Plug and Play

BPME visits Unipods’ plant to find out how it’s meeting increasing annual demand
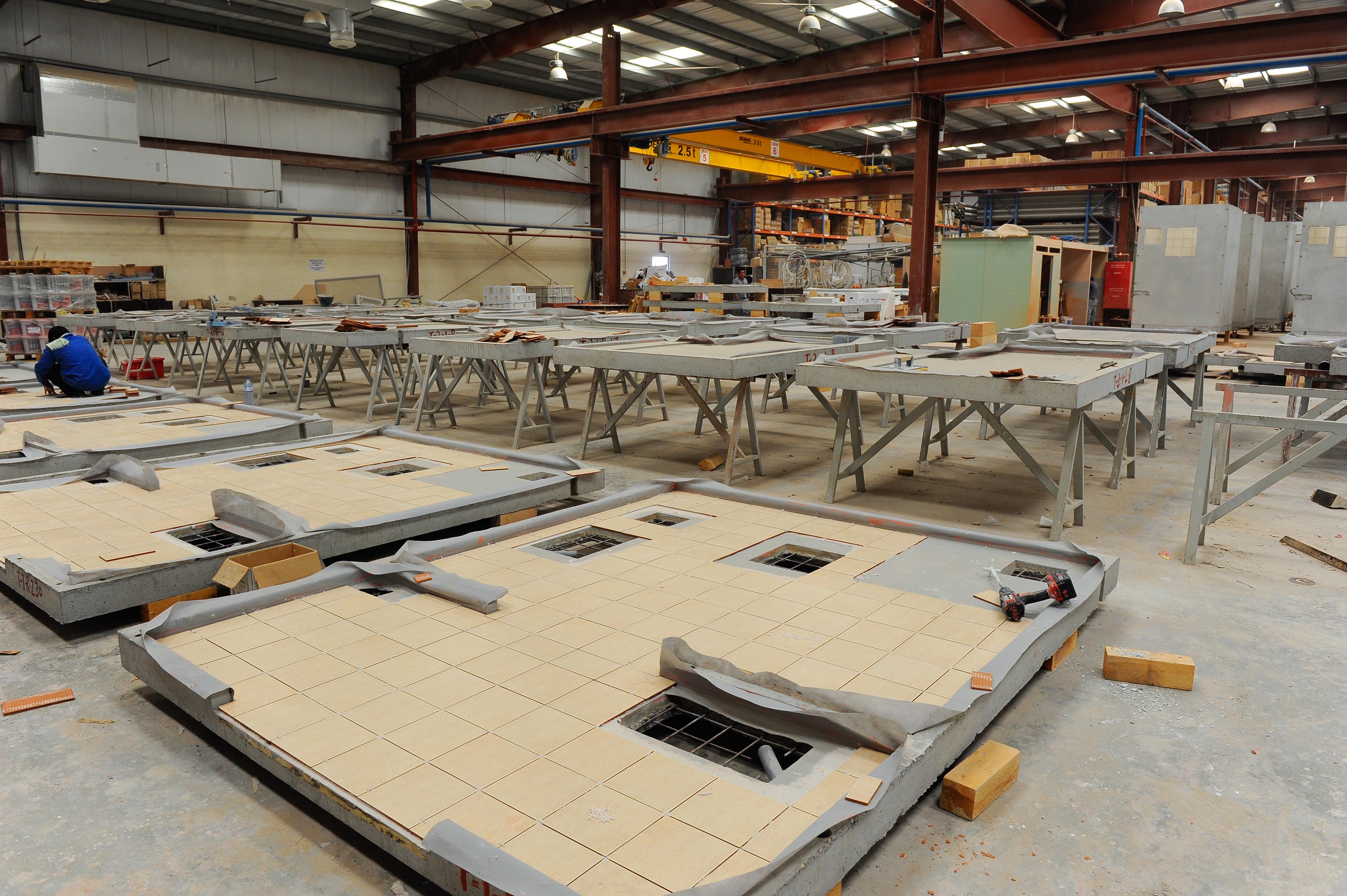
The concept appears to be simple: Build and fit out a project’s most time consuming rooms offsite and deliver them – complete with their own walls, floors, fixtures, fittings and MEP requirements – as quickly as four weeks after their design is signed off.
The company behind the idea in the Middle East, Unipods LLC, is based in Ras Al Khaimah, UAE. Now in its fifth year of operation, the firm has built and supplied bathroom and kitchen pods for projects in the UAE, Qatar and Saudi Arabia.
In short, the primary benefit is control – over everything from quality to waste. Even the cost of projects can be set before design and manufacturing commence.
The concept is far from alien, with chains such as Premier Inn, Travel Lodge and even McDonalds using the method to fit out their hotels and restaurants for decades, yet it’s an idea that is only just beginning to catch on in the Middle East.
The product is based on the pre-plumbed modular system (PPMs) currently used in Europe, PPMs are preassembled in the factory, fitted with access panels, sanitary ware, flushing systems and brassware and delivered to site ready for simple installation.
“Clients here don’t fully understand the concept of the pods, so one of the first things we do is invite them to the factory to see how they are made,” says technical director Gary Barrass, who was headhunted from the UK to launch the business under Al Rajhi Holding.
“There are a few things that we do when clients are in the factory to demonstrate that what you get is as good as if not far superior to what you can usually expect on site.
“For example, we lift the completed pods, which have shower screens and sanitary ware fitted, with a forklift truck and nothing will fall apart,” Barras continues to explain, saying the next challenge is to answer clients’ logistical questions about drainage, delivery and lead times.
“It’s quite simple, there are drains in the pods and we can deliver them between four to eight weeks of design sign off. They pay what they are quoted and the units are delivered on time, because we’re not part of their project chain. But to really make a project efficient the pods need to be specified in the design stage, which is before the fit out project is traditionally considered,” he adds.
Planning ahead
On a standard project that has a number of identical rooms, such as hotels, student accommodation and residential developments, the interior fit out of a project is undertaken by a whole team of plumbers, electricians, tillers and quality control supervisors, all brought in once the project shell has been built. Barrass says it is changing this mentality that is the greatest challenge in the Middle East.
“This concept reduces the issue of supervising tradesmen, because everything is manufactured as a single product here and that manufacturing process is supervised. It’s a real plug and play concept.
“But we didn’t realise how difficult the regional market would be. We thought construction means opportunity then when we began speaking to consultants, suppliers, main contractors, and we are trying to sell something that isn’t too complicated, we just need clients to be onboard with the concept from early in the design stage of the entire building,” Barrass reiterates.
In the UK and Europe the idea of pods and modular design isn’t just familiar to the industry, but even the general population. In 1998, McDonald’s decided to branch out from fast burgers to fast building and Barrass, while working for his former employer, was on the team of 173 people that built an entire restaurant and cooked and served a burger in 23 hours and 19 minutes. A record that included travel time from the factory in Hull to the vacant tarmac lot in Runcorn.
The project was a world record, achieved through steel piling and light steel pre-fabricated modules, but despite time demands in the Middle East, similar concepts are only just beginning to catch on.
With similarly impressive speed as the McDonald’s record,
Currently Unipods of supplying to the second phase of the Dammam University project – one which, in phase one saw pods installed into student accommodation at a rate of 24 per day. In addition, the company is working on ARAC Hotel, Makkah; Jizan Housing project, Jeddah; Porto Arabia, Qatar; villas and townhouses at The Pearl, Qatar; and D1 Tower, Dubai.
“Every project has a different challenge and the language barrier for me is a big one, that’s why we demonstrate what we do. But in terms of the project, the biggest challenge is going from drawing board to factory,” Barrass adds.
Concept to completion
In taking the project from drawing board to factory, clients work with senior designer Steven Michael Fisher to combine their vision and requirements with what is technically feasible.
“We receive a specification of what the client expects and then we design that according to their budget. From there we get drawings from the architect and MEP consultants and we fit the pod to those requirements,” says Fisher.
“There’s quite a lot of technical work in that process and We’re often asked questions such as ‘will it fit’, so we advise on where a wall can be removed and penetrations in the slab will be placed,” he adds.
Supported by projects manager Abdul Monem Zaher and production manager Jorgen Bahne Hansen, the team liaise with contractors, developers and designers ensure everything from the size of the tiles to the wind pressure on the building is tested and checked.
“We begin by talking to the client about their needs and our designers help the client meet a solution that is best for the site and for the project. The products inside the pod may be changed and so on, and each project is bespoke,” Hansen explains.
“The length of the design process hinges on the client, but from the point when they sign off the design, things move very quickly,” he adds.
The pods are then undergo waterproofing tests and pressure testing on all the water pipes, drainage and electricity.
“Another big advantage is that the fitting of tiling and plumbing is coordinated so the finishes aren’t damaged by other work,” Hansen says, adding that if construction of the shell faces delays, completed pods can be stored at the Ras Al Khaimah plant.
Unipods isn’tn just about bathrooms. As part of its “off site construction technology” remit, Unipods also manufactures kitchens and washrooms, and with repeat clients now developing a greater understanding of the potential of pods, it’s unlikely to stop there.
“People understand it more now. For example we had a client view the reference pods and they said that for their next projects they wanted one concrete wall and the others gypsum. Then for the next project they want us to do a whole bedroom, fully furnished,” Barrass shares.
“We’ve been doing rooms like that for years, for example with the Travel Lodge hotel chains in Europe, so hopefully that idea can come here now,” he adds.