A CAT among the pigeons
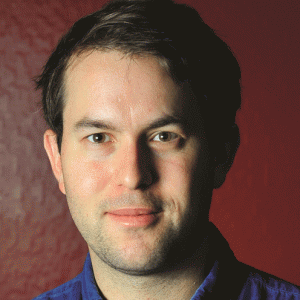
The inside story of Cat’s new 950 GC loader

As quickly as high-tech machinery and telematics features are changing the industry, at its core the basic demand on manufacturers hasn’t changed: build and sell machines that fit with the customers’ demands. And that’s why Caterpillar’s newest 5-tonne wheel loader, the 950 GC, isn’t stacked with features which are expensive and high-tech: the industry’s biggest player is going after the value segment, where customers favour a lower acquisition cost. Ahead of the machine’s official launch in the Middle East, CMME’s Stian Overdahl spoke with the product application specialists in charge of the new machine, Vincent Danloy and Frank Stadelmann, at Caterpillar’s S.A.R.L (EAME) headquarters in Geneva, Switzerland. Both are experts on wheel loaders, as well as the Middle East and emerging markets, and say the drive to produce a new wheel loader in the 5-tonne payload class came out of discussion with customers, who were adamant that they wanted a stripped back machine to fit their business models and the current economic climate, namely a machine with lower owning and operating costs, which could be paid off over a shorter period.
“The world has changed, we see a tremendous shift to new markets and new customers with different value drivers,” explained Stadelmann. “Whereas in the past there was a pretty consistent type of customer we were serving, we see that that spread is growing, from those who value our traditional products and those who don’t value them so much. We needed something new.”
It’s a shift that has been felt perhaps most acutely in the wheel loader segment, and the 5-tonne class was specifically targeted. Caterpillar already has a wheel loader in that class, the 950H, which remains the high performance – or production – machine in the segment. But according to Stadelmann, the 950H doesn’t represent an attractive value proposition for all customers in the market; it’s a global machine, the outcome of a ‘one machine fits all’ approach. While it has better performance and lower fuel costs, and pays for itself over the machine’s lifetime, “customers have to be prepared to pay more to get more,” he said. “From the customer interactions we had, we all got the message we had to do something different to remain attractive for a large portion of them.”
The 950 GC will be attractive with companies that have an eye on shorter economic cycles or less market certainty (needing to pay off the machine faster, with less appetite for large up-front investment), customers in new markets (with smaller equipment budgets), and those looking for specific wheel loader applications, with the machine most effective in a support role rather than in continuous use. Stadelmann sees the machine being used for truck loading, hopper charging and stockpiling, and general construction job site work. Mostly it’s a machine that will be utilised throughout the day for different jobs, rather than continuously as a production machine. On the front end, the bucket is easy to load, with wider mouth, longer floor and curved side plates, making it easier to pull out and carry a load.
For his part, Danloy describes the development of the 950 GC as a shift from a product-centric approach to a customer-centric strategy. The product-centric approach was required to build the machines that had to meet the new emission standards in the highly regulated country (HRC) markets, whereas the customer-centric approach is more heavily based on customer demands and requirements.
Out of this, the team designed a machine that fitted the main customer demands for ease of operation, reliability and lower operating costs, including fuel and maintenance. In this sense they started with a blank slate, and it was an entirely bottom-up design process, starting from the customers’ requirements.
And while it may have been tempting to simply roll out an older version of a Cat loader, the 950 GC is a mix of proven technology and new technology, including elements taken from the hydraulic system of the advanced K-Series loaders in use in Europe. And with the machine remaining completely Caterpillar, reliability was a core parameter for the loader.
Since ease of operation was a must-have for the 950 GC, it is built with a longer loader arm than the 950H, to make dumping into trucks easier and for better reach. Simplified controls means that any operator should be able to jump into the cab and control the machine with ease. There’s also the combined tilt and lift movement feature from the 950H, meaning that there is no priority of the lift movement over the tilt.
Under the skin, the steering system uses pilot hydraulics to control the arm and bucket, rather than an electro-hydraulic (EH) pilot system. The advantage of a pilot hydraulic system is that it is easier to maintain, since it is less complex – the control instructions are sent down a slim hydraulic hose. What is the trade-off? With the EH system it’s possible to programme functions such as lift kick out and return to dig from inside the cab, and it’s also possible to adjust the sensitivity of the machine controls by plugging in a laptop. With a pilot hydraulic system, the magnets on the arm have to be manually adjusted to change kick out heights.
There’s also no video screen in the cab, another simplification. “Owners were saying they want operators to load trucks, not to play around with the screen or be distracted by a message that might pop up,” comments Stadelmann.
Nevertheless the cab is still comfortable, with air conditioning and a suspension seat both standard. And the ROPS structure itself is from the next generation of wheel loaders, built out of hydro-formed steel tubes. These pillars are offset from the corners, which gives operators better visibility, especially at the rear, a cab structure that will be introduced onto future Caterpillar loaders.
Another instance of a high-tech element used on the 950 GC is its idling control. The system is being used to solve an old-fashioned problem: high idling time, since, on average, a 5-tonne loader in the Middle East will be idle up to 40 percent of the time. When the parking brake is applied on the 950 GC, the idling control reduces the engine speed even further, down from the ordinary 900rpm idle speed to 600-650rpm.
Another fuel efficiency feature is the load sensing hydraulic system, with load sensors and a variable displacement piston pump which scales back power to the loader arm and bucket when there is a light load; the pump only delivers the amount of oil and pressure needed, reducing fuel consumption and wasted energy, with the energy used to power the wheels instead.
The loader is powered by a C7.1 engine, with a power rating of 168 kW (225 hp). It is fed with a common rail electronic injection system, tuned for lower grade fuel and using only about three quarters of the injection pressure capability – with lower pressure the system is less sensitive to dirty fuel. Meanwhile, a triple fuel filtration system, including a fuel-water separator and dual filter, further ensures trouble-free operation.
With pre-production versions of the machines tested in countries including Russia, China, Peru, Indonesia, the UAE and Bahrain, Stadelmann says that there have been no issues at all with fuel or the engine, with the C7.1 an established engine.
And on the topic of its Middle East trials, the machine is fitted with High Ambient Cooling capability as standard in the region, allowing it to work in heat of up to 50 degrees. For improved performance in dusty environments, the air flow goes from the rear and into the side (some machines are the opposite), so there is less risk of plugging, as can happen when the air is taken from behind the wheel (side into rear), where the wheel kicks up dust.
Service and maintenance is another area where they’ve looked to shave costs. It’s no secret that customers in the Middle East and Africa prefer machines that are easy for them to repair themselves, if only because they may be operating on remote jobsites; and with the reduction in electronics on the machine, service teams should have an easier time. And as with the 950H, the filters for the hydraulic and transmission oils are on the side of the machine in a single service centre, accessible from the ground, as too are the Scheduled Oil Sampling (SOS) ports. This also make the job of servicing and maintenance safer, and the 950 GC retains the guard rails as well as many other safety features of the 950H.
While there is no special meaning behind the ‘GC’ in the name, representatives from Caterpillar’s dealer for Kuwait, Bahrain, UAE, Qatar and Oman, Al Bahar Group, have been joking that there is a missing ‘C’ in the name, wanting it to be called the ‘950 GCC’. Wishful thinking as it may be, it’s certainly the case that it’s a machine that is likely to appeal to buyers here – after all, it will potentially allow customers to buy a new Caterpillar machine at a price-point that previously would only have applied to second-hand machines. And it’s also been tested extensively in the region: as part of Caterpillar’s process to validate machines before they get released for production, one of the pilot machines – there were many around the world – was in the Dubai and Bahrain with Al Bahar, to test the machine in extreme temperatures and dusty environments. Al Bahar also recorded the first sale of a 950 GC in the Middle East, to a buyer in Kuwait.
According to Vincent Danloy, one major differentiator separating the 950 GC from the competition in its segment is that the entire powertrain system is designed and built by Caterpillar.
“Everything involved with the powertrain is made by Caterpillar, from the engine to the axle, for maximum efficiency,” Danloy said in comments in Caterpillar’s in-house magazine. ”It’s much better value as opposed to our competitors, who use off-the-shelf components from different manufacturers.”
When questioned by CMME, Danloy was quick to emphasise that the sentiment is no slight on the quality of driveline components from manufacturers who supply to OEMs, but just a comment about the design expertise involved in developing their transmission.
“When you design the engine down to the axle, you can optimise them to fit together, to get to the best fuel efficiency. I’m not saying that the off-the-shelf components – [brands X and Y] – I’m not saying that those components aren’t good, it’s just that they aren’t necessarily optimised to work together. I think because we control the whole process, we provide superior value to our customers, in terms of fuel efficiency and overall.”