Bucket crushers offer on-site recycling capabilities for contractors
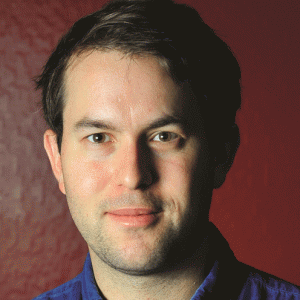
Compact but highly productive, excavator-mounted crusher buckets allow contractors to recycle construction waste on-site

When a contractor is faced with a large amount of construction waste on a project site, the traditional methods of dealing with it can be ineffective or costly.
Bringing in a mobile crusher is expensive and requires a considerable volume of waste to be cost-effective. Trucking the waste away to be dumped or recycled (at plants such as Abu Dhabi’s Al Dhafra Construction and Demolition Recycling Facility) remains expensive, with a cost per tonne to shift, as well as environmentally unfriendly with extra heavy vehicle road traffic. A contractor can also potentially reuse the waste on-site, but if they can’t process it effectively then they are unable to use it for its full potential, which may result in buying extra aggregates where properly recycled material might be suitable.
Hydraulically powered bucket crushers are viable, cost-effective and increasingly popular in the region. They are offered by a number of manufacturers in a range of sizes, and the larger buckets can crush in excess of 100 tonnes per hour (t/h) of material. The excavator-mounted attachments can be used on any hydraulic excavator, and with the larger-than-average size of excavators in the GCC, contractors are able to easily run large-capacity bucket crushers. For recycling applications, these are normally paired with a screening attachment, available from most firms who produce the crusher attachments.
The first to enter the Middle East market was MB Crusher eight years ago, and the company is a familiar sight at major regional trade fairs. Despite it being a novel concept, when contractors first encounter a bucket crusher they are quick to understand the benefits, says Najmeddine Sahraoui, area manager at MB Crusher.
Customers include civil construction contractors, demolition workers, recycling operations and quarry operators. They’re also favoured by utilities contractors, because the excavated material can be crushed and used to bed in pipes. “The idea is to save money, time, and to recycle the material you take from the ground by crushing and screening.”
There is increased demand from customers who want to carry out recycling on-site, especially concrete. Sahraoui that one customer in Kuwait uses their crushers and screens to produce aggregate for reuse or sale to other contractors.
Its relatively low unit price means it is especially popular with smaller contractors, explains Sahraoui. The company also has a line of crushing and screening buckets that can be used on smaller equipment, such as skid steer loaders, backhoes and mini-excavators. Despite their smaller size, these offer extremely high standards of productivity. The range is entirely produced in their factory in Italy, using high-strength Hardox steel.
A newer entrant to the GCC market is Hartl Crushers, which in October 2014 signed an exclusive distribution agreement with FAMCO for the Gulf region. Dominik Hartl, the company’s CEO, says he’s excited about market demand in the Middle East. “Potential in the market is enormous. With this strong relationship with FAMCO, we expect a long-term relationship.”
The Austrian company has a long history of providing equipment to the quarry industry, explains Hartl, grandson of the company’s founder. His father and uncle were innovators, developing in 1977 a crusher unit on wheels in response to the needs of their own quarry. With a high throughput rate, the Powercrusher was marketed as the world’s first mobile crusher unit. This was followed by a fully mobile recycling plant for concrete in 1980, and the business focus shifted to manufacturing quarry equipment instead of quarrying. Today, Hartl Crusher sells a range of bucket crushers and screens, as well as a recently launched mobile screen plant. With four different bucket crushers, the HBC 950 and HBC 1250 are the two largest in the range, best suited to the GCC region due to the preference for larger excavators. The HBC 950 and HBC 1250 crusher buckets have production capacity of 35-85t/h and 50-110 t/h respectively; production capacities vary based on material, feet size and gap setting. For gypsum, production for the HBC 1250 can be up to 128 t/h. In practical terms, this means a single excavator can crush up to 1,000 tonnes per day.
Hartl says the chief benefits of the crusher bucket are the ability to crush material at a far lower cost per tonne than with tracked mobile plants, and the fact that it can be used on remote job-sites where hauling virgin aggregates would incur extra costs.
But there are obstacles to adoption. Some contractors are reluctant to use recycled material if they are unfamiliar with its application, says Hartl. On this front, he says their product is well-suited since it produces the cubical material needed for construction work such as sub-base. The parallel jaw-crushing action of competitor crusher buckets can result in a flat or flakey material shape. By contrast, the Hartl crusher buckets use a patented Quattro or figure-8 movement, with the jaw crushing higher on the face, allowing larger stones to be crushed and higher through-put. As the material moves down the chamber, it is worked a second time, resulting in the desired cubical shape.
The origins of the Quattro movement go back 40 years, when the company used it for larger jaw crushers. However, its function is more important on the bucket crushers, since the crusher only touches the material a single time, and there is no chance to shape the material using the multi-stage process that is possible with larger crushers.
Contractors who see the output immediately recognise the quality of the material, explains Hartl. “It is very important for contractors that the material is produced with a top-quality, very cubical shape. That’s their key to success, and the Quattro movement can provide this better than any other motion on the market.”
The global market for crusher buckets is growing, though there are regional differences. In Europe, the focus is on recycling, while in Latin America and the Far East, it is aggregate production out of small quarries and borrow pits. But the technology is also enabling recycling opportunities in markets where it has not previously been common, says Hartl.
Apart from demand in civil construction, MB Crusher has seen good business from quarry operators in the region, who like being able to use it in areas where it would be difficult to place a mobile crusher, or with smaller volumes. In these cases, crushing with an attachment avoids the cost and time of using trucks to transport material to the primary crusher.
The quality of material produced by a crusher bucket is “more or less as good” as that produced from a static crusher, says Sahraoui, and when operators realise they can eliminate transport costs, the business case is pretty clear. “A bucket crusher can never replace the mobile or the fixed crusher, but it’s an instrument that can be used alongside existing plants,” he explains.
MB claims to sell the largest bucket crusher in the world, the BF150.10, the ‘Records Bucket’. This is matched to excavators 70t and larger, and has a total weight of over 10t. But this hefty specification is more than compensated for by its output: with a load capacity of 2.30m3, it can produce 120m3 per hour. The firm has sold a number of units to Saudi Arabia, the only country in the GCC which has bought the BF150.10, but is now in discussion with customers in Kuwait and Qatar, says Sahraoui.
Sahraoui expects demand in the region to continue to grow, based on the number of requests for quotations they receive. “Our forecast for the region is positive; we expect to strengthen our relationships with our customers and partners.”
GCC recycling round-up
Abu Dhabi is leading the way when it comes to recycling of construction and demolition waste. There are a number of factors in its favour, including government vision and the fact that its distance from the quarries in the north of the UAE means that cost per tonne of virgin aggregates is higher, making recycled material more price-competitive.
The Abu Dhabi municipality mandates that certain large projects must source at least 40% of aggregate from recycled material. The Etihad Rail project is one prominent example. it sourced a significant volume of material from the Al Dhafra recycling plant for use as sub base for the rail bed. The material meets the specifications set by the municipality.
Managed by Habtoor Leighton Group (HLG), the Al Dhafra facility can process 5,000-7,000t of material per shift, and the product performs as well, if not better than, virgin natural materials. It has been specified as suitable for use as road base aggregates and on structured and non-structured backfill projects.
Abu Dhabi’s Estidama rating programme also requires contractors to have a waste management plan on-site, and to use material on-site or otherwise prevent it going to a landfill. The higher the Estidama rating, the greater the volume of material which must be diverted, which encourages the use of on-site equipment to process material, either bucket crushers or larger mobile crushers, depending on material volumes. One prominent project, the recently opened Yas Mall, achieved a Two Pearl rating, requiring it to divert at least 70% of the waste it produced from the landfill. In practice, 75% of waste was diverted during the construction phase, a process which included the crushing and screening of more than 39,000t of concrete on-site (the high volume was due to a change in construction plans that saw many elements on-site demolished).
Dubai naturally has a record as a major producer of CDW. At the peak of construction in 2008, Dubai Municipality calculated that the emirate was producing 30,000t of construction and demolition waste daily. Things have certainly improved since then, with the Green Building Regulations of 2012 requiring that recycled content must account for at least 5% of material used on a project, while at least 50% of the waste created must be diverted from landfills.
Qatar has one of the highest levels of per capita waste generation in the world, and is seeking to scale up its use of recycled materials in the construction and demolition sector. A report last year from the Qatar Development Bank (QDB) estimated that the annual revenue potential from construction and demolition debris was $104m (QR387m). This can only be expected to rise as construction projects continue, and recycling has extra incentives in Qatar since it has high raw material costs, much of which must be imported through a busy port.
Meanwhile, on-site recycling helps reduce heavy vehicle traffic and thus general road congestion. Last year, an official from the Ministry of Environment, Dr Khaled Hassan, said that in order to ensure sustainable supply of sand and other raw materials, Qatar is recycling a huge amount of excavation waste. About 20% of concrete waste recycled, and this may rise to 50%. “Qatar is also working to find alternatives of sand, gabbro and other raw materials to reduce its dependence on imports,” said Hassan.
Saudi Arabia currently has no systemic requirement for the recycling of construction and demolition waste (to this author’s knowledge). But with the country’s size and many remote job-sites, the demand for on-site recycling is driven by high transport costs for hauling virgin aggregates over large distances. Projects that feature extensive use of excavators with breakers to level rocky ground in preparation for civil construction projects are good candidates for the use of bucket crushers; these sites typically require a small crusher to process the material, but moving the rock to the crusher is time-consuming and requires trucks or haulers. Excavators using crusher buckets can perform the same function.