Heavy Hitters – John S Taylor, Sitech
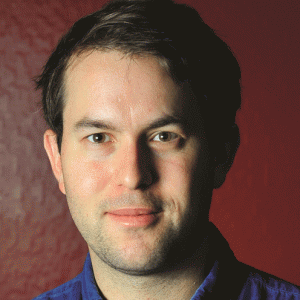
With contractors in the GCC busy building roads, railways, airports and ports, there are serious savings to be had – both in time and money – for contractors who have already adopted machine control technology. Stian Overdahl talks to Sitech’s John Taylor

demonstration day in Abu Dhabi, while working individually with companies to prove to them the benefits of the technology has borne results.
“We have really started to get our ball rolling here even in the past few month,” says Taylor, noting that the company’s products are being used on many of the major projects underway here. It seems that currently the most profitable use of MC is on levelling machines – dozers and graders – as well as rollers and pavers, all machines that play a core role in infrastructure projects. “The technology really shines on road construction, airports and railways. Our tests on road projects show a double in production for graders when using our technology.”
When the company provides a demonstration on a customer’s site, they also do an in-depth study giving a precise comparison of the productivity of the MC-enabled machine versus the ordinary machine working on site. One demo with a MC-enabled D8 showed it to be more productive than the two other D8s working on the site; the conclusion was that a single, automated D8 could do the work of all of the three machines originally working on the project.
“[These reports] really open up a contractor’s eyes to what the benefits of machine control are, beside the accuracy and other things,” explains Taylor. “If we can actually double or triple their production, that’s where we pique their interest.”
He says it’s easier to convince customers working on larger projects to adopt the technology, since they know they have a lot of work to do, and the savings can be easily quantified. But over time contractors with MC-fitted machines are likely to move these machines around to other job sites, where projects may only last several weeks. The technology can be deployed in a 2D or 3D configuration, with the latter more accurate but also costlier. 2D grading uses laser sensors, and is highly effective for fine grading of flat or sloped surfaces, controlling the height of the blade. 2D is fine where what is needed is a flat, levelled surface, such as a carpark or port area, and is even more accurate in this case than GNSS, but lasers will not measure the horizontal position of the machine, which is needed for roads and other similar designs. 3D grading uses GNSS (GPS) antenna, which measures the position and slope of the blade and compares that to design data for rough grading and mass excavation on complex design surfaces. The systems are integrated with the surveying technology, and both 2D and 3D can be operated in either automatic or manual mode.
Machine control obviously isn’t cheap when compared with buyng a new GPS for your car – but for contractors working on a major project the cost savings are signficant. Manpower reductions are dramatic, with workers are no longer needed to pound stakes and check grades. Existing GPS base stations and rovers are compatible with the system. ROIs vary.
Taylor says that a study in Al Ain on a dozer showed that the cost of the upgrade, for a dual GPS, would have paid for itself in 168 days of work. In 23 hours of work during a field test, the single D8 managed 9000m2 of work, while two other D8s, each working 23 hours, only managed a cumulative total of 6500m2. The study was carried out over three days, rather than being extrapolated from a small test period. Taylor says that during a demo they involve the contractor in measuring the production, since some of the numbers are ‘unbelieavable.’
“We want to make sure they’re involved with it, and understand that they’re real numbers. We can calculate diesel savings, and also man-power savings, since stakers aren’t needed. The Al Ain demo was also a neat project since they were leasing the machines, so there was an exact monthly cost for each of the machines.”
But how does it feel for the operators in the cab? Taylor says that, as can be expected, there’s a fair amount of trepidation – if not outright fear – from machine operators, when they see SITECH installing sensors and antennae on the machine, with screens in the cab. In one case, an operator asked him – through a translator – if he would need a college degree. But, after 20 minutes, he was able to work the machine perfectly. Taylor says that from a user point of view, it’s designed to be easy and intuitive, including large screens, with information that is very simple rather than showing complex information.
“We have not had any issues from operators.What this technology does is transform mediocre operators into pretty good operators. For example, the king of the road job-site is the finish grade operator. He’s the guy that can get you that high consistency before you pave, so you don’t have to remill and grind it up. He’s a very high skilled worker, that demands the highest salary and is a bit of a primadonna. Now, with machine control, we’ve taken that advantage away from him. It’s as easy as a flick of a