Beneath the surface

Facade developers explain the impact of education on the regional design pool
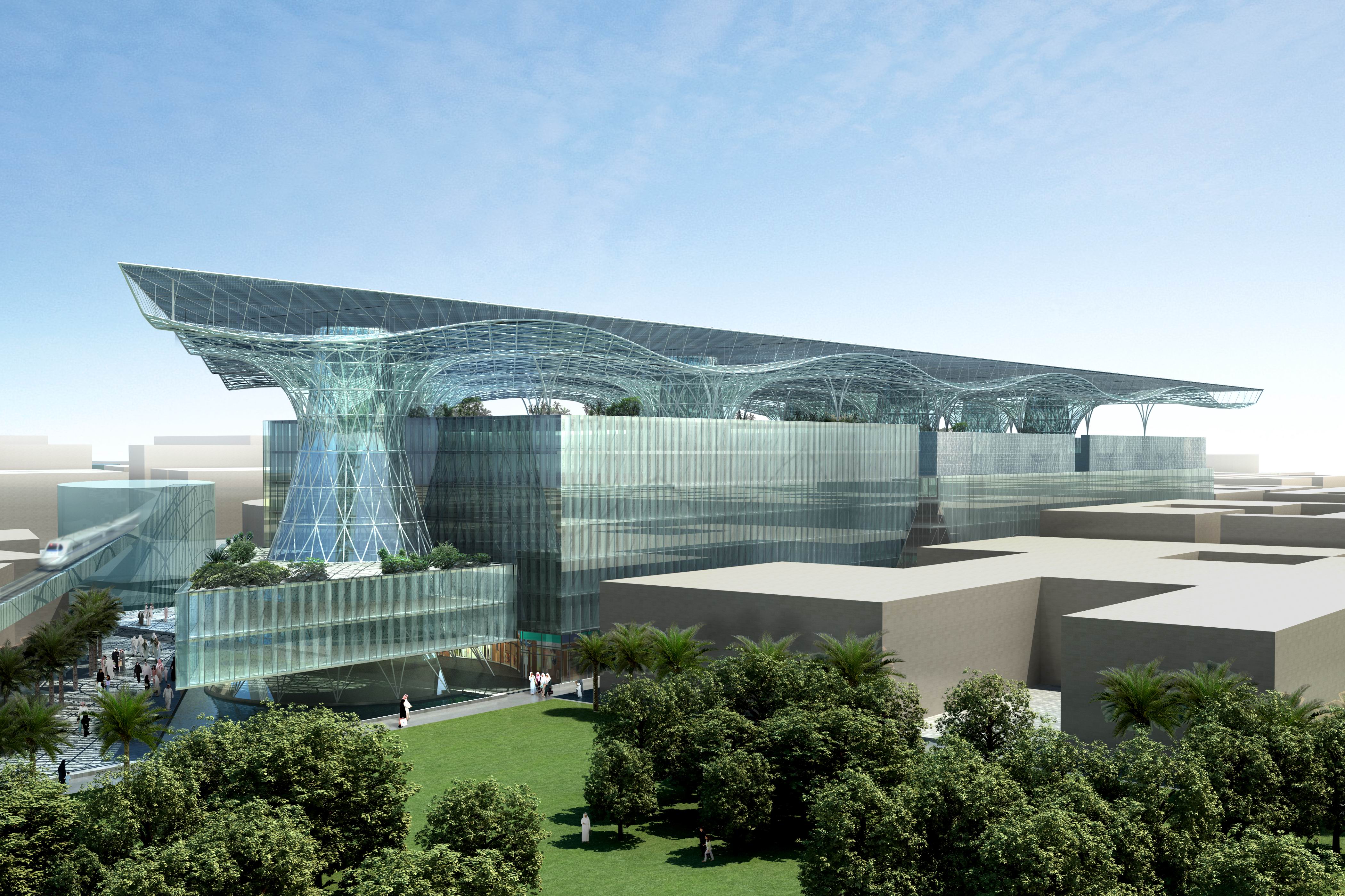
In a region that is striving to make its ‘statement structures’ safer and more sustainable, standards in facade design are becoming an increasingly important element of architecture and construction.
Whether it’s fire safety, thermal insulation or air filtration, the lack of unified local regulations is causing a headache for local manufacturers when it comes to educating clients about the benefits of their products, in a quantifiable way.
In other geographic markets the main benchmark for quality is pegged to the application of design, fire and safety standards. However with comprehensive codes yet to be introduced in the Middle East a melting pot of design influences blends to create an equally diverse collection of standards.
While this is still a more beneficial approach than ignoring all legislation, the end result is a client who is unaware of lifecycle cost savings and the efficiency benefits that could be created for the end user.
“What you have here is a region that, especially in regards to product standards, tends to be very much focused on or influenced by the US or occasionally UK standards, because there is no set remit for local standards,” observes Paul Kinsey, director for Trimo Middle East, who adds the trend causes of misunderstanding for clients when they are left to interpret the impact of differing international codes on lifecycle costs and efficiency of the built asset.
Currently, Trimo is undergoing the soft launch of QBiss Air, ahead of the official launch in Germany in February 2013. Described by the company as a “smart skin”, it can be personalised to mimic glass, stone or ceramic and has an energy efficiency of U=0,17 W/m2K and sound insulation up to 60dB. Both specifications are achieved with only a fraction of the material that would normally be demanded by such results.
The product does away with traditional mineral wool insulation in favour of CO? filled chambers of gas, captured during the manufacturing process. The entire façade is also 96% recyclable.
“The working philosophy of Trimo is sustainability and the environmental impact of our products. All of our focus is behind product that will help future buildings confirm to the best international standards.
“Because we are a European company selling products would wide we are looking at the whole environment not just a micro environment, such as that of the UAE,” Kinsey continues.
But despite the benefits of QBiss, Kinsey says that in the absence of unified standards adn codes, getting the product specified depends on higher levels of education among architects and clients.
For some manufacturers facing the same dilemma, the next best things is endorsement.
The highest such endorsement for efficient building products and solutions currently is Masdar’s Future Build programme, which generally includes a contract win to provide the approved product to the headquarters, institute or city building programmes.
Such products gaining approved Future Build status to date include: Alubond Green, Texlon cladding system, Elastophor, Corro-coat Durasol, EmiCool Classic and Foamglass.
Manufactured by Pitsburgh Corning, Foamglass established a Dubai office in 2006 and has been specified on projects such as the Armed Forces Officer’s Club, Abu Dhabi; the Intercontinental and Crown Plaza Hotel, Dubai Festival City; and Doha’s Texan A&M University, Museum of Islamic Art and New Doha International Airport.
Foamglass is such an effective insulant that the manufacturers claim it can even eliminate the need to upgrade HVAC systems.
“The facade represents the ‘face’ of a building structure,” explains Middle East sales director, Marco Vincenz.
“However, beyond aesthetics it has extremely important functions to fulfil. First it must protect the building substrate against the climatic effects of cold, heat and precipitation. It also must perform acoustically as well as providing fire protection and above all thermal protection,” Vincenz adds.
Perhaps the most astonishing statistic is that a facade can comprise up to 25% of the initial capital expenditure for project developers, but with a disproportionate focus on the construction costs over lifecycle costs, there is little incentive to buy a higher grade – and therefore higher performing – product.
“Better performance translates into improved energy efficiency, which minimises running costs and improves the building environment,” says Alumil managing director, Christopher Chatzigeorgiou.
“Green is definitely the way to go and an increased thermal insulation performance and an overall improved energy efficiency at a competitive product cost is what guides our product development activity,” he adds, referring to the new generation of thermal break systems being developed by the firm, which reduce aluminium use and unitise the curtain wall system.
In agreement, Kinsey adds: “The disadvantage in this region is that everything comes down to the cost of the initial project and if it’s a case of replacing an expensive element only five years down nobody thinks twice.
“The aim now is to bring products to the market that suit architects and clients. And it’s down to companies like us to re-educate the market and tell them there is no need to build how you have done for 20 years,” he concludes.