Clash of the 5t loaders
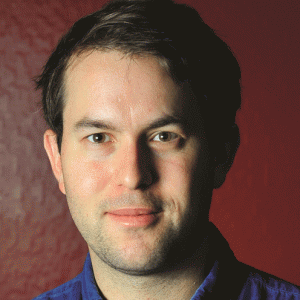
Nowhere is the clash between premium and value more pronounced than in the five-tonne loader segment
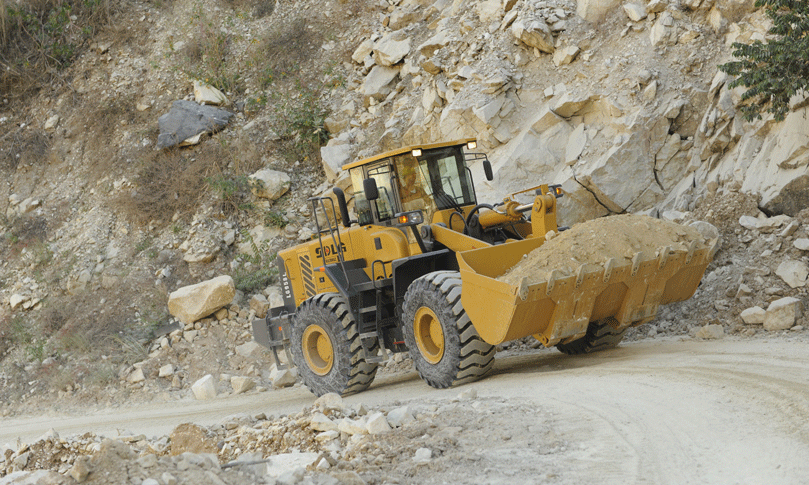
The application requirements of a wheel loader customer can be split between production – such as a quarry, where machines are expected to perform arduous tasks for long shifts – and the less demanding roles, such as stockpiling. Loaders may be expected to perform in both roles, but the general rule of thumb is that the larger the machine, the more production work it does.
While the established machinery brands have traditionally focused on building the most reliable and productive machines possible, for some of the highly engineered loaders the cost of ownership can only be returned in production applications, where a lesser machine has longer cycles and breaks down more frequently.
Conversely, if a production machine is used for a less demanding role such as stockpiling, truck-loading or general construction work, then it’s harder to earn back the machine’s cost. As customers have learnt, in these cases it makes more sense to look for a cheaper option, such as a second-hand or value segment loader. And when it comes to cheaper loaders, manufacturers – especially those in China – are happy to oblige customers.
SDLG, the Volvo CE-owned Chinese manufacturer, has a large range of equipment including excavators and graders, but its five-tonner, the LG958L, is the most popular, confirms Jan-Erik Eriksson, SDLG’s regional business manager in the Middle East. “This is a modern designed machine with excellent comfort and high performance, and we are happy that all the product improvements done on the 2015 models have not affected the cost.”
“This is thanks to a very competent engineering department. In a few markets we are appreciating a market share above 50%, and that tells us that our customers are accepting the product and our after-market support given.”
The machine has an operating weight of 16.6t, and is powered by a 19 litre Weichai engine delivering power of 162kW at 2,200rpm. The loader has a maximum breakout force of 168kN, and maximum torque of 860Nm. Forward travel speed can go as high as 38km/h, while reverse maximum travel speed is 23km/h. The LG598L has a height of 3,382mm, length of 8,020mm and dump height of 3,120mm; standard bucket capacity is 3m3.
Eriksson says that SDLG has a “tremendous focus” on improving its entire after-market operation. “We are very well aware that a customer that buys a value machine has the same demand as any other premium brand customer.
“The only difference is that a value brand customer works with a tighter budget, but his uptime expectations are equal to all other customers’, and his commitment to his customers is important for us. We have to deliver uptime – simple as that!”
The task is made easier by the simplicity of their machines, he explains, with experienced mechanics and product specialists to focus on the repairs. “[There are] no troubleshooting tools needed, no computer that has to be hooked up in an IT network is needed, and when a fault happens to the machine it is fixed in no time, with a minimum of lost production time.”
Typical current applications for the LG958L include load and carry and rehandling operations, but Eriksson is hoping that with the introduction of the motor grade in the SDLG line (replacing Volvo CE’s discontinued grader line), the wheel loader will see good use on road construction job-sites.
Saudi Arabia is by far the largest market for wheel loaders in the GCC, and a large group of customers gravitates to value purchases. XGMA is one company that has made in-roads, selling large volumes of loaders into the Kingdom. It launched its H range in 2013, with 3-8t payloads. Its 5t payloader is offered with three different wheel base options, and benefits from improved efficiency over the previous generation, thanks to the updated XGMA hydraulic system.
LiuGong is another, represented by Al-Qahtani Vehicle & Machinery Co (AHQ) in Saudi Arabia. The company has a busy launch schedule and recently released its new 17.8t wheel loader with a 5t payload, the 856H. It is the first in a new generation of H-series wheel loaders, and in the Middle East will replace the current 856G.
The machine makes extensive use of technology from LiuGong’s two major joint ventures in China, with engine producer Cummins and axle and gearbox producer ZF.
David Beatenbough, vice president in charge of LiuGong’s research and development, says the 5t payload machine will eventually be followed by a 9t payload class loader, and machines with 7-8t, 3t and 4t payloads will all be introduced to the market over the next 18 months.
The Middle East version will use a GCIC engine, produced out of the LiuGong-Cummins joint venture, with a power curve specifically developed for wheel loaders. In the Middle East, most machines will likely be sold with axles and transmissions from the ZF-LiuGong JV.
The project to design the H-series began in 2010, says Beatenbough. “This is the first time that we’ve done a true integrated design from the ground up for a wheel loader. In the past it was more bolting components together, and there was very little looking to see how systems work when they’re coupled with other systems. This changes all of that.”
The machines have been designed by the LiuGong team with all the component systems integrated, including the software controller. “We build our own controller, writing the software and optimising the machine for the needed applications.”
Common features across the range are improved fuel efficiency, a new and wider cabin and improved rear visibility. The machines have been developed by LiuGong’s internal industrial design team, the first project they have worked on.
The development process also included extensive reliability testing, with around 50,000 hours of testing, says Beatenbough. “This gives us a lot of confidence in the component reliability and the whole machine reliability.” The majority of the testing took place in China, since temperature extremes and a full range of operating conditions can be found across the huge country. But H series loaders were tested globally, and a number of 856H units were tested in the Middle East.
Existing LiuGong customers will notice improved efficiency, coming from the tuned engine curve and the integration with the controller, says Beatenbough.
“In terms of owning and operating costs, they’re going to see a difference. You’ll see the same machine response for less fuel-burn.”
But with the onslaught of five-tonners from the value brands, the traditional brands have responded. Caterpillar has launched a down-specced 5t payload wheel loader, and other traditional brands are preparing similar offerings to bring to market.
The drive for Caterpillar to produce a loader in the 5t payload class came out of discussion with customers, explains Frank Stadelmann, a product application specialist at Caterpillar’s S.A.R.L (EAME) headquarters in Geneva, Switzerland, and one of the architects of the machine’s development. Customers were adamant that they wanted a stripped-back machine to fit their business models and the current economic climate, a machine with lower owning and operating costs which could be paid off over a shorter period.
“The world has changed, we see a tremendous shift to new markets and new customers with different value drivers,” explains Stadelmann. “Whereas in the past there was a pretty consistent type of customer we were serving, we see that that spread is growing, from those who value our traditional products and those who don’t value them so much. We needed something new.”
Caterpillar already had a wheel loader in the 5t payload class, the 950H, which remains the high-performance machine in the segment. But according to Stadelmann, the 950H doesn’t represent an attractive value proposition for all customers in the market – it’s a global machine, the outcome of a ‘one machine fits all’ approach. While it has better performance and lower fuel costs, and pays for itself over the machine’s lifetime, “Customers have to be prepared to pay more to get more,” he says. “From the customer interactions we had, we all got the message we had to do something different to remain attractive for a large portion of them.”
The 950 GC will be attractive with companies that have an eye on shorter economic cycles or less market certainty (needing to pay off the machine faster, with less appetite for large up-front investment), customers in new markets (with smaller equipment budgets), and those looking for specific wheel loader applications, with the machine most effective in a support role rather than in continuous use.
Stadelmann sees the machine being used for truck loading, hopper charging and stockpiling, and general construction job site work. Mostly it’s a machine that will be used throughout the day for different jobs, rather than continuously as a production machine. On the front end, the bucket is easy to load, with wider mouth, longer floor and curved side plates, making it easier to pull out and carry a load.
On the technical side, Caterpillar took a mixed approach, introducing some new high-end components as well as going for the more basic options, such as using pilot hydraulics to control the arm and bucket, rather than an electro-hydraulic (EH) pilot system. The advantage of a pilot hydraulic system is that it is easier to maintain, since it is less complex – the control instructions are sent down a slim hydraulic hose.
While with the EH system it’s possible to programme functions such as lift kick out and return to dig from inside the cab, with a pilot hydraulic system the magnets on the arm have to be manually adjusted to change kick-out heights.
There’s also no video screen in the cab, another simplification. “Owners were saying they want operators to load trucks, not to play around with the screen or be distracted by a message that might pop up,” explains Stadelmann.
One high-tech element on the 950 GC is its idling control. The system solves an old-fashioned problem: high idling time, since on average a 5t loader in the Middle East is idle up to 40% of the time. When the parking brake is applied on the 950 GC, the idling control reduces the engine speed even further, down from the ordinary 900rpm idle speed to 600-650rpm.
Another fuel efficiency feature is the load-sensing hydraulic system, with load sensors and a variable displacement piston pump which scales back power to the loader arm and bucket when there is a light load; the pump only delivers the amount of oil and pressure needed, reducing fuel consumption and wasted energy, with the energy used to power the wheels instead.
The loader is powered by a C7.1 engine, with a power rating of 168kW (225hp). It is fed with a common rail electronic injection system, tuned for lower grade fuel and using only about three quarters of the injection pressure capability – with lower pressure, the system is less sensitive to dirty high-sulphur fuel. Meanwhile, a triple fuel filtration system, including a fuel-water separator and dual filter, further ensures trouble-free day-to-day operation.