Moving mountains: How the UAE’s highest road was built

Take the high way: Volvo CE and FAMCO on how building the country’s highest road (up its tallest mountain) was a unique challenge for both man and machinery
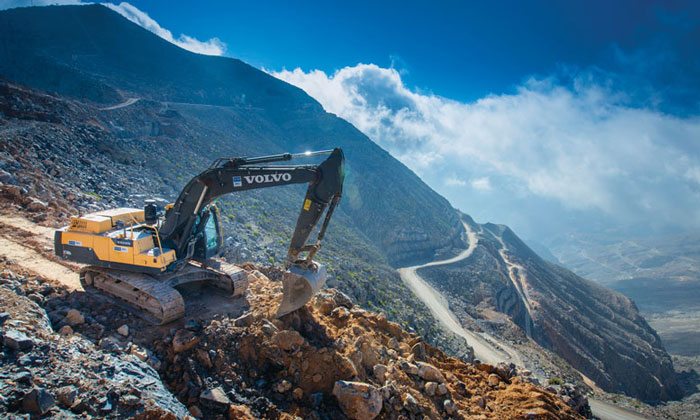
It may be only around a couple of hundred kilometres from bustling Dubai and even fewer from Ras Al Khaimah city, but step onto the 36 kilometres of winding mountain road that leads from the sands of the northern emirate to the heights of the Al Hajar range and you will be forgiven for thinking you have set foot on a different planet.
The undulating dunes first give way to pebbles, rocks and boulders before starting their sharp rise to the 1700m-plus Jebel Jais peak, the UAE’s highest point. Craggy spires of bare and jagged rock, precipitous drops and narrow, forbidding gaps greet you as you roll on to the Jebel Jais mountain road.
The spectacle is at once dramatic, awe-inspiring and frightening, making you wonder at the ferocity of the natural forces that carved up these mountains many eons ago, lifting and arranging the limestone of the area into layers upon layers of torturous folds, twisting entire blocks of bedrock into sheet-like swirls that stack up upon each other to form sharp peaks.
And it is this other-worldly landscape that instantly tells you how challenging a task it must have been to lay down the smooth, culverted, cambered and perfectly graded slope-hugging road that snakes its way up the mountain. This was the task that was accomplished by Yaghoub Alipour Vaezi and his team from General Mechanic Company, the project’s contractors, fortified with an army of Volvo CE equipment backed up by the Swedish giant’s dealer FAMCO, one of the biggest machinery companies in the region.
“This is 36km of some of the most challenging and difficult roadworks you can find,” says Vaezi. “When we compare this road with regular roads and highways, you can see that our work here was tough.
“We started this project in 2005 with an initial time frame of three years for completion. But the estimation by the consultant was way off the mark. We also had to do some extra work, such as protection barriers, bracing walls, etc. So it took around eight years to build the road up to the point it already stands built until now.”
He explains that due to decisions taken by the Ras Al Khaimah government, the project owners, construction stopped at that point for two years. “It has now been resumed and we are busy finishing the work within the allocated 25-month timeframe, which we expect to actually be no more than 22 months. The end of March 2017 is when you can drive all the way to the top of the peak.”
The first big challenge was to create access, Vaezi says. “It is impossible to imagine how difficult it was to access the area at the beginning, and especially transport heavy equipment to the places it was required.
“We had these very narrow and rough tracks back then to move on with the Volvo trucks. Sometimes one or more wheels were hanging off the road in midair over a sheer drop. You can imagine how perilous it can be when some of your wheels are not in contact with the road surface. And it wasn’t as if the drop on the side was just a couple of metres. Instead, if your equipment rolled off the road, the plunge would probably be about a hundred metres and you could kiss both operator and the machine good bye.”
Another challenge was the remoteness of the terrain, he adds. “Transporting all the necessary things for the project up to the site was difficult and costly. And if an equipment broke down on site, it was a completely different story compared to building something in a city. If you are in Dubai you can just go to the dealer and get what you want, but not here.”
Proud achievement
Enter Volvo and FAMCO. The powerhouse equipment dealer provided 50 pieces of Volvo construction equipment to the project and 33 Volvo trucks. More importantly, it provided a tremendous level of back-up service to keep the machines running in trying conditions.
Nigel Johnson, senior managing director, FAMCO Group, is justifiably proud of his organisation’s contribution in the project. The project also had significant importance for FAMCO, as it was the first project undertaken by the company’s Rental & Used Equipment Division at a time when equipment rental was a new thing for the contractors in the market.
“Our Rental & Used Equipment Division was a major option for the contractor and provided him with solutions to meet his requirement for a large fleet of machinery and trucks for as critical and challenging a project as the Jebel Jais mountain road,” Johnson says.
“FAMCO provided the contractor with the much needed resources for this project and helped him save capital expenditure which reflected positively on the project’s budget and delivery timelines. FAMCO not only provided the machinery and trucks, but we also provided the operators and drivers, outstanding aftersales support, the flexibility of replacing any unit with a supporting one to ensure optimum uptime and smooth flow of operations.
“All these factors, as well as FAMCO’s leading position in the market as a solution provider for construction equipment and commercial vehicles, played a key role why the contractor selected FAMCO to support him in this challenging and iconic project.”
Speaking about the equipment supplied by FAMCO in the project, Johnson added: “For earth moving and excavation we supplied several pieces of Volvo’s EC700, EC480, EC460, EC380, EC360, EC290 and EC210crawler excavators. The excavated material was hauled away by Volvo’s A35F and A35E articulated haulers, which one could have found being loaded by Volvo’s L120F and L180G wheel loaders.
“The fleet of 33 Volvo trucks we provided to the project comprised mainly the FMX370 Tippers, which were used for a variety of transport tasks, including carrying excavated materials away for being dumped off-site. And when the mountain was carved and a path was finally cleared, it was Volvo’s SD110 soil compactor that helped to lay the smooth road you can find up there today.”
There were challenges aplenty on the job, Johnson adds. “The remote location far from supply points in the cities and the limited access points around the mountain were some of the problems. Even more challenging was the extreme and inaccessible terrain, the unpredictable and harsh weather conditions such as snow, fog and blowing winds, and the surrounding hazards such as the loose rocks and rock avalanches at the mountain.”
This necessitated a great effort in site support and service, and Johnson adds: “FAMCO provided ‘in-house’ high quality Operator/Driver 24/7 support, plus 24/7 service and site support and trained supervisors for ‘on the job’ instruction and production expertise. Additionally, we provided our own experienced machine operators and truck drivers who contributed towards eliminating any major accident in the project’s duration, ensured timely delivery and helped to reduce the contractor’s operational costs.”
Feather in its cap
As the prime supplier of machinery to the project, Volvo CE, too, considers the Jebel Jais road a feather in its cap. The machinery giant’s involvement in the project is made even sweeter on account of the trouble-free and safe performance of the equipment it provided as the contractor’s first choice.
“It is surely an iconic project and a badge of honor for us to have been part of building the UAE’s highest road,” says Shahir El Essawy, business director, Volvo CE.
“Safety has always been one of our core values. Our vision is to have zero accidents with Volvo machines and we incorporate safety into each and every aspect of design and operation in our machines. This clearly puts our machines as best suited for such tough conditions with extremely narrow haul roads and high altitudes with big drops. We are proud to say that we have gone through this project without any incidents.
“Once again this project clearly confirms to us the importance of continuing to incorporate safety in all aspects from design to production. It was also a testament to the great partnership we have with FAMCO and how we teamed up successfully on this project. FAMCO had set up great aftersales support on site at this remote location, and that has definitely been a key element in our joint success.”
For Vaezi, the reasons to opt for Volvo were simple ones. “We chose to go for Volvo because of their technical specifications and reliability. The project used mainly Volvo machinery, some of which we purchased and some of which we rented from FAMCO’s rental section,” he says.
“Being in a remote location far from civilisation, we had to be as self-sufficient in our operations as we could. This included the upkeep of the machines we were using and so we set up a workshop here on-site to do most of the routine maintenance and regular repair work. Of course we need parts and sometimes we need the suppliers’ technical team to be available here because our workshop cannot solve some issues.
“With Volvo machinery we just had to call FAMCO and they sent their technicians, who solved our problems quickly. When the problems were big, the machinery were taken away to FAMCO’s workshop, but such occasion were few and far between.”
Another challenge for the machinery and operators was the weather. It gets densely foggy in winter on the mountain, reducing visibility, and rains often make the bad terrain slippery and worse, Vaezi adds.
“In the winters it gets bitterly cold and starting the machines is not easy. But the machines proved reliable and enabled us to complete the first and major part of this AED350m project. And we continue to push forward towards an early completion of the remainder of the road.”
This project is important to the whole of the UAE, the project manager feels, because it is a unique one.
“This is the most visited area in the country outside of the cities because it is special in terms of the landscape, the weather and the sights it offers,” Vaezi says. “Also, it is all very well to say an area belongs to the country but if you cannot reach it, it’s as good as not being there. With this road, we have provided access to an area of the country that was inaccessible. This road has actually made the UAE bigger.”
Volvo F-Series articulated haulers
Hauling away tons of excavated rock, debris and blasted mountainside from the Jebel Jais road construction site, Volvo’s F-series articulated haulers have proven to be among the star performers of the project.
The trucks were indispensable for the work. As project manager Yaghoub Alipour Vaezi puts it: “We could not have done without the Volvo articulated haulers. We initially also brought in some rigid heavy dumper trucks, but they did not prove to be so useful. The biggest gain in using the Volvo articulated haulers, apart, of course, from their power and hauling capacity, was the maneouvrability they enjoyed with their articulating bodies.”
And indeed, one look at the terrain the haulers had to work in drives home this point. Clearing a path on the side of the mountain requires hugging its contours and snaking around it bends, something the articulated hauler’s design has proven to be adept at.
“At places the gradient was more than 30 degrees. Our normal trucks or six-axle trucks were not able to pass these areas but the articulated hauler was perfect and allowed us to work in this challenging terrain,” Vaezi adds.
When Volvo CE’s articulated hauler first hit the market in 1966, it was a ground breaking new concept. The company has continued to revolutionise its articulated hauler with the F-Series, which includes features designed to improve comfort and productivity. The robust and reliable F-Series articulated haulers include, among others, the A25F, A30F, A35FFS, A40F, A40FFS and the A35F, which was used in the Jebel Jais project. The range is suited to a wide variety of applications in quarrying, mining and earthmoving.
Featuring advanced technology and built on decades of experience, the powerful Volvo engine delivers a combination of high performance and low fuel consumption. The Volvo drivetrain and a unique inline drop box designed for high ground clearance are purpose-built to ensure perfect harmony and optimised performance. The drivetrain’s unique design delivers high rim pull, lowers fuel consumption and provides reliability in heavy-duty applications.
The A35F – and others in the series – features a proven concept of oil-cooled wet multiple disc brakes, reducing maintenance costs and increase uptime, even on muddy or dusty job sites, such as Jebel Jais. The retardation system controls downhill hauling speeds using wheel brakes and the Volvo engine brake – important features when building a mountain road.
To keep the F-Series surefooted in a treacherous job site such as the mountain, automatic traction control (ATC) and unique differential locks came as standard. The ATC system automatically switches between unique drive combinations of 6×6 and 6×4 to ensure lower fuel consumption or maximum traction when needed. If necessary, all differentials can be 100% locked, causing all wheels to rotate at the same speed for maximised traction in slippery conditions.
The A35F, A35F FS, A40F and A40F FS can be equipped with Volvo’s award-winning onboard weighing system, which allows for precise machine productivity monitoring, helping to optimise payload and minimise wear, tyre damage and high fuel consumption.
The maintenance-free rotating hitch that connects tractor to trailer enables high ground clearance, boosting accessibility and drivability in tough conditions and maximising uptime.
The centrally positioned cab gives the operator a commanding view of the job site, vital for not falling off the sheer cliffs of Jebel Jais while working on the project.
The F-Series comes fitted with CareTrack, Volvo CE’s telematics system, which remotely provides machine information. The Contronics system continuously monitors fluid levels and relays diagnostic information to a screen in the cab, alerting the operator to problems early on – another vital safety measure in a project where danger was a constant companion.
Volvo excavators
Among the army of Volvo CE excavators that worked on the Jebel Jais project were the EC700, EC480, EC460 and EC380, EC290 and EC210.
“The Volvo 70t excavators that FAMCO provided us proved to be ideal for the project,” says project manager Yaghoub Alipour Vaezi. ”They were safe because first of all they were in perfect condition. When a machine has a problem then a lot of other problems usually follow.
“For the excavators we chose rock buckets, suitable for handling the loose rock and boulders that needed to be cleared. The buckets measured four cubic metres in capacity, so our trucks had a busy time keeping up. Only two bucket-fulls and they were fully loaded.”
The EC700D from Volvo CE, which was the backbone of the excavation work for the Jebel Jais road project, combines a robust design with a powerful engine for enhanced performance and a lower total cost of ownership when working in a range of heavy-duty applications.
The EC700D is built to deliver superior productivity and efficiency in a variety of heavy construction applications. Equipped with a Volvo D16 Tier 3 engine, this machine provides increased horsepower and fuel efficiency in combination with a robust design to ensure a low total cost of ownership.
Working in harmony with it is an improved, Volvo-designed electro-hydraulic system, which uses intelligent technology to control on-demand flow and reduce internal losses in the hydraulic circuit.
The excavator incorporates Volvo’s unique integrated work mode systems, through which operators can choose from a range of modes for optimum performance.
When the operator selects the best work mode for the task at hand – I (idle), F (fine), G (General), H (Heavy) and P (Power) – the rpm is already set for maximum efficiency.
A comfortable, low noise cab with adjustable seat increases operator efficiency to further improve production. The Volvo cab boasts superior visibility from large expanses of front and side glass with slim cab pillars, and the spacious environment provides ample storage and leg room.
The EC700D is equipped with efficient technology to ensure outstanding digging force in any application. With improved stability and tractive force the machine offers improved cycle times for outstanding performance.
This excavator’s constant high system pressure delivers greater digging force, which was vital to carve out the hard limestone in the mountains.
For more power, better productivity and increased manoeuvrability, the high system pressure and durable track ensure impressive tractive force when climbing gradients and travelling over unstable ground. A wider track gauge and heavier counterweight improve stability even when working in challenging environments.
It is no wonder then that Vaezi is all praise for the excavator.
Volvo FMX truck
The Jebel Jais mountain road project was completed with the help of the Volvo FMX 6X4 rigid truck, equipped with the I-Shift automated gearbox.
“This innovative gearbox is the first transmission of its kind which has been specifically designed for heavy long-haulage and construction applications,” says Jan-Erik Thoren, business team director, Volvo Trucks Middle East.
“The truck has high ground clearance to operate in tough environments and a comfortable cabin for the drivers, which made the job less physically draining and allowed them to drive for longer.”
For eight years, a fleet of 33 Volvo FMX trucks worked round-the-clock to carry more than 5.5 million cubic metres of rocks and aggregates to build the 36km road. Despite challenges such as the rugged terrain, steep slopes, loose rocks and extreme weather conditions, the fleet of Volvo FMX trucks completed the ambitious project without any major breakdowns or accidents.
“The Volvo FMX is designed for tough construction operations with tailor-made specifications for such extreme conditions. The truck has also been designed for optimised fuel consumption and maximum uptime, which is essential for a project of this size,” Thoren says.
Ahead of its arrival in the Middle East, the FMX was extensively tested in the region to ensure that it can tackle some of the roughest, most demanding off-road conditions in the world.
“We were confident that this model would provide an unbeatable transport solution for this project and stand out from competitors. We are very proud to be a part of this development and to see it meet completion after eight years,” he adds.