Get to know: Chris Wan, design manager at Masdar City
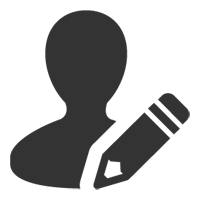
Middle East Consultant gets to know: Chris Wan, design manager at Masdar City
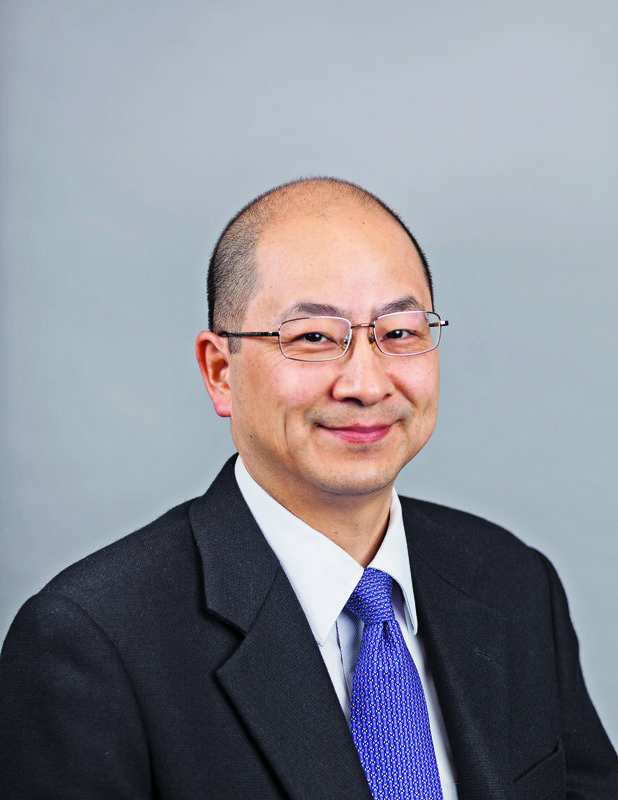
For the last six years, Chris Wan has been instrumental in bringing Masdar City to life, in his role as design manager for the zero carbon city in Abu Dhabi. Educated at the University of Bath, receiving a BArch, he is a member of both the Royal Institute of British Architects (RIBA) and the Hong Kong Institute of Architects (HKA). He was previously an architect for Richard Rogers, Rocco Design, as well as Walt Disney Imagineering in Hong Kong. Wan moved to the UAE to join Sorouh Real Estate in 2006 before taking up his role at Masdar City in May 2008.
How would you define sustainability?
The question of defining sustainability is an interesting one. At Masdar City, we stick to the main core definition of it as revolving around the three pillars of economic, environmental and social sustenance, and we’re very clear when using that model for our projects and developments. If something isn’t economically sustainable, then by our definition, it isn’t sustainable at all. In that context, the question of what is the premium for sustainability is in some way a potential contradiction, because it seeks to treat cost as outside of the sphere. We instead view it as part and parcel of integrated sustainability.
Do you think sustainability is sometimes seen as unaffordable?
It’s understandable when industry players perceive green products and technologies as potential challenges to sustainability, due to their high costs. We at Masdar City are addressing the question directly, and the best way to do so is to give an example to amend this breakdown. The most common concern about sustainability remains the premium during implementation, but through a series of studies, lessons learned and interaction with the industry, we’ve reached the conclusion that perhaps the premium isn’t the real concern after all.
The question is regarding what approach is best suited for a given economic model – how can environmental sustainability be made commercially viable for a project operating within the given economical, budgetary or financial setups. When you ask the question that way, it ensures that, irrespective of the project result, it will work within the given economic setup. For instance, the recently launched Siemens building in Masdar City is commercially viable and generates profits for the shareholders, but it is also LEED Platinum and Estidama rated. We achieved all those aims without spending extra money over what we would in a business-as-usual office construction process.
What advice would you give to developers that want to build green?
Three things are important before designing actually begins. Firstly, get your brief sorted out and bought off by all shareholders. Next, work out a business plan so you understand your budgets and parameters and can design accordingly. Finally, set targets and goals for environmental performance before you start designing. Once you have done this, ensure you stick to the design and do not make frequent amendments and changes – it is the worst thing you can do to a designer who is halfway through his building drawings. We operate in a real world with actual time deadlines and cost constraints to deal with, and even one change in the design can lead to fluctuations in the entire project’s delivery timeline. Implementation of discipline, from start to finish, is critical to ensure the project does not stagnate or get delayed.
Which consultants should be involved in a sustainable project?
Working with a cost consultant is ideal in such scenarios, especially since they can estimate how much a building will cost if constructed without any sustainability targets – use that budget, and circulate it around your design team as the real budget. With the Siemens project, we had a cost consultant as part of the decision-making team, who worked with the designers over details such as choice of glass, material, fixtures and so on, because it all matters when pricing is concerned. Eventually, the cost of the project was very closely monitored at all stages, such as concept creation, schematic design, detailed design, construction documentation, pre-tendering estimates and so on.
How should costs be allocated for a green project?
There is definitely a market here for a green supply chain to operate. It eventually boils down to appropriate cost allocation. For instance, we used a variable fan coil unit for the Siemens building, which massively contributes to reducing energy-consumption in comparison with a normal fan coil unit. If the question is ‘do they cost more?’, then the simple answer is yes. But we view cost as more than an individual component and as a holistic part of the total building – the technology itself is a key part of the jigsaw, in a way. It is up to the designers to work out with the stakeholders what the best cost allocation within given budgets will be.
Put simply, do we invest in an energy-recovery system, or do we spend on importing marble supplies which may be available in the local market with the same specifications? To address these budgeting and allocation questions at a workshop level is far more sensible than throwing everything together and hoping the budget will work out. Eventually, subsidised or not, the market value of such green products and services remains what it is. At Masdar City, we believe in optimising the real situation, where we find a solution to deal with the challenges it may throw up, as against looking for cost-cutting alternatives.