The Whistleblower
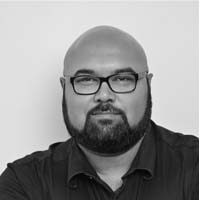
William Whistler is ready to lift the lid on an issue that’s often hidden away

The first thing that strikes you about William Whistler is that he doesn’t hold back when it comes to expressing his opinions and that those opinions are invariably forthright and cut right to the heart of the matter.
Having worked as an architect for the last 33 years, Whistler has had ample opportunity to air those opinions as he made his way across the world, working on projects in the US, Japan, India, the UK and Germany, both as an architect based in New York City and as director of design on an international level for Fidelity Investments, one of the largest mutual fund and financial services groups in the world.
In 2008, he moved to Dubai to work with the Engineers Office, where he was tasked with bringing in management techniques and reining in control procedures, as he says.
“I did quality assurance and control, design guidelines, supervision protocols, all kinds of things like that. My orientation has always been as a designer, and I’ve always been striving for quality or the right thing in what I’m doing. And as I’ve gotten more mature (over the last 10 years or so!) I’ve focused on quality management,” he explains.
“When I came here to work for the engineer’s office, and got into those things here, it was during the course of that, I got given a project. It was a Level II containment laboratory, which means that it has some level of air pressure zones so you can contain toxins and gases. But it had never worked right from day one, they could never get a clean atmosphere and they could never get the air conditioning balanced. There were dirt particles in the air and so on.”
“When it was turned over to the department I was attached to, this facility, the entire area above the ceiling, all the piping and the ductwork, everything was covered in mold. It was damp and a breeding ground for mold colonies,” he recollects.
“The point of this story is that this happened because of just two spots in the building facade, above the false ceiling, where somebody had left out AED50 worth of rockwool insulation. So the desert air came into the building, met the air conditioned air and released its moisture, and that’s the spot where mold can grow.”
With this story, it’s illustrative to note Whistler’s reaction to the problem. While most people would have hired a service company to come by, remove the mold and clean up the place, Whistler decided to eradicate the problem once and for all.
Upon investigating the situation, he realised that there wasn’t anyone in the GCC up to the standards he demanded of himself and his project. Undaunted, the architect decided to switch avatars and become a mold assessor. Taking the initiative, he decided to get his own equipment, which included an infrared camera and air-tightness testing machinery.
“I would have had to sign off on this building, which was my responsibility after a year of work on it and I wanted an infrared camera inspection. I wanted an air-tightness test, but I could not get anybody to do it in the GCC. The closest was somebody in England who wanted tens of thousands of pounds to bring his equipment over. So I decided I was going to get my own camera and equipment and do it myself.”
With this attitude in mind, Whistler took it upon himself to learn how to use the equipment, taking courses both in Europe and America and turning himself into a veritable expert in the field.
“I began to do this kind of thing, because of a couple of things. In 2010, the Estidama code came out and I was in the first graduating group of Estidama PQPs. So when the Estidama code came about and began to talk about the building envelope, and 2010 was when the first edition of the Dubai Green Building Regulations was released, I thought that was something that would start to develop.”
As a result, he began Green Building Solutions two years ago, with the aim of educating and changing the mindset of the building industry when it came looking at the building envelope system.
“I’ve really set my standards high. I want to be known as a company that does high quality work. In a way, it’s not about the testing. Quite often, buildings here are built in a rushed atmosphere, but air tightness isn’t about rushing around in the last two weeks with a caulking gun. It is really about the mindset and looking at the building envelope as a system, just like air-conditioning, irrigation and so on. All the parts of the system have to work together,” Whistler explains.
Fortunately, he says, the response he’s got has been nothing short of fantastic. With the region primed to adopt green building technologies, the market had been extremely receptive to what he’s had to say.
“We’ve been very fortunate and I’ve been getting several calls a week, several RFP’s. I’m doing several thousand Emirati villas, national housing sites. Currently, I’m also doing 10 buildings at Masdar, including the Siemens headquarters,” he adds.
“The Siemens headquarters, there’s a building that’s going for LEED Platinum, the five star Estidama. Fortunately, the project head realised at an early point that it was going to be important to have someone like me on board, and I got involved in the facade design during the detail design. I’m signing off on all the shop drawings, all the drawings that have to do with the facade, all the windows, the glazing, all the details for the panelling go through me first and I sign off on them before anyone else on the team.”
This attention to detail is crucial for him to ensure that a building’s envelope system remains absolutely perfect. This hasn’t always been the case as initially, he was invited to come onto building sites when they were 75% to 80% complete. By then, it’s often too late for any truly effective changes to be made.
“I never like to look at it in a negative way; I do what I can because I’m coming in as a diagnostician. With my 33 years as an architect, I can understand how a building works and I do what I can to help the team see where the problems are. The biggest part of my job is site inspections, which I perform at several points of the construction. If I come in at 75% of the construction, there’s only so much I can do,” he explains.
However, he says that things have changed dramatically, and he hopes the Siemens building can be the flagship of the building envelope movement.
“I’m very optimistic about it I’ve been there for all the testing, for all the site inspections. I issue reports and go to weekly meetings with the team, where I’m able to maintain an independent position. So it’s been really good, they have very high standards, it’s a very interesting building and it’s going to be the largest single air-tightness test in the UAE and it should be ready by December,” he explains.
As such, he points out that other projects would be well served to follow that lead and adopt a stance similar to Siemens.
“There are excellent facade designers out there doing fabulous jobs on these buildings and they perform great in testing, but if you don’t put them together correctly in the field, this is where buildings leak,” he asserts.
“It’s so simple, so why does it happen? Because somebody made a little change somewhere and because they weren’t looking at (the big picture), they’re not looking at the building envelope as a system to keep out air and moisture. The more complex a system, the more chances there are of failure.”
“This is why I’m out there, to educate and create awareness. These issues are real and the evidence is irrefutable. No set of figures can disprove that your window leaks, it’s a reality based thing.”
“There’s more of a growing understanding of these issues. I think what people need to realise is how different these forces are in this extreme climate, the incredible amount of electricity that goes to air conditioning over here and also, thinking about the building envelope as a system rather than an assemblage of parts,” he concludes.