GPS: Smarter not harder
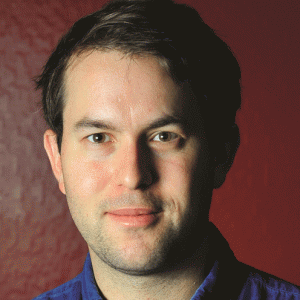
You don’t think twice about buying a newer smartphone with improved features. But does your fleet also need a tech upgrade? Stian Overdahl writes.


Caterpillar recently released an upgraded version of its VisionLink product, which is the user interface which links with Product Link
We live in a world where advancements in computing technology – especially mobile – are a given, and no-one thinks twice about checking their emails while out of the office. Yet despite advancements in communication technology, not all construction companies are taking advantage of IT tools to improve their fleet management.
Knowing where machines are located on a jobsite, how they are being used and whether operators are efficient, is an important part of any construction manager’s job. Most managers visit a jobsite everyday to check progress, and in the process will often need to dispense advice about technique and efficiencies for machinery operators.
And though there may never be a replacement for having a physical presence on the jobsite, machine telematics are providing an extra set of eyes for plant and construction managers, as well as providing tools for longer-range analysis of individual machine and operator functioning.
Telematics had its birth in the trucking industry, with GPS used to track vehicle location over long trips, as well as monitor fuel usage, a critical component for the industry’s profitability. In the construction machinery industry, telematic products are offered by all of the major manufacturers, and there are also third-party product offerings available.
Most telematic systems have a chip that collects information from the machine, which is then transmitted either via cellular network, GPS satelite or else cable, to the site manager’s computer. Increasingly monitoring updates are also available directly to smart phone or tablet applications.
The main areas of machine operation that are monitored include idle time, machine position, fuel levels and consumption, payload information and cycle times, as well as fault codes.
Telematics also allow plant managers to create schedules for maintenance and receive reminder alerts in advance, and the systems will also send alerts if fault codes are detected on-board.
Managers can also geofence their machines, setting up parameters around the job site, and will receive an alert if one of the geofenced machines leaves the site or is in the wrong area. This can be useful in extreme cases such as theft or use of the machine by employees outside of hours, but more often it will be used when a construction site is adjacent a critical area such as a gas pipeline or railway track, and the machines are forbidden to enter the area.
In Europe, telematic systems were been developed to improve fuel costs, as well as combat machinery theft. Machinery theft is less of an issue in the Middle East, but despite significantly lower fuel costs, diesel still contributes a significant percentage to a job’s overall cost.
And one of the main contributors to fuel usage in the Middle East is idle time. Idling also generates extra wear and tear on the components and increases maintenance costs with respect to the amount of work carried out.
Machine idle time can occur due to poorly organised job site: for example, if there are not enough trucks and the loader operators are forced to wait a long period between fills. Or it can simply be a case of employees sitting in the cabin with the engine running to take advantage of the cabin air-conditioning. With telematics, managers can analyse and compare the idling time of various operators, and target those who have the lowest utilisation rates.
The amount of money that can be saved by operators is illustrated by a recent case study from Qatar, where Al Jaber Engineering (JEC) in Qatar approached the local Caterpillar dealer Mohamed Abdul Rahman Al Bahar, with an interest in using CAT’s Product Link telematics on their fleet. JEC was established as a part of Al Jaber Group in 1995, and has around 1700 pieces of equipment in its fleet.
Before investing on the product across their fleet, they agreed on a demonstration on one of their Cat 345D excavators. Over a demonstration period encompassing 758 hours, the monitoring detected two problems – unnecessarily high idling time, and a specific sensor fault.
Of the 758 hours the machine had been in operation, 270 of these had been spent idle, equating to 36% idling. As a result the operator was provided with additional training, which over the next section of the trial resulted in idling time being reduced