Against time and on form
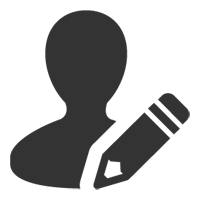
Ten-month target for new campus
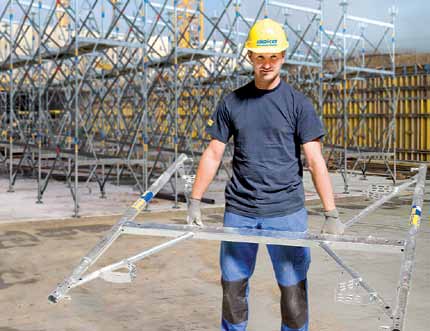
Challenged with building the first phase of Manipal University’s new campus in ten months, contractors Sobha targeted their formwork requirements to meet a tight deadline.
When Manipal University embarked on a plan to build a new campus in Dubai, time was of the essence. The plan was to construct a two-block science and technology department with a project value of US $27 million, located in Dubai Academic City, and to be completed in ten months.
The first of three phases in a 69,700 square meter development, blocks A and B – due for completion in mid 2011 will soon be supported by a 3,000 square meter capacity accommodation block, two further teaching blocks and parking facilities.
“We are due to complete Block A and Block B in June 2011, in order to begin using them in August. So it meant we had only ten months to complete the project,” says Sobha Contracting’s vice president of projects, B. Vidya Sagar.
With a challenging design incorporating cantilever slabs and three-storey corridors and a terrace floor, Sobha analysed the most efficient way to execute the plans and targeted the project’s formwork requirements in order to meet the imposed deadlines.
“We needed to achieve a 15 day cycle per floor of 2,300m2. The material component is huge so the labour and time elements became critical,” Sagar explains.
“We specified Doka’s Staxo 40 load-bearing system because we needed something which could be erected and dismantled quickly,” he adds, further saying that the lightweight shoring system was “technically more suitable”.
According to Doka’s technical manager, Alexander Macho, among the primary elements posing a challenge to construction — besides the geometrically challenging design, area size and time to construct — were the forming of the cantilever slab, and the double height requirements at the entrance.
“Phase two is on the drawing board right now, phase three will replicate the two blocks currently under construction and there is already talk of constructing additional parking areas”
Doka engineering provided a working platform designed to transfer the loads safely from the cantilever slabs to the lower floor. Due to design changes, by deploying the use of downstand beams, it was possible to reduce the slab thickness from 300mm to 125 mm.
Doka provided further solutions to work around additional requirements mid-project.
“The cantilever slab was in the upper floor so to support it all the way down would have required a lot of materials and it would also have taken time to erect the supporting structure.
Therefore a customized cantilever platform using standard Doka systems and components was very helpful solution for Sobha” Macho adds.
Finding a solution
According to Sobha, the specification of Doka formwork in the project was based on three vital elements; safety, speed and efficiency.
Staxo 40 was developed to offer additional strength, providing clients with an efficient shoring system to meet project needs. The systems was launched by Doka worldwide at the end of 2010 and first used in the UAE during the construction of a school in Abu Dhabi, where around 2,300 square metres of formwork was constructed and delivered to the site, as required, in two weeks.
Designed by Doka’s Austria-based research and development department, engineers used the “finite element method”, popular in aerospace design, to pioneer the use of ultra lightweight materials.
By using this method in the constructional design process, Doka’s engineers were able to reduce the weight of the Staxo 40 frame while improving its strength. As a result a standar version Staxo 40 frame weighs between 15 and 24 kg and has provided time savings of up to 80% on projects in the UAE, compared to traditional scaffolding systems.
“The market here requires fast, efficient and safe work,” says Michael Arnold, Doka’s Dubai sales and branch manager.
“More and more, Dubai is becoming focused on safety issues and this site is accident free. Staxo 40 features, such as the tested anchorage points for personal fall arrest systems, integrated safety catches for fixing the diagonal crosses, gapless assembly decks in and between the towers, and a sturdy built-in ladder system, all ensure a safe working environment at any height, Arnold continues.
“For the cantilever working platform, even for the non-standardised areas, Doka advised and designed with ultimate safety precautions,” Arnold adds.
Staxo 40 is constructed with a small number of separate parts and is colour coded to enhance speed and ease of usage, which Macho calls “a logical assembly grid”, likening the ease of assembly to building with Lego.
Staxo 40 provides faster erection and dismantling times and can be set up faster than single-leg shoring towers, which often weight up to 32% more, comprising up to 78% more separate parts.
“The cantilever slab was in the upper floor so to support it all the way down would have required a lot of materials and it would also have taken time to erect the supporting structure”
The H-shaped frame makes it possible to have gapless, full-area assembly decks both inside and between towers. Under the towerframe structure is 1.70m headroom and additionally work-deck levels can be extended beyond the scaffold itself, to extend below cantilevering structures. When it comes to repositioning, erected Staxo 40 towers can be travelled on shifting-wheels, or crane lifted in their entirety, without dismantling.
“Usually, in conventional systems you have many single elements which are connected together, but here you have a minimal amount of elements constructing the tower. It basically consists of the H shape frame which allows gapless, full-area assembly decks not only inside the towers, but also — for the first time ever — between them as well., diagonal crosses of different lengths and foot and head units. This allows for a planned assembly procedure,” Arnold explains.
Sagar adds:“Before with the other systems, we had too many small parts and the chances of losing them or not assembling them properly was higher. But here it has all been made with a minimum number of components so safety wise it’s much more reliable and it is much more economical,”
Once used, the rented equipment is returned to Doka for reconditioning at a newly opened, 50,000 square metre facility in JAFZA. Sagar says the reconditioning process at Doka’s Yard further reduces costs as the client’s materials are returned to usable state.
Building blocks
Formerly operating as Indeset, Sobha Contracting has been executing projects in Dubai since 1992. After acquiring Al Belad Contracting Company LLC in 2003, The company began trading as Sobha in 2005.
[facts]
Activities undertaken by Sobha Contracting:
- Real Estate
- Civil Contracting
- MEP Contracting
- Metal Working
- Facade Engineering
- Interiors
[/facts]
Major projects include the Yacht Club at Dubai Marina; IT Plaza, Silicon Oasis and a number of industrial and residential projects. The company also has on-going projects at Dubai’s Business Bay, Jumeirah Village, Sports City and Ghantoot, among others.
With campuses already in India, Nepal, Antigua and Malaysia, Sagar says Manipal University has “big plans” for Dubai, strengthening an existing campus located in Dubai Academic City, which opened in 2006 following a move from Knowledge Village in 2003. “This large-scale project is divided into multiple phases. Phase two is on the drawing board right now, phase three will replicate the two blocks currently under construction and there is already talk of constructing additional parking areas,” Sagar adds.
Upon completion of the project, the new facilities will also allow the institution to deliver more courses, specifically in engineering and technology. Sagar concludes: “The schemes and the vision are there.”