Tooling up in Taiwan
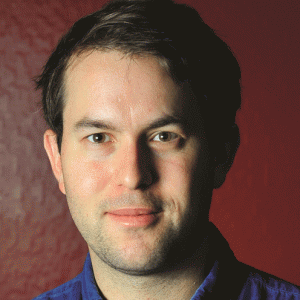
Stian Overdahl visits Taiwan to learn how technology advances are improving methods for manufacturing componentry, contributing to improved quality standards for construction machinery
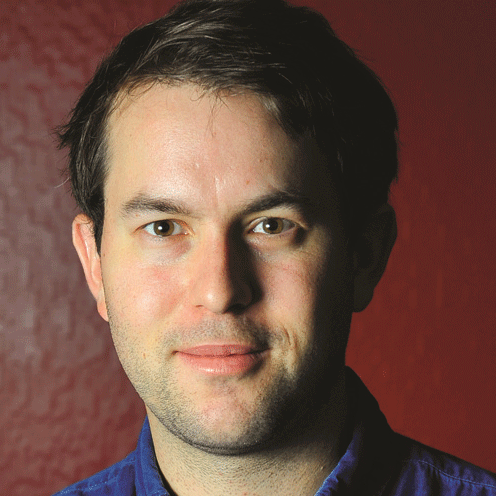
Taiwan is a major producer of machine tools, used in factories around the world in the manufacturing of construction machinery and vehicles. CMME international editor Stian Overdahl visited the island nation to learn how technology advances are improving methods for manufacturing componentry, contributing to improved quality standards for construction machinery.
Though a small island to the east of the Chinese mainland, Taiwan has always punched above its weight as a manufacturing base, despite its relatively small population of 23 million. In the 1970s and 80s, before the rise of the giant Chinese manufacturing industry, Taiwan was a major producer of simple consumer goods, and many will remember the stamp ‘Made in Taiwan’ on cheap consumer items. But, with the rise of China, the factories producing volume goods moved across the Taiwan Straight, onto the mainland (Foxconn, Taiwan’s largest consumer technology manufacturer, which assembles Apple products amongst others, has most of its assembly plants in China), and Taiwan has had to focus on more high tech manufacturing, becoming now the fourth largest manufacturer of machine tools in the world, behind Germany, the USA and China.
Taiwanese producers of machine tools are seeing some increase in orders from companies in the GCC, with manufacturing hubs in Dubai, Sharjah and in Saudi Arabia. Typical products manufactured in the Gulf can include formed steel used in construction, such as frames for drywall, and other products used in infrastructure, such as the steel barriers used on highway edges, and lampposts. There are also industries such as stone cutting machinery and producers of paving stones which require large, often custom-built machinery. In addition, there are a number of automotive assembly plants in the region, who source some components locally, and as a sector its volume is set to increase, especially in Saudi Arabia. While smaller size manufacturing companies will purchase small numbers of machine tools, once their volume increases it becomes more important to establish efficient manufacturing processes, in which high tech and precision tools play an important part.
Export figures from the Taiwan Association of Machinery Industry (TAMI) show that in 2012 the UAE was the 23rd largest buyer of machine tools from Taiwan, and Saudi Arabia the 24th, and the GCC is considered a future growth region, and of strategic importance, especially as the manufacturing industries grow. Nevertheless, in terms of volumes, the GCC has only a fraction of the five largest buyers of Taiwan machine tools, respectively China, the USA, Japan, Thailand and Indonesia. Another major regional buyer is Turkey, with a relatively advance manufacturing base. For construction, this includes asphalt and concrete batching plants, generator sets, automotive brands including trucks, as well as major manufacturers that have plants there.
Machine tools have a variety of segments, and Taiwan produces a broad range of machines, with machining centres being the largest segment, followed by lathes, grinding, presses and shearing, and as well as precision tools such as linear actuators, and the switches and sensors used industries as construction (including batching plants) and petrochemicals.
Taiwanese companies are aided by government tax relief for expenditure on research and development, and in some segments of the machine tool industry R&D expenditure can be as high as 20%, a opposed to the normal 3-5% of R&D spend.
Finetek is a producer of level instruments – which are used to measure all sorts of variables, including temperature, water levels and pressure – and is one of only a handful of manufacturers worldwide with such a broad range. Examples of applications include sensors inside concrete batching plants, temperature gauges inside Nespresso-style coffee machines, sensors for measuring water content of ballast tanks inside ships, and numerous applications in the petrochemicals industry, including monitoring water presence in oil tanks.
Level instruments are often delivered as a custom solution for individual clients, and building a sensor to a required specification is a project that can at times take more than a year, especially if it is a demanding application, such as in the oil and gas sector where the instrumentation often must be explosive proof.
Chin Fong is the largest producer of presses in Taiwan, and its products include tandem press lines, which involves using numerous presses in a line to produce a high volume of formed metal parts, including the panels used in the automotive industry. The company first provided a tandem press to a Toyota plant in Taiwan in 1986, and the association with the Japanese automotive producer has continued (the tandem press line itself is still running), while it has also provided presses to companies that include Mazda and a ThyssenKrupp subsidiary in China. In China it has a factory with a production area of 32,000m2, a plant in the United States, plus five plants in Taiwan.
A slightly smaller player in the press industry in Taiwan is SEYI, which grew from building simple presses in the 1960s, to a full range of presses today, from 25 to 2,400 tonnes. It has worked with a number of major corporations including Hitachi Zosen Fukui Corp. for a Chinese production plant, and
Nevertheless, due to competition from the Chinese market, which is able to build the smaller and cheaper presses at a competitive price, but not the larger presses which are more complex, SEYI has begun a process of positioning itself in the market as a provider of larger size presses, the higher margin, lower volume product.
One recent development in the field of presses is the utilization of a servo motor, which is a high torque, low rpm solution to driving the press, and has yielded new advancements in the methods for forming metals. A servo motor confers a number of benefits to a press machine, including delivering the maximum torque only when the press is actually stamping, saving on energy, as well as a vastly reduced noise signature. The servo drives are also able to be programmed with more precise and more complex stamping patterns, delivering multiple taps or presses within the pattern of a single stroke.
Looking to the machinery industry, while the forklift business segment is arguably the most competitive segment in the industry, Taiwan material handling equipment manufacturer Tailift is inside the top 20 companies globally in terms of forklift volume. This is in no small part due to its large presence in the Chinese market, where it has invested heavily in a sales network, support resources, as well as a large manufacturing plant. Its range extends from electric counterbalance trucks, Gasoline and LPG powered, diesel, as well as pallet trucks and towing tractors. On the counterbalance trucks, capacities range from 1 tonne to 3 tonnes on electric, up to 5 tonne for the gasoline/LPG line, and up to 16 tonnes on its premium diesel-powered products.
The company also produces a range of machining centres, as well as CNC turret punch presses, used for complex perforation patterns in plated steel, its application sounding like bullets. When CMME visited their headquarters, now mainly an R&D centre, engineers were experimenting with the use of a robotic arm to use on a side-press machine, replacing the humans who place the metal for stamping. While Taiwan and China’s manufacturing industries involve large amounts of manual labour compared with practices in Europe, North America and Japan, the trend is towards increasing automatisation of processes, including replacing humans that interface with machine tools, with robots.