Twisted Thinking
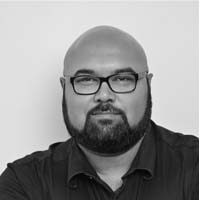
Gavin Davids examines the highest addition to Kuwait’s skyline, the Al Hamra Firdous Tower, a truly iconic structure
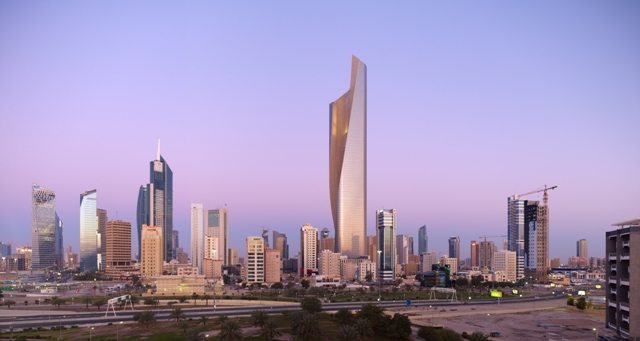
Ever since they opened in 1979, Kuwait City’s skyline has been defined by the needle like silhouettes of the Kuwait Towers, which serve the dual purpose of being functional water towers and iconic symbols of the Gulf Arab state.
However, over the last decade there has been a surge in construction in the tiny, oil rich state, which has ambitious plans for its growth in the coming years. As a result, Kuwait City’s skyline has undergone a massive transformation, with all ten of its tallest buildings being built within the last ten years.
One such building is the Al Hamra Firdous Tower which opened its doors in November of 2011, following nearly six years of stop-start construction and numerous delays.
Designed by the US based architecture firm, Skidmore, Owings and Merrill (SOM) the 412m building towers over Kuwait City, providing it with a new defining image, one that mirrors the country’s progress and growth over the course of the 2000s.
Covering nearly 195,000m2 in total area, the building houses 74 stories and serves as a mixed use development, with both retail and office space being available.
Initially planned as a 50 storey tower, the project started life as the design of a local firm, Al Jazera Consultants. But a sudden about turn by Kuwait’s government, when they changed zoning regulations to allow taller structures to be built, prompted a change of plans to build a truly iconic building.
As a result, SOM were called in by the developer, Al Hamra Real Estate, and were given the remit to design a super-tall structure that would rival the best in the world.
Having worked on a number of previous projects including One World Trade Centre, Jiangxi Nanchang Greenland Zifeng Tower and the Beijing Greenland Dawangjing Tower, SOM has a wealth of experience in designing buildings like this, and were well established in the region, having been responsible for the Burj Khalifa; which at 828m, is the world’s tallest tower.
Located on an intersection of two main streets, the Al Hamra Tower has a six story shopping centre at its base, providing high end retail, cafes, restaurants, cinemas and various other entertainment areas, according to information sourced from the Council of Tall Buildings and Urban Habitats.
Furthermore, there are 195 offices available for lease in the tower itself, providing a net office leasable area of 77,000m2. The offices are ‘Smart and Hi-tech Offices’, designed and built to multi-national standards, with fibre-optic cabling, advanced security systems and IP telephony systems.
In addition, the development has an 11 floor car park that holds around 1727 cars. There are also extensive landscaped areas around the building, with marble, water features and ‘soft landscaping’ all combining to provide a distinctive feel to the building and its surrounding environments.
However, what really gives the tower its unique selling point is its innovative facade which has a 130 degree sweeping turn, with two ‘fins’ sprouting from the top and bottom of the building, going in opposite directions, thereby creating a completely asymmetrical exterior.
“The building’s appearance resembles a subtle, elegant modern sculpture or an enshrouded figure with its delicate glass veil reflecting the profile of the peninsula. The resultant form will provide transparency on the north, east and west sides towards the Gulf and near-complete opacity against the severe desert sun to the south,” SOM says.
Furthermore, the south side of the building’s wall has been designed and constructed with the aim of minimising the solar heat gain on the office floors, while also maximising views for tenants. As a result, a quarter of each floor plate is chiselled out of the south side, shifting from west to east over the height of the tower.
“The result reveals a rich, monolithic stone at the south wall, framed by a graceful, twisting ribbon of torque walls, defining the iconic form of the tower,” the architecture firm adds.
In addition, the south wall serves as the structural spine of the building, helping protect it from critical environment conditions.
The carefully placed windows and openings also help decrease solar radiation with each positioned in relation to the sun and the relationship of the envelope, thereby helping to minimise the building’s solar heat gain, a vitally important feature in a region where summer temperatures can reach 50?C.
Furthermore, when it came to planning for the flow of traffic through the building, a sky bridge runs between the two wings, on each floor of the tower, allowing for the flow of people in a smooth and easy manner, as well as providing tenants with dramatic views of the city, peninsula and desert thanks to its panoramic windows.
Named as one of the best inventions of 2011 by Time Magazine, Al Hamra Tower is a marriage of mathematics and architecture, with the point at the apex of the tower not only resolving the complex geometry of the curved, flared walls, but also implies the continuation of the sculptural form.
While a steel framework has traditionally been associated with skyscrapers of this height, the designers and constructors of Al Hamra Tower took a different approach to its completion.
Nearly 500,000tns of concrete went into its construction, with all of that concrete required to be pumped vertically. Not only was this a challenging task in itself, but because of the unique design of the building, the outermost corner of the main structural wall was a mammoth 45.72metres away from the building itself.
Furthermore, as construction continued, engineers realised that the spiralling form would concentrate gravity loads on the west side of the building, while very little load would be applied to the north and southeast edges.
In response to this load differential, the engineers came up with a plant to install a 4 metre thick reinforced concrete raft that was supported on 289 piles, each between 20 and 27 metres long, with deeper piles located densely around the areas of greatest stress.
The raft, which required approximately 22,900m3 of concrete, was poured into 15 different sections, over a period of four months, contractors say. They add that this approach was not only necessary because of local production capacity levels, but also because it allowed them to come to grips with the heat generated during concrete hydration.
Given the particular environmental conditions, this was a very real concern for the architects and contractors, who decided to counteract this by building at night.
Furthermore, the building’s design and construction help its lateral and gravity-load resisting systems to function efficiently, thanks to the thick south facing wall and the lighter, more delicate ‘flared walls’.
During the construction process, SOM devised a ‘construction compensate program’, which allowed the contractor to adjust the ‘self-climbing’ framework with each pour, so as to compensate for the displacement caused by the building’s ‘counter-clockwise-torqued geometry’.
This allowed for the elastic movement of the concrete under its own weight and its long term movement from natural shrinkage and expansion.
As such, the building is an iconic structure in more ways than one, with its architects and contractors taking a revolutionary approach to its construction and indirectly changing the face of construction in Qatar forever.