Here for Good
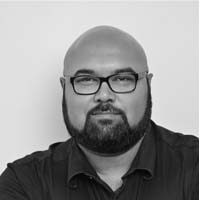
Big Project ME tours the new Standard Chartered headquarters in Dubai and gets a first-hand look at a building that is striving to become a benchmark for green design in the GCC

At first glance, the new Standard Chartered headquarters in Dubai isn’t the most attention grabbing of buildings, but given that it is adjacent to the world’s tallest building, that was something it was always going to struggle with. However, once you get into the building, it becomes immediately apparent that the 18-storey building (ground, four podiums, thirteen office floors and one mechanical floor) is very different from most office buildings in Dubai, if not the entire Middle East.
For starters, the building, which was constructed and fitted out by Brookfield Multiplex, has been designed by Standard Chartered and architects Arif & Binotak with the concept of ‘agile working’ in mind.
Andrew Philips, project manager for the site, explains that the interiors of the building have been explicitly designed to allow workers to be more efficient and productive. They will also be kept in a comfortable, sustainable and green-friendly environment.
“Because there are so many people in the bank who aren’t actually there (on a day-to-day basis), there aren’t permanent desks. If you walk around, you’ll see that there are no drawers in the desk, but everyone gets an individual locker. It’s called agile working and a lot of big companies in the UK are doing it at the moment, it’s meant to promote a more efficient workplace,” he says.
“I don’t know if it’s the first in Dubai, but it’s definitely one of the first,” he continues. “Because you’re saving on space requirements, you’re saving on costs. It has an impact on design and on everything.”
Saeed Al Aabar, a director at AESG, whose firm works with Brookfield Multiplex to achieve a LEED Platinum rating for the project, adds that there had been a number of sustainable measures introduced into the building, especially in regards to water conservation and energy efficiency.
“One of the big drivers for Standard Chartered, with a lot of people working in the building, is that their costs are driven by their staff. So there are a lot of features in here that allow people to work more efficiently, with less sick days,” says Alabbar as he and Philips take Big Project ME on a tour of the headquarters.
“For example, the flooring is green labelled certified, the paints are low VOC, so there’s a very low level of chemicals in all of this. All of this relates to data that shows that you get a lot less sick days (from employees). So they’re able to increase the company’s efficiencies.”
Furthermore, the building incorporates a sophisticated set of systems to ensure that energy wastage is kept to a minimum, with even the glass used in the windows chosen for its high performance and ability to conserve wastage.
“The glass has got a UV value of 1.5, which is very high end. There’s a lot of energy efficiency from that. With the way the glass is set out, 90% of the occupied spaces receive daylight.
There are daylight sensors linked to all the lights. So when it’s sunny, as it would be 345 days of the year here, those lights won’t turn on. If it’s an overcast day, they’d just turn on the right amount, so you haven’t got them on full and people get whatever light is needed at their desk,” Alabbar explains.
In addition, the building has installed extremely efficient water fittings which help reduce the water consumption in the building to 48% below US baselines. Alabbar adds that it was a conscious decision to work to US specifications as they are more stringent than UAE baselines.
“On top of that, all of the water that comes out of taps, because that water is still fairly good quality water, it’s not discharged as sewage. It gets treated through a grey water treatment system, and then all that water is used for flushing,” he says.
One method incorporated into the building was for cooling down fresh air coming into the building, which served the dual purpose of cooling down the interiors, while ensuring fresh air for people in the building, Alabbar said.
“As you can imagine, particularly during the summer, you could be introducing fresh air that’s 50°, and that takes a lot of energy to cool down, particularly if you want to provide a lot of fresh air for the health and well being of your occupants,” he explains.
“Actually, all the exhaust air that has to be ventilated out of the building passes over that fresh air, though they don’t actually make contact. But through a sort of heat exchanger, the fresh air that is coming into the building is already pre-cooled. So rather than introducing 50° air, it can be reduced to 30°-35° before being introduced into the building. And that’s free cooling basically.”
While achieving LEED Platinum status is the ultimate aim, the building has so far been certified as LEED Gold, though both Alabbar and Philip are certain that further improvements will be made to achieved their coveted rating. Brookfield Multiplex has worked on a number of projects around Dubai, but the building is the first one they’ve had complete control over, right from construction to fit out.
Despite completing similar projects in Australia and the UK, working in Dubai brought its own set of challenges.
“It’s actually not that hard if you do all your planning up front. The devil is in the details and that’s where AESG have been brilliant. We built a lot of the structure at night so there were no issues (with noise and logistic complaints in the crowded Burj Khalifa/Emaar Square area). They’ve been planning this for a number of years and they’ve allowed for expansion as well. They knew they wanted breakout zones on a certain percentage of every floor. They’ve been designing it for a very long time and making it all fit, so for us, it was easy actually building it,” Phillips explains.
However, this commitment has meant that there has been additional responsibility for Philips and his team, with the contractor having to install a BMS system, as well as turnkey systems and all the cabling and wiring, in the building. In addition, both BM and AESG will be in charge of testing and commissioning of all the systems in the building, which is a rigorous and time consuming process.
“There were requirements to make sure that the building didn’t leak, and also on the ductwork. There’s a fairly rigorous process to inspecting all of that through to the testing and commissioning phase, to make sure there are no leakages,” says Alabbar. “For the commissioning phase, everything was checked to see if the airflow was through the grills, is the airflow where it’s supposed to be, if it’s not, then you can tell that something has not been programmed right or there’s a leakage in the ducts or something like that.”
Phillips concludes: “That’s all rigorously tested because that’s an area, particularly in this part of the world, where efficiencies are lost,” he points out. “Because things were planned and inspected so well throughout; once you get to the testing phase, it becomes more of a procedure. There are things that are picked up and resolved, but luckily it’s all just small very easy fixes.”