Heavy Hitters – John S Taylor, Sitech
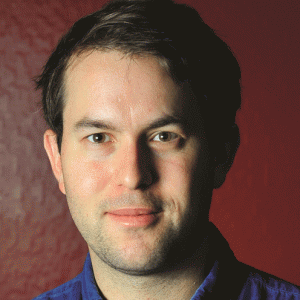
With contractors in the GCC busy building roads, railways, airports and ports, there are serious savings to be had – both in time and money – for contractors who have already adopted machine control technology. Stian Overdahl talks to Sitech’s John Taylor

If you’re a contractor or fleet manager working in construction, and your company is involved in infrastructure projects, the odds are that you’ve heard of machine control or are already using it. After all, it’s a technology designed to improve machine performance and efficiency, reduce the reliance on highly-skilled operators, and lower overall job costs. So what’s not to like?
For machine control in the Middle East, it seems that there is simultaneously both good news and bad news. The bad news is that uptake of machine control (MC) in the Middle East lags behind the rest of the world (less than 1% of machines here equipped with MC); the good news is that contractors can make their fleet suddenly perform dramatically better by adopting the technology. Bad news is that implementing MC across a fleet has a cost; the good news is that in the long term their business will become more profitable through lower operating costs, and ROIs can be low. The bad news is that MC is still relatively new in the construction machinery market, which means that there can be problems with compatibility, and not all manufacturers are equally invested in MC; but the good news is that there are some excellent players in the market with long track records, who are delivering proven results.
Almost all equipment used in repetitive, process actions can be fitted with machine control (MC) technology. MC for bulldozers and motor graders can be used to complete earthworks to a high level of precision, and with far less reliance on operator skill. Excavator sensors allows operators to quickly dig to accurate depths. And many manufacturers have developed automation controls for their specialised machines, such as BOMAG with its highly accurate compaction controls for its rollers, or Wirtgen, with a slipform paver that can pave according to the surveying plan, without the use of pegs. In the tower crane industry, anti-collision controls automatically prevent tower crane clashes, and put in place safe-working parameters for operators.
Japanese manufacturer Komatsu has invested signficantly in machine control technology, and is allianced with Topcon. Its most recent and advanced product is its machines equipped with intelligent machine control (iMC), notably its D61PXi-23 launched at Bauma last year, while four iMC dozers are being shown this month in Las Vegas. The iMC technology is fully integrated into the dozer during the factory build, meaning that the sensors and controls are built into deep into the core of its hydraulics. Komatsu believes it’s the most sophisticated MC product on the market, and it can transition seamlessly from rough dozing to finish grading, allowing operators of all levels of experience to operate the machines.
When activated, the blade lowers until it meets the target surface or until the blade load reaches a maximum. Before the blade overloads, it automatically rises to minimize track slip and maintain forward momentum.
This maximses productivity and minimises track wear and damage to the target surface. Factory integration also means that the sensor packages and cables are internal, or placed in areas of the machine that will protect them from daily wear. Internal testing by the company suggests that improvement in combination rough dozing efficiency is up to 13% higher in iMC machines than for other brands of add-on machine control systems it tested.
A major provider of machine control tech in the GCC is SITECH Gulf, part of Mohamed Abdulrahman Al-Bahar group of companies, which operates in Oman, UAE, Qatar, Kuwait and Bahrain. SITECH itself is a global brand, established as a partnership between Trimble, one of the oldest innovators in the field of surveying equipment and MC, and Caterpillar. The technology can be implemented on almost any brand of equipment, whether Komatsu, John Deere, or Volvo CE, though in all cases, the newer the machine the easier the installation process will be (new machines can be specified as ‘Trimble-ready’ from many manufacturers). Nevertheless, buyers using Caterpillar machines will be able to receive more machine information through the VisionLink software relating to machines usage or fault codes.
John Taylor, COO for SITECH Gulf, says that the company has made significant strides in the past year, since the company held a well-attended