Heavy Hitters – John S Taylor, Sitech
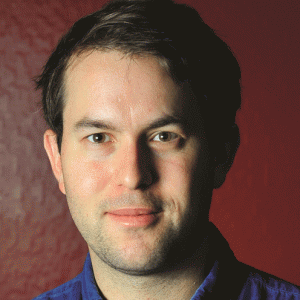
With contractors in the GCC busy building roads, railways, airports and ports, there are serious savings to be had – both in time and money – for contractors who have already adopted machine control technology. Stian Overdahl talks to Sitech’s John Taylor

switch, and you can have an operator with far less experience producing very good grades.”
SITECH Gulf also liases with consultants, when it is needed, to convince them of the efficacy of the MC technology. The quality of earthwork finishing is also noticeable – so contractors can expect to win further contracts on the basis of high productivity and accuracy. There’s also the reduced possibility of a contractor having to redo sections which might not meet the consultant’s spec.
While grading operations are a popular technology to adopt, it’s not to forget the other areas where machine control can be utilised. MC from SITECH for rollers can produce a colour-coded passcount for operators, letting them know how many passes they have completed, and still need to do, as well as measuring a relative compaction value. Excavators can be equipped with MC that will show the operator precisely how deep to dig, or in the case of a island project, can allow them to place marine armour accurately underwater at the required position and depth. Pipeline projects will also benefit from the precision of machine control enabled excavators, especially for gravity feed pipelines where the accuracy is required.
Taylor says that when they first began selling MC technology local contractors were very hesitant, and it was only being used by the international contractors in the region. This view has now certainly shifted, especially when contractors see their competitors utilising MC, or see it on all the machines exhibited at the international shows.
“Over the last few years, you’ve seen the equipment manufacturers push GPS very hard, and I think that’s helping. You see it at Bauma, World of Concrete and ConExpo,” surmises Taylor. “I think we’re at a turning point here in the Middle East, and I think we’re on that edge to where we’ll really start to see some rapid adoption over the next few years.”
The screwing down of contract bid prices also means that contractors who don’t adopt risk missing out on business or profit, he believes. Mistakes on a project can further erode already-thin profit margins. “I think these contracts are getting bid so tight now, that for them to be really financially lucrative, contractors will have to adopt machine control technology.”
Production gains proven
As background for this article, SITECH Gulf’s John Taylor provided to CMME a number of productivity reports it had completed for contractors in the Gulf. Since, while there exists significant literature and reports on the productivity gains from MC, nothing quite compares to seeing the improvements on your own worksite. The typical demonstration is to equip one machine with control systems, and then benchmark that against another similar machine working on the same project, having both machines complete a day’s work on different patches. One customer demonstration used a Cat 14M grader, fitted with a GCS 900 dual GPS system.
This operated alongside a grader working in the conventional way on an embankment, using the string and dip method to attain the top level within allowable tolerance – thus three workers were engaged in the measuring. For the sub base first layer, following the rough grading, the grader completed the final grading of a 220m long, 27m wide strip in 90 minutes, whereas the conventional method takes a minimum of 8 hours. For the top layer, final grading took 115 minutes, versus 4 hours for the conventional method. But how to calculate the cost savings?
There are obviously a lot of variables. Since the grader can cover more ground, a contractor can own fewer machines in his fleet, also lowering the fuel cost. The number of surveyors is reduced, and the helpers are not needed. SITECH calculated a saving of 77% per square metre that needed to be graded for the contractor; while for the individual machine it calculated a production increase of 353%: the normal production machine was able to complete 495m2 per hour (averaged from the 12 hour shift), while the machine control equipped machine was able to finish 1747m2 per hour (it completed the same amount of area in just 3 hours and 25 minutes).
A second test pitted a Caterpillar D8 equipped with AccuGrade against two D8s. the result was that the single D8 increased productivity by 27% over both of the conventionally operated machines. The single machine completed an area of 9000m2, while the two machines in the same shift completed 6571m2. Diesel savings were 63%, while labour was reduced by 96%, in part since no survey control stakes were needed. The AccuGrade method was also far more accurate (accuracy of 1.5cm versus +/- 16cm for the conventional method). The conclusion was that a single D8 with machine control could have replaced all three dozers with nearly the same production – but obviously for a fraction of the price.