re-inflate themselves.”
“There’s also some future concepts coming out where they’re developing tyres which can be used on water. Potentially, your vehicle could go off the road straight into the sea and carry on driving, which is quite revolutionary. I’m very sure that ten years down the line, tyres are going to be very different from what they are today.”
Requirements of GCC customers
With the tough operating conditions so typical in the GCC, it’s not surprising that this is a particularly challenging market for tyre makers to cater to. High ambient temperatures and high speeds need to be taken into account when designing truck and bus tyres for the region.
While ambient temperature is certainly the biggest challenge, roads can get fairly hot too, Parekh says. “Road temperatures can be 60-70°C, and if you look at the temperature of the tyre after it’s been running for 45 minutes to an hour, it actually reaches 70-80 degrees C.”
“Another challenge we see here is because the roads are of very good quality, there’s a lot of high-speed running as well. So you’ll see trucks which are running at 100km/h for four or five hours.”
Although high temperatures are common across the GCC, the applications tyres are most frequently used for vary in each market, Sanga says. While in countries like the UAE and Saudi Arabia, commercial vehicle tyres are typically deployed in long-haul applications, Qatar and Oman are usually known for mixed (on-road/off-road) applications, due to the type of terrain.
Accordingly, tyres need to be manufactured specifically to cope with such conditions, Bhagavathula points out. “The usage of cooler running materials and designs which resist tread deformation and help in faster heat dissipation is always the rule, to ensure the durability of tyres at high ambient temperatures.”