Big data’s power in construction machinery
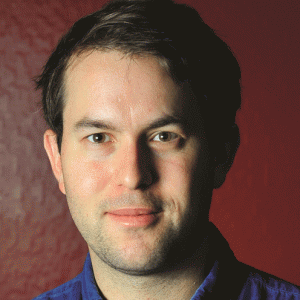
Manufacturers like Caterpillar and Komatsu are looking to harness the predictive power of big data

While the construction machinery industry remains by and large a traditional industry – you can still find machines from the 1960s on some job-sites in the region – manufacturers and end users are embracing the opportunities of the digital age, through improved on-board controls, advance diagnostics and machine control. These technologies improve up-time and performance of machines in the field, but OEMs are also looking to improve their predictive abilities by harnessing the power of big data.
This is part of a general focus on the industrial internet and the Internet of Things, which has been estimated to be a market one day worth $19 trillion, encompassing the whole range of activated technology, from smart phones to cars to construction equipment.
Earlier this year, Caterpillar bought a minority stake in Uptake, a tech start-up in Chicago. Uptake was already developing predictive diagnostics and fleet optimisation solutions for locomotives for Electro-Motive Diesel (EMD), a subsidiary of Caterpillar, and its success made Cat consider the possibilities for the wider field of construction equipment.
Meanwhile, arch-rival Komatsu is collaborating with General Electric to develop its next-generation mining equipment, as well as providing recommendations for optimisation of mines to Komatsu customers, by using GE’s high-powered analysis of data collected by sensors on dumpers.
The new initiatives coalesce around the concepts of big data and the Internet of Things. The term ‘big data’ refers to increasingly huge data sets which can be mined for information, while the Internet of Things refers to embedding objects with electronics to connect to wider networks. Construction equipment manufacturers see opportunities to aggregate the data from their fleet populations, to develop sophisticated models to predict machinery breakdown and to provide enhanced analytics to their customers.
While existing solutions such as on-board diagnostics can measure the performance of individual components, a big data solution would monitor streams of data coming from a machine and provide a more sophisticated picture of machine health, predicting impending breakdown or component failure more accurately. As breakdowns can be expensive, both through lost time and from damage to surrounding components in the case of a major failure, better predictive powers would mean savings for customers.
The largest seller of equipment in the world, Cat has a natural advantage in leveraging big data, with both the resources to invest and the largest data-set – the over three million Cat machines operating across the planet. The company has a solid track record of investing in data solutions to improve machine performance – witness its Cat AccuGrade products and heavy collaboration with Trimble – and is clearly focused on advancing the predictive powers of its monitoring software.
In March, when Caterpillar announced it was buying a stake in Uptake, chairman and CEO Doug Oberhelman was bullish about the benefits. “Customers use our current technology for fleet monitoring and to track fuel efficiency, idle times, location and more. Our existing solutions are effective, but it’s time we take it to the next level.”
Oberhelman feels that Uptake’s software will transform the “quintillion bytes of incoming data we see every day” into useful information to send back to customers. “We want to empower our customers with the insight necessary to shift from a reactive ‘repair after failure’ mode to a proactive ‘repair before failure’ stance.”
While Komatsu stands second in the OEM table, rather than partnering with a smaller start-up as Cat has done, it has partnered with another giant: GE, whose total revenue in 2014 was $148.6bn.
While GE is a big player in the industrial market, with a product portfolio including locomotives, jet engines and the AC engines for Komatsu’s large dumpers, it has also invested heavily in data centres to make good use of the huge volumes of data it receives. GE estimates there are more than 10 million sensors built into the $1 trillion-plus worth of equipment it has sold. Komatsu is now taking advantage of that computing scale, and hopes to return the benefits to its customers.
It’s starting with customers in the mining industry. As is typically the case with high-tech additions to the machinery industry, production applications are best-placed to take advantage of new developments, since minute savings in a single cycle result in major savings across a year of operation. Also, their repetitive nature makes them suited for analysis and primed to benefit from automation.
Komatsu will collect data from sensors on its large dump trucks working in the field and send it to GE’s data centre for analysis, for example improving calculation of the best route through a mine, as well as optimal speeds and braking patterns. According to a report in Nikkei Asian Review, the two companies have done trials at a copper mine in Chile, and plan to offer the data analysis service to customers later this year. While Komatsu’s own analysis alone can boost fuel efficiency by 5%, combining it with GE’s big-data analysis capabilities lifts that figure to around 13%. This means massive fuel savings on a large mine; on a site with 300 trucks, a 1% improvement is estimated to save $4.1 million a year in fuel costs.
Other companies in the industry are following suit, and those which are part of a larger group have a natural advantage. Hitachi Ltd has its own data systems division, which in February this year announced it would buy Florida-based Pentaho, an established big data company, for a reported price of over $500m. “Data remains an untapped resource for many organisations and businesses, with the realisation of the value of that data remaining a challenge,” said Kevin Eggleston, a senior vice president at Hitachi Data Systems. As a result of in-house experience building control systems for bullet trains in Japan, Hitachi CM has embarked on a venture to build autonomous haulers by 2017.
The automotive sector is also focused on data analysis. Volvo Truck’s I-See product (available in Europe) uses topographical maps to help improve gear changing and acceleration to save fuel. The system also takes in road condition data from individual Volvo trucks, making it available to other drivers. Data about a trucking route can also be used to recommend the right vehicle for a specific job.
Following on from its acquisition of a stake in Uptake, Caterpillar has founded a new Analytics & Innovation division comprising both Cat and Uptake staff in Chicago, hoping to accelerate the company’s platform for utilisation of big data. It has also seeded money in a venture capital fund to invest in emerging technologies that could enhance product and service development.
Rob Charter, a group president with responsibility for Customer & Dealer Support, describes the analytics and innovation as a huge opportunity for competitive advantage. “We have a unique opportunity to connect data from the broadest product line that cuts across multiple industries. We can transform the mountains of incoming data – from a single machine or engine, an entire job-site, the supply chain, a shipping location and much more – into valuable information for our customers and suppliers more efficiently and effectively than anyone else.”
How quickly and profoundly OEMs can integrate the predictive advantages of big data in their systems remains to be seen, but the possibility of higher productivity and more up-time means the opportunities are too big to ignore.