A mountain of rock
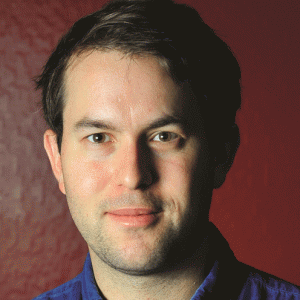
CMME’s International Editor Stian Overdahl returns to Stevin Rock to learn how operator training has helped the huge mine fill orders and boost productivity in the last year

Drive north past the city of Ras Al Khaimah, in the UAE’s northernmost emirate, and you’ll soon find yourself on a sliver of land alongside the Arabian Gulf, surrounded by industrial plants, factories, a huge harbour, and the trucks and conveyors that move material between them.
But the landscape is dominated by the brownish mountains that rise up from the land, and for the government of the emirate contain a wealth of limestone resources. Stevin Rock, the quarrying company owned by the ruler of Ras Al Khaimah, which access to 17 billion tonnes of surveyed reserves.
And it is the Q2 site, that begins inland a few hundred metres from the port, which is the largest site of extraction. Last year 29.5 million tonnes of material was produced by Q2, an increase of nearly two million tonnes on the previous year’s production. The hills contain limestone of the highest quality, with low silica and low magnesium content, which is needed for the production of steel, and other industrial processes. Stevin Rock supplies several million tonnes each year to the steel industry in India, as well as to local factories such as RAK Ceramic, the largest ceramic manufacturing company in the world. Limestone with higher silica content is used for general purpose aggregate, such as in construction.
The varying qualities of the limestone means that the quarry has to be mapped out by a geologist, and the different materials kept separate, to avoid contamination, or in cases blended together to produce the required chemical content.
Alastair Gibson, shift superintendent, has the job of roving about the mine during the day, keeping an eye on all the processes, and intervening where necessary. “I’m everywhere on the course of the day”.
Gibson reports to the operations manager, Simon Turner. As a background, Gibson has worked in open cast coal mining in Scotland, and in a limestone quarry in the UK. The quarry, which had an annual output of 1.5mt, was deemed one of the largest in the UK. By comparison, Stevin Rock produces 2.5mt every month.
“It’s a different scale here”, says Gibson. The company runs 24 hours a day, seven days a week, with the staff working two 12 hour shifts each day. The day shift has a one hour break, during which blasting takes place, while breaks during the night shift are staggered. Up to 700 people will work on a shift, and at the Q2 site, there are about 1,200 people working.
The continuous nature of the operation means that machines are putting in long hours. Gibson says that during a recent trip to Japan to visit the Komatsu manufacturing facilities, the staff there were shocked to learn that the amount of work the machines were doing, since in Japan, quarries work no more than 10 hours a day.
“We can easily put 6000 hours on a machine in a year. They were shocked when we told them that. But that’s 22 hours a day, 365 days a year.”
The machines will be taken out for regular servicing, but other than that they will continuously, in effect until they are too old, at which point they are likely to be moved to one of Stevin Rock’s smaller quarry sites. At the Q2 site office is the machine workshop, itself a small factory with some 200 staff, who can repair buckets, teeth, and even build customer grabbers for the marine armour work. The company can do virtually everything for a machine – it even has its own oil testing facilities, to monitor wear levels on its machine components, while the local dealers will work on the machines at the site where it is covered by the service agreement.
Doing the oil samples in-house means that test reports can come back that same day, and so they very quickly know if there is fault with a part in a machine. There is also a full revamp shop for refurbishing of engines and transmissions, while the manufacturers hold a significant amount of spare parts, with Caterpillar and Komatsu having their Middle East spare parts centres in Jebel Ali.
The scale of the operation at Stevin Rock inevitably gives it an advantage when it comes to filling its customers’ orders, since it can virtually guarantee it can fill an order, on time and with the specified qualities. By one industry estimation, Stevin Rock is responsible for producing 70% of total limestone produced in the UAE. The mine holds very little in the way of stockpiles, since material can be weathered or contaminated if stored on site, so most of the material is being mined for orders that are being filled – straight out of the ground, down the mountain, and on to the boats.
Production in 2013 outstripped the previous year, and Gibson credits improvement in operator skills as being a big factor in being able to increase output. The staff have worked to educate drivers on improved technique, and the manufacturers of the loading machines (Komatsu and Caterpillar) have also brought driving instructors to the site to carry out training. The skill of the operators in the loading machines can make a large difference in the overall efficiency of the quarry, whereas the skill of the truck drivers is less of a factor.
For the Caterpillar 390 excavators, the goal is to load the trucks in 10 passes, in 3-3.5 minutes. Anything above that is caused by very bad blasting, or a poor operator, says Gibson.
The shift superintendent spends a lot of time on a daily shift monitoring performance of vehicles operators – “Are machines being operated efficiently, are they being operated correctly? Do we have the machines in the right place, are we feeding the right amount of trucks? Are we loading in the right areas?” They monitor the production of the quarry over three hour periods, and if production starts slow at the beginning of a shift, it needs to be picked up to reach the shift’s targets. Production outputs can vary – machines may need to be swapped around or moved early in the morning, and there tend to be a lot of variations in daily production explains Gibson. The police are in charge of monitoring the safety of the blasting, and at times they will ask for machines to be removed from near the blasting area, which can be time consuming.
On top of the business of extraction, the team are also engaged in serious construction project on-site, a long term plan to move the 2nd crusher higher up the hill, and closer to the blasting faces. At the same time, they are building a conveyance system which will bring the crushed material down the mountain from the main crusher to the screening plants. The system of conveyors is being designed and built by Quarry & Mining, a local company that is the agent for Kleemann and Stiebel, as well as manufacturing material handling systems. It has previously installed a conveyor system on the other side of the quarry, taking the material down the hill from crusher 1, and even using the braking energy to generate electricity.
The chief advantage of the conveyor system is that it replaces the use of trucks, and Gibson has estimated that the new system, with up to 14km of track will take 8-10 of the large 100 tonne dumpers off the mountain. The new placement of the crusher will also see increased flexibility: the crusher will be installed with a 800 tonne dump hopper – double the size of the current hopper – and it will also have a total of six dump stations for trucks to unload into it. The conveyor system will also have two lines, the B-grade line coming from the aggregate crusher, and the a-grade line.
Having increased flexibility and redundancy in the system will help to mitigate the inevitable production snags that occur in an operation of this size – on the day that CMME visited the mine, the number two crusher had its operation interrupted after a foreign object went into the jaws. Trucks backed up with full loads, and loading machines stood idle waiting for empty trucks. It was a vivid illustration of how important it is for the mine’s productivity that all aspects of the process flow smoothly, or, at least, the importance of in-built redundancies.
Looking to the year ahead, and the demand from the industrial users is expected to be stable, while the possibility for growth comes from construction contracts being awarded in the UAE, especially with the impetus of the 2020. Qatar is also a market for the mine, and it is likely it will have to provide a large amount of material for the construction work there – but the exact dates and amounts are not yet timetabled. With the number of contracts rising and falling, any month can be the largest for production – in 2013, it was July and August that had the largest outputs, rising to 2.7 and 2.8mt– meaning that men and machines have to be prepared for the gruelling work and long hours.