Ten tips: Machine servicing
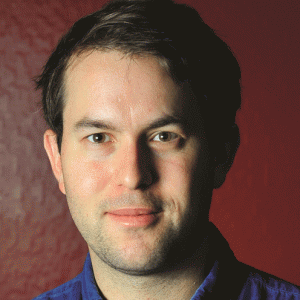
The most important things to remember to keep your fleet running efficiently

1. Daily checks
Operators should be trained to do visual inspections of their machines before they start work on the shift. This includes a walkaround, checking for obvious damage from the previous shift, such as loose hoses, fittings or any oil residue that can signal a leak. Safety equipment should also be checked before starting work.
2. Ensure wear edges are in good condition
Cutting edges on attachments, such as the teeth on excavator buckets, the bits on hydraulic breakers and any other wearing part, should be checked by operators before a shift starts. Worn out teeth or bits should be promptly replaced, otherwise the machine will have reduced productivity, and there will be extra stress placed on the machine’s powertrain.
3. Perform regular greasing
Regular greasing is required to extend your machine’s life, and failing to do so will cause extra wear. Greasing should be done according to your machine’s specified intervals, and more frequently if working in dusty, abrasive conditions.
4. Follow recommended service intervals
All manufacturers will provide guidance on the recommended service intervals, for everything from those features which need to be checked every 10 hours of operation, to those that only need to be changed once a year. Adhering to these guidelines requires accurate documentation of how many hours a machine is used per day so that regular maintenance can be scheduled.
5. Tailor to the conditions
Experienced fleet managers in the Middle East will tell you that there are certain parts of a machine that struggle with the harsh conditions, such as the heat, moisture or dust, and may recommend changing these more regularly than specified by the OEM. For machines that are operating in more abrasive environments, you may choose to reduce service intervals on filters or fluids that are taking the brunt of the conditions, such as the hydraulic system oil, to limit the chance of breakdown.
6. Buy machines that are easy to service
Manufacturers design machines with the end user in mind, and that includes servicing. But not all machines are created equal, and some are easier for your technicians and operators to service, including having all checkpoints reachable from the ground, or bunching together of the checkpoints. If the service checks are made to be easy, they’re more likely to be carried out.
7. Use authorised spare parts
Genuine parts may cost more up front than some of the alternatives, but they also last longer and are designed to operate within the system of the machine. An under-performing component or filter may end up affecting your entire machine’s operation, and failure may be catastrophic and costly.
8. Oil sampling
Regular oil sampling should be an important part of your preventative maintenance programme. Sending an oil sample to your manufacturer, dealer or maintenance contrator’s laboratory allows them to check the wear status of components to detect imminent component failure before it occurs.
9. Telematics
Effective use of telematics can significantly improve your servicing regimen. It allows you to accurately measure usage and schedule required maintenance. Telematics can also perform diagnostic functions, alerting you to a problem with the machine. Diagnostic alerts can even be visible on a machine’s onboard display.
10. Total rebuild
Rebuilds are available from a number of dealers, and can be a way to extend the operating life of a machine. Rebuilt machines are normally available with warranties, and can incorporate newer features. In most cases, a rebuild is more economical than buying a new machine, though it depends on the capital value of the machine and the total rebuild cost.