Safety first in Gulf construction
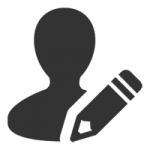
How contractors and consultants are working to improve the GCC’s safety record
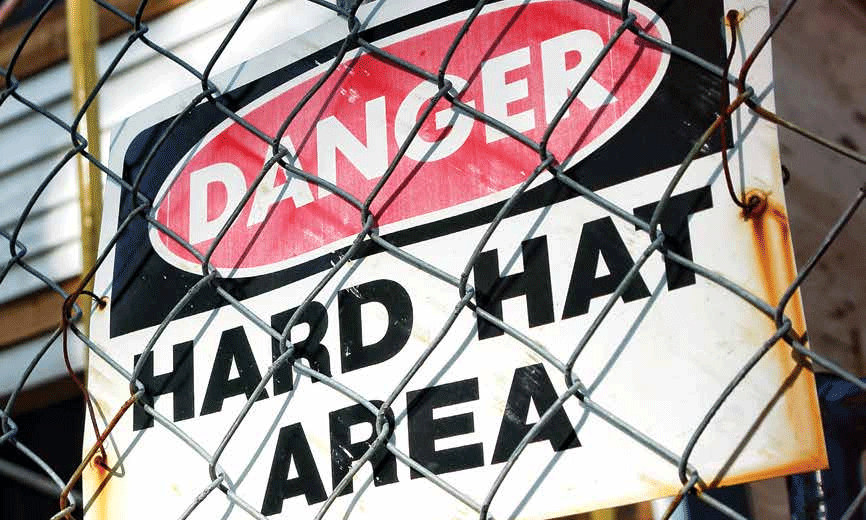
The health and safety of workers on construction sites has always been a hot-button issue in the UAE and GCC. The region has been subject to intense scrutiny from international entities for failing to pay adequate attention to worker welfare. FIFA president Sepp Blatter admitted last month that “more must be done in Qatar to ensure uniformly fair working conditions for all” on the 2022 World Cup construction sites, although some progress had been made.
Closer to home, Abu Dhabi developer TDIC has also come under fire for mistreatment of workers on Saadiyat Island projects, including the upcoming Guggenheim Abu Dhabi and New York University’s campus in the capital. Allegations made in a Human Rights Watch report released in February [see below] were strongly denied by the developer, which rejected what it called “unfounded conclusions” by the New York-based entity.
READ MORE: Health concerns of UAE construction workers ‘need more attention’
OPINION: Mental health of construction workers needs more thought
However, despite the dubious reputation of construction projects when it comes to worker welfare, consultants and contractors say major gains have been made in the UAE and the region in terms of health and safety.
“I’ve been in the UAE for eight years now, and I feel that there’s been some dramatic improvements in health and safety standards across the region. And a lot of that is being driven by government,” says Rob Cooling, director of Health & Safety Middle East at WSP.
John Milligan, QHSE Director at WS Atkins, has also been working in the Middle East for eight years and notes that he’s seen a steady improvement. “Part of the reasons for that is the maturing of regulatory enforcement,” he says.
The statistics might indeed indicate an improvement. Last year, The National reported that there was a 32% reduction in the number of deaths in Abu Dhabi caused by work at height between May 2012 and May 2013. The decline was observed following the Height Aware safety programme, which aimed to highlight injuries in sectors like construction and oil and gas.
Big Project ME wondered, therefore, about the most common hazards and challenges that safety professionals have to deal with on-site, and how consultants and contractors create a culture of safety on projects.
Commonly faced hazards
The most fatal hazards, Cooling says, are lifting operations, work at height, excavation work and vehicle movement on sites. “We have a lot of cranes on-site doing some major lifting operations, and the quality and the testing of that equipment is a common issue that we’re having to face. So in terms of our fatal hazards it gets the most attention.”
Moreover, in a country known for delivering projects at a fast pace, on-site accidents can also be chalked up to a lack of planning and tight timeframes, Cooling points out. “In the construction industry, there’s always a lot of pressure to finish projects quickly and not always sufficient emphasis is given to planning.” Health and safety requirements need to be made clear from the onset of a project in order to address this, he adds.
READ MORE: Health concerns of UAE construction workers ‘need more attention’
OPINION: Mental health of construction workers needs more thought
Apart from obviously dangerous work like working at height or lifting operations, a common hazard across sites is something typically overlooked: housekeeping.
“The common problems on construction sites, people refer to them as housekeeping and keeping the site organised,” says Peter Jolly, director – Health, Safety & Environment at Al Jaber Group. “Whereas really, when you look at the housekeeping problems, you see other things which aren’t even housekeeping in terms of keeping the place tidy but they’re actual hazards: fire hazards, trip-and-slip hazards, bits of wood with nails in it, shards with metal.”
Paying attention to perceived housekeeping problems that are really hazards not only makes the site safer, it also organises it, he adds. “An organised site is an efficient site, not just a safe site, and so that improves productivity.”
David Sweed, regional SHEQ & Construction manager, Mouchel, echoes Jolly’s comments about the link between safety and productivity. “In truth, a safe site is more efficient than an unsafe site. So the perception of safety being a hindrance, of safety slowing production, of safety costing money, is really not the truth. If you see a site that is safe, you know behind it that it’s well-run, it’s well-managed and producing a good product.”
Moreover, Sweed notes, health and safety professionals can face a host of challenges on remote sites where easy access to healthcare facilities isn’t available. An example of this, he says, is one of Mouchel’s projects, the Um Al Aish liquefied petroleum gas filling plant in Kuwait, 100km from Kuwait City. From day one of the project, a trained nurse and a medical centre were available within the compound or confines of the site.
“When activities of high risk have been undertaken, then we’ve been able to arrange for a paramedic and an ambulance to be on-site, to be there in case there was a serious incident. If we’ve been doing quite a dangerous activity, such as confined spaces entry, then we need to have the right emergency rescue teams in place with appropriate equipment so that people can be safely removed if there was an accident.”
Training and compliance
While governments may do their bit in providing regulations, it is generally up to consultants and contractors to create awareness, uphold safety standards on site and ensure rules are being followed. “We do spend a lot of our time actually trying to raise health and safety awareness amongst contractors. So we get involved in providing regular toolbox talks, or short training sessions on health and safety topics,” Cooling says.
READ MORE: Health concerns of UAE construction workers ‘need more attention’
OPINION: Mental health of construction workers needs more thought
But with multicultural staff on projects, training often needs to be adapted to be understood by all. “Quite often with the guys that are on-site, they’ll speak different languages. We deliver briefing in languages that are obviously appropriate for the target audience, to make sure that the message is understood.”
Training, however, needs to go hand in hand with enforcement, the consultants note. In order to ensure compliance with safety standards, Milligan says Atkins has introduced a concept called “consent to work” on its projects, wherein contractors have to go through a two-step approval process to carry out construction activity. This is done by emphasising the importance of the method statement, a document often not given its due by contractors.
“Method statements are produced by contractors to describe the methodology for a particular aspect of the construction. Commonly, contractors produce these method statements just for approval, and then they neatly get filed away. They’re no longer used as a reference document during construction,” he says.
In Atkins’ consent to work procedure, the contractor needs to submit the method statement for prior safety approval to Atkins and then demonstrate that he can build according to the document.
“If we find that a contractor isn’t observing their method statement, then we will withdraw consent to work for all of the same activities right across the whole construction site, which would be a complete nightmare. For instance, if it was block-laying on a high-rise and all of a sudden we stopped all blocklaying just based on a single infringement, then you could see that it would have a considerable impact on the contractor.”
READ MORE: Health concerns of UAE construction workers ‘need more attention’
OPINION: Mental health of construction workers needs more thought
In order to overcome language barriers, Atkins also advises contractors to develop method statements with lots of photographs, he says. Moreover, the firm has developed a method of classifying contractors according to maturity levels and refuses to work with contractors below a certain level of competence.
“What we’ve introduced in Atkins is a method for classifying contractors according to [their] level of maturity. And there are four elements to that. So the most mature of our contractors we classify as 1, and then it runs to 2A, 2B and 3. The Tier 3 contractors are those contractors that we as a company have decided that we will not engage with,” he says, adding that Atkins has put in controls in the bidding process to ensure this.
“If we are sufficiently assured that contractor is not capable of implementing and sustaining the health and safety management system for the life of a project, then there’s clearly going to be risk to their own employees and that will impact us massively,” he adds, defending the policy. “It’s not just about reputation loss. We don’t want our people working on a project where people are either being seriously injured or have died.”
However, he notes that the firm might consider working with Tier 3 contractors if there were sufficient assurances from the client that the contractor would improve, along with additional resources available to Atkins to support the contractor’s safety management.
While established or international construction firms may have a sound HSE policy in place, smaller players like local contractors or subcontractors may not. This is less of a problem than it used to be, but Jolly says disparities still exist. “Most of the time we have to look at costs, and therefore we could lean towards cheaper contractors. So basically the code of practice is if you don’t have a safety policy or if your safety policy is inadequate, then you use ours. It’s as simple as that.”
READ MORE: Health concerns of UAE construction workers ‘need more attention’
OPINION: Mental health of construction workers needs more thought
“We link that to the contract, and if they don’t provide or issue standard protective equipment, or they don’t provide enough supervision, then we can bring it in and we can back-charge them for it,” he adds.
The next step
When asked what improvements he would like to see in safety standards, Cooling points out that while legislation in the UAE – particularly in Dubai and Abu Dhabi – is detailed and prescriptive, the next step is proper enforcement. Moreover, HSE aspects of a project need to be taken into account right from the start.
“It’s about getting health and safety embedded in the earliest phases of a project. Because when it actually comes around to the construction phase, typically that’s often too late. A lot of our focus is how you get health and safety embedded in the planning and particularly the design phase of projects, and how to mitigate health and safety risks when it comes to construction.”
Additionally, despite the range of challenges that HSE professionals face, one of the key obstacles to be overcome is the notion that health and safety is only the responsibility of a HSE team, Cooling concludes.
“Everybody has a responsibility for health and safety, but in particular project managers should be managing health and safety in the same way that they manage costs, that they manage schedules, and manage other aspects of a project. I think that’s an important point.”
READ MORE: Health concerns of UAE construction workers ‘need more attention’
OPINION: Mental health of construction workers needs more thought
Long-term health of workers needs more attention
While strides have been made in improving safety standards across construction sites in the UAE, the health aspect of health and safety has yet to receive adequate attention. “The focus still is very much on safety as opposed to health, so I feel that quite often, and particularly in construction, there is a great deal of attention that’s given to things like the fatal hazards [like] working at height that kills a lot of people every year,” Cooling says.
“But I think the next progression really is to focus more on worker health and worker health promotion and the occupational health hazards, things like noise, heat and humidity, occupational fatigue, stress, that are probably not given at the moment the attention that they deserve compared to safety.”
The fact that several health issues associated with construction work tend to only show up over the long term adds to the problem, he notes. “The tendency is to focus on worker safety and I think quite often the challenge is around latency, that these health effects might not be apparent until later years in the life of the worker. So sometimes it can be a bit of a challenge to focus on things that might affect workers in the future when they may be back in their own country, as opposed to things that are here and now and could cause serious injury today.”
Milligan echoes Cooling’s comments, stressing the role of pre-employment screenings in ensuring the health of workers as well as preventing the outbreak of contagious diseases. “What we’ve observed over time is that some of our mature contractors are already providing pre-employment screenings for workers. Most of the countries in the GCC where we work, they have good controls in place, especially with communicable or high-risk diseases,” he says, though he admits that worker health has “received scant attention in the past”. “We are expecting improvement over the coming years as the market matures, but we’re not seeing enough of it at the moment.”
READ MORE: Health concerns of UAE construction workers ‘need more attention’
OPINION: Mental health of construction workers needs more thought
TDIC vs. HRW: The battle over workers’ rights
In February, New York-based Human Rights Watch (HRW) issued a report highlighting instances of worker abuse that it said were still prevalent on projects on Abu Dhabi’s Saadiyat Island. “Nearly five years after Human Rights Watch first revealed systematic human rights violations of migrant workers on Abu Dhabi’s Saadiyat Island, there remain serious concerns about violations of workers’ rights on the island,” the report said. According to HRW, some employers continued to withhold wages and benefits from workers, failed to reimburse recruiting fees, confiscated worker passports and housed employees in substandard accommodations.
Abu Dhabi’s Tourism Development and Investment Company (TDIC), however, was quick to deny the claims and issued a statement refuting the allegations.
“TDIC rejects the report’s unfounded conclusions, which are outdated and based on unknown methodologies. We have established a comprehensive Employment Practices Policy outlining the standards required from the companies working on our projects, and laying out penalties for those found to be in breach of any aspect,” the developer said.
HRW, however, claims these penalties are simply not enough. “The penalties for contractors and subcontractors are so small – at most 1% of the contract value – that they are unlikely to have a significant deterrent effect,” the body said.
Meanwhile, TDIC insists that many of the issues previously raised have been addressed. The developer has established the Saadiyat Accommodation Village to house workers, and says that all workers have access to their passports and medical insurance. Grievance procedures have also been put in place for workers to address complaints, it said.
While HRW noted that progress has been made in the UAE overall with regard to labour law reform, it called upon international organisations involved in Saadiyat projects, like the Solomon R. Guggenheim Foundation and New York University, to “make their continued engagement… dependent on public commitments by the UAE government authorities and the EAA and TDIC to ensure that workers are protected from abuses.”
READ MORE: Health concerns of UAE construction workers ‘need more attention’
OPINION: Mental health of construction workers needs more thought