Building Strong

Christine Fashugba finds out about ten existing, new and innovative concrete and cement products
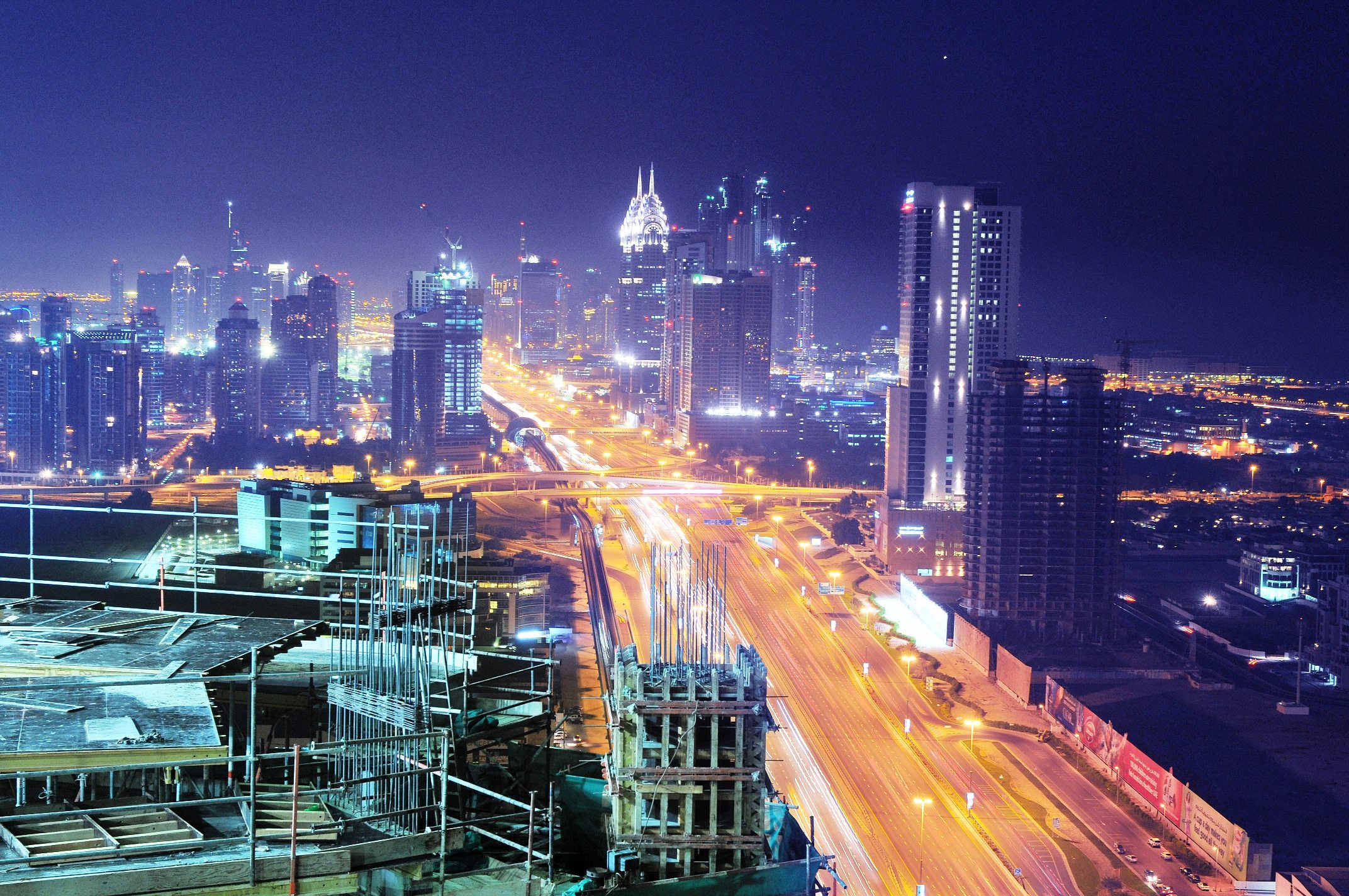
1. Agilia Force
Agilia Force is designed to flow through highly congested, heavily reinforced areas of complex framework and congested reinforcement.
The cement product can be used for any type of construction and its self-compacting properties make the substance particularly suitable for jobs with areas of difficult access or complex formwork configurations.
Advantages of using Agilia Force include a reduction in labour due to the product’s ease of placement and large pour sizes which also reduce plant requirements.
With less labour there are fewer safety hazards and no vibration eliminates the problem of vibration white finger. Noise is also decreased due to traditional methods of placing and finishing concrete, which is particularly important in inner-city and builtup residential areas.
Agilia Force was used at Winson Green Prison in Birmingham, UK, and the walls were completed with a high quality surface finish despite access and security issues. The use of Agilia Force saved both time and money, allowing the project to recover two weeks thus saving £11,000 in site costs.
The product is designed with a compressive strength to suit client specification while meeting their water and cement ratio requirements. Agilia Force also maintains its fluidity for two hours on average and its compressive strength lasts 28 days.
2. Artevia Concrete
Artevia Concrete is a fully customisable decorative solution, which can be used for a variety of interior styles combining design and performance.
The product offers a rich colour palette, textured effects and versatile design enabled by its ability to adapt to complex shapes, quick installation, low maintenance and resistance to wear and tear.
Widely used throughout the Middle Eastern region for projects such as pool decks, patios, sidewalks, driveways, livingrooms and stairways the product can also be used for hotel landscaping with exposed aggregates to produce a sophisticated flooring to match the quality of its hotel, pool surroundings or villa.
Manufacturers of Artevia Concrete believe the material creates driveways, which makes a statement and complexes which stand out from its counterparts.
Although no special products are required for Artevia Concrete’s maintenance, due to the product’s highly durable surface and resistance to temperature variations, the application of a protective sealant every two to three years is recommended to enhance colour and preserve sheen.
The concrete’s extensive colour range was created to suit the vibrant style of the Middle East while providing a concrete solution of high quality finish.
3. Post-tensioning slabs
Thinner than conventional reinforced concrete slabs post-tension slabs lead to less excavation, little or no reinforcement and eliminate all or most of the costly joints. The product can be used on large areas in excess of 2,500m2 and decreases construction time. In addition to a competitive initial cost the slabs benefit owners with low maintenance due to the lack of joints.
The product’s performance is “crack-free” and the initial stressing of the slabs can prevent shrinkage. With a high impact and abrasive resistance the post-tension process leads to the product’s compression while the optimum
concrete strength and surface treatment reduces wear and tear and decreases maintenance requirements.
The large indoor and outdoor slabs are widely used in the construction of pavement areas where a concrete foundation is placed directly on the ground. Projects the post-tension slabs have been used for include warehouses,
distribution centres, container storage terminals, rail and shipping terminals, airports and manufacturing facilities. Slabs are also used in residential purposes and recreational developments such as tennis courts and skating rinks.
The 30,000m2 joint-free slab used for Nestle Distribution Plant constructed by VSL Chile currently holds the world record.
4. i.light
Suez Cement, Egypt, will introduce the innovative product i.light at the Interbuild Exhibition, one of the country’s annual construction events. The substance, described by its manufacturers as a breakthrough product, is a type
of cement which filters in light.
The construction product is used to create panels made with a cement basis which let the light through without compromising on structural integrity.
The cement is said to appear exactly the same as normal concrete from a distance with a transparent grid that gives the effect of dozens of tiny holes in the material.
The inclusion of appropriately sized and transparent polymer?based inserts in the design structure of i.light takes advantage of its transparency properties on a macroscopic scale. Such transparency properties become apparent not only in the element’s ability to transmit natural and artificial light, but also in the human eye’s ability to reconstruct images of objects placed beyond the built structure.
This product is the first of its kind.
5. TX Active
Self-cleaning and de-polluting product TX Active is expected to lead to cleaner buildings and fresher air.
Concrete produced with TX Active work under two types of formulation; TX Arca concrete is self-cleaning and will resist most organic and inorganic pollutants that gather on the surface causing discoloration while TX Aria, which is also self-cleaning, removes significant amounts of environmental elements deemed harmful to human health.
The product works on the photocatalytic principle, an accelerator of an oxidation process that already exists in nature. The system utilises light to alter the speed of a chemical reaction. By taking advantage of the energy of light, the principle accelerates the formation of strong oxidising reagents leading to the decomposition of the organic and inorganic pollutants which accumulate on the product.
Such build-up on the concrete surface causes discoloration. Other compounds diminished or eliminated by the use of TX Active photocatalytic cements during the self-cleaning include soot, grime, and organic particulates as well as
mold, mildew, fungus and tobacco smoke and stains. Potentially, any product containing a cementitious material as its base could be manufactured with TX Active cements.
Uses for the substance include precast and architectural panels, pavements, road surfacing, sidewalks, and other types of concrete.
6. Sulfate-resisting Portland cement
Sulfate-resisting Portland Cement (SRC) has proved to be particularly beneficial in conditions where there is a risk of damage to the concrete from sulfate attack. The product’s use is recommended in conditions where the concrete is exposed to attack from excessive amounts of sulfates, which damage the structure in places where the concrete is in contact with the soil, ground water or exposed to seacoast or sea water.
With less than 5% quantity of tricalcium alumiante and made with raw materials such as coke, limestone, Iron Ore and Iron Scrap Sulfate-resisting Portland Cement can be used for purposes wherever Portland Pozzolana Cement, Slag Cement, and Ordinary Portland Cement are used.
The product should be kept in a dry place to avoid premature hydration and carbonation which causes the quality of cement to deteriorate. It is for this reason the use of Sulfateresisting Portland cement has increased in India where the product is manufactured in large quantities to meet the domestic demand and export to other countries.
7. Ultra Durable Concrete
Sustainable solution Ultra Durable Concrete incorporates a high proportion of cement replacement materials, which minimise environmental impact. Recycled aggregates can also be included in the Durable mix subject according to local availability.
The product offers improved resistance to exposure and enhanced durability in comparison to conventional concrete. The product, which can be used for applications including heavy industrial, underwater, aggressive environments and embedding ducts or pipes, benefits its users with advantages such as improved durability, improved strength and application speed.
Ultra Durable Concrete’s minimum grade of concrete is greater than 25N/m2 and its cement type can be any combination of slag and fly ash extenders with a consistence of S3 and greater.
The product is available with all standard aggregate sizes and incorporates technical features, which enable it to minimise alkali-silica reaction, improve sulphate and chloride resistance as well as achieve higher compressive and mechanical strengths at all ages.
8. Sporosarcina Pasteurii
Sporosarcina Pasteurii, formerly called Bacillus Pasteurii, is the result of research to prove the method microbial induced calcite precipitation [MICP] in conjunction with local sand aggregate can be used to create a “biologically
grown” building material.
The non-pathogenic, common-soil bacterium acts as a binder, similar to Portland cement within concrete and can induce the MICP production of calcite through a chemical reaction, fusing loose aggregate and forming a hardened material.
The substance, which is manufactured through a form of bio-cementation results in physical properties similar to those of natural sandstone.
Although the process takes less than a few days to complete, strength can be increased with additional time, which is achievable at a range of temperatures with a variety of aggregates. The bio-manufactured units are either achieved
by utilising manual casting methods, or automating digital tooling to fabricate layered units with a programmed material composition.
The bacteria then act as nucleation sites, attracting mineral ions from the calcium chloride to the cell wall, forming calcite crystals. Mineral growth fills the gaps between aggregate particles, bio-cementing the aggregate together.
Digital models are also designed to locate mineral templates for growth and different sizes of aggregate for structure.
9. Eco Green Block
Eco Green Block is a panel of polystyrene (EPS) with a length of 1.2ms, a height of 45cm and 2.5 inches thickness. This panel joins with another sheet of polystyrene with the help of the Poly Propylene (PP) connectors, which makes it a
block with a hollow cavity of 15cm.
The entire unit, also known as Insulated Concrete Form (ICF) can be stacked like a Lego system. After the system, which only needs a support structure on one side, is vertically and horizontally reinforced using steel concrete is poured into the hollow cavity.
The block can be adjusted if required with the help of different lengths of PP connectors.
An advantage of ICF is door and window arches can be cut after the walls are erected so when the concrete is poured they are already in shape enabling specified sizes to be made right from the beginning of the construction.
When the polystyrene product is used to create four walls and a roof it produces the airtight effect of a fridge, preserving indoor energy, sealing out air infiltration and reducing the need for air-conditioning.
A conventional block has the insulation value of R1 or R2 while the ICF system has an R value of 22.
10. Lightweight Aggregate
Also called ‘sintered, pulverised fuel ash lightweight aggregate’ Lytag LWA is made by pelletising waste material fly ash produced from electricity production in coal-fired power stations.
The aggregate, which contains a hard honeycombed structure of interconnecting, voids created by adding a controlled quantity of water in specially designed dish pelletising pans which are then heated on a sinter strand
to a temperature of around 1100°C.
The product’s particles are rounded in shape and range in size from 14mm down to fines; these are processed to the required grading, depending on the final use.
As Lytag is a wholly manufactured aggregate, made from a waste stream the quantity of peletised fly ash going to landfill is reduced, as well as the demand on virgin aggregate extraction.
Lytag lightweight aggregate has a Class 1 fire resistance due to the aggregate being produced by a refractory process and weighs approximately 50% less than the conventional aggregate.
In addition, the cellular structure of the aggregate particles relieves any pressures from expanding gases making the material stable at high temperatures. The product will be exhibited this year at Middle East Concrete, International Exhibition and Conference Centre, the region’s event dedicated to the concrete industry.