Tomorrow’s world

Despite its futuristic properties Pittsburgh Corning’s Foamglas dates back to the 1930s
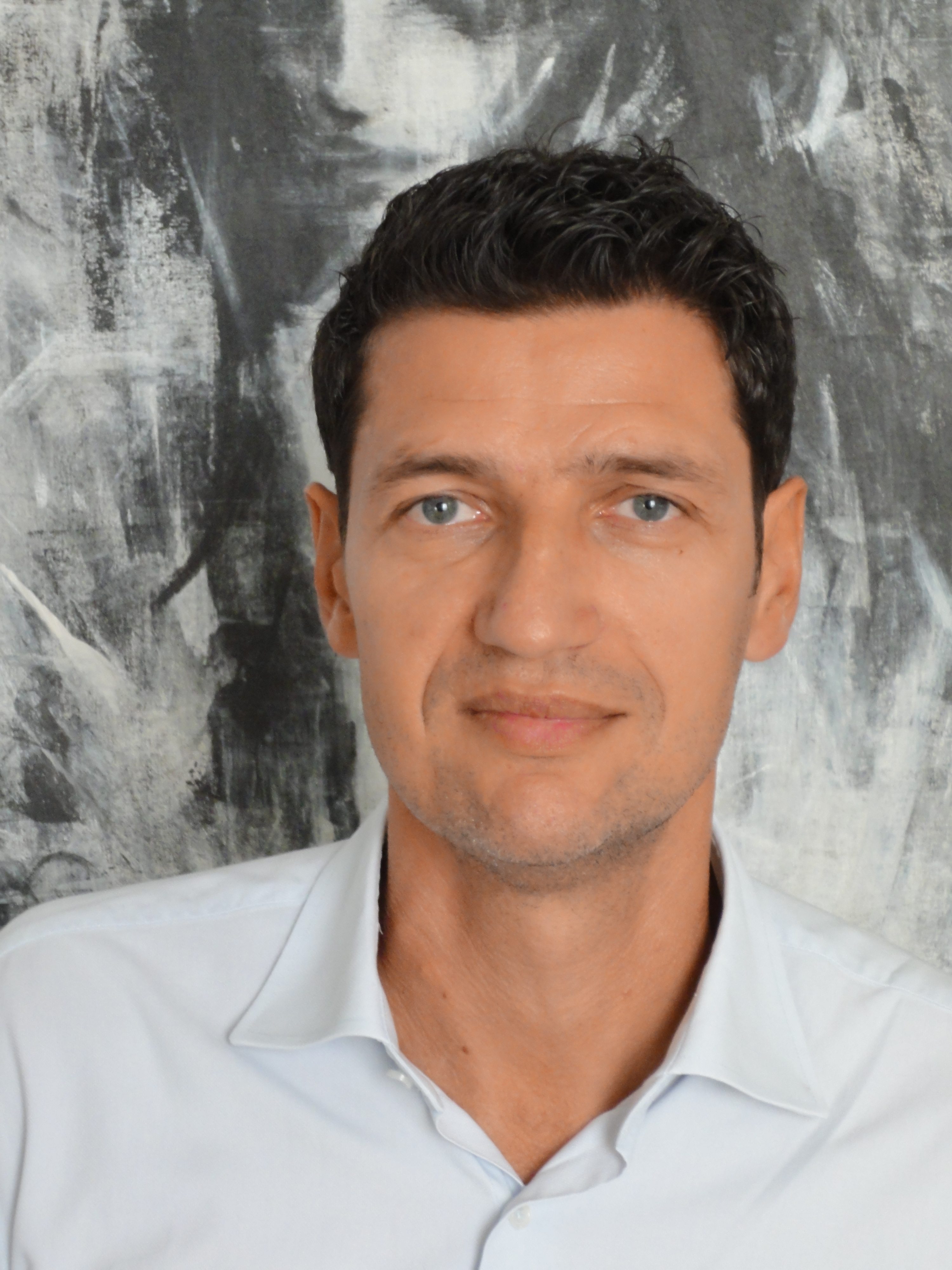
It sounds like a product from the future: water, fire and degradation-proof; environmentally friendly; and strong enough for use under concrete slabs. Yet Foamglas has been specified in projects for more than 50 years.
The stuff tomorrow’s science is made of, Foamglas is an insulation material composed of millions of hermetically sealed glass cells, locking in a vapour barrier which facilitates its waterproof and vapour-tight properties. It is due to this cell geometry that it has high compressive strength, even under long-term loads.
“The most important part is that we have 66% recycling content and in the production we use only renewable energy,” explains Middle East sales director Marco Vincenz, adding: “We do not need water to produce FoamGlas and it has a very long durability.”
Continuing to promote the benefits of Foamglas for applications in the Middle East, Vincenz says that due to climatic conditions, pressure comes from inside a building — where air is cooler — meaning insulation materials require protection from atmospheric moisture.
However, Foamglas includes a “wave of tightness”, which forms a moisture barrier; one property which manufacturers Pittsburgh Corning say makes the material unique. “This is a very old principle, the product has developed but this is glasfoam. The only thing we do at the moment is use small cells to improve thermal conductivity and we improve
the compressive strength,” Vincenz continues.
“If the cells inside the insulation are smaller the product can carry more weight. If you look at the flat roofing in this region, Foamglas can carry those loads so you can apply it to parking decks, roof gardens, and so on,” he adds.
Behind the science
Pitsburgh Corning began when the American Pittsburgh Plate Glass Company and Corning Glass merged, forming the Corning Corporation, in 1937. The new company spent two decades researching the science behind industrial glass applications.
The company then moved into the European market, opening a production unit in Belgium in 1962, close to vast resources of sand, to reduce transportation of raw materials. Today, Foamglas products are manufactured in facilities
Tessenderlo, Belgium; Schmiedefeld, Germany; and Klàsterec, in the Czech Republic.
A wholly owned subsidiary of Pittsburgh Corning Europe was established in Dubai in 2006, to provide sales and technical support, design and onsite technical training to the Middle East market.
Foamglas has since been specified by both the region’s and the industry’s biggest names, such as Al Futtaim and architects I. M. Pei and Roger Tallibert.
The most high profile projects to date have included the Armed Forces Officer’s Club, Abu Dhabi; the Intercontinental and Crown Plaza Hotel, Dubai Festival City; Doha’s Texan A&M University and the Museum of Islamic Art.
Commenting on the application of Foamglas at the Armed Forces Officers’ Club, Vincenz says the product was specified after the failure of other systems.
“At the end of the nineties the roof required a refurbishment of the sprayed polyurethane thermal insulation and waterproofing, which had failed. The client followed the architect’s recommendation and chose the Foamglas compact
roof build up with a metal roof covering.”
Built to last
For the A&M University project, Foamglas was specified for its resistance to humidity and durable performance.
“A two-layer brick wall does not provide a fully water and vapour proof external shell and high humidity and extreme heat can affect the thermal insulation between layers.
“Foamglas, will never warp, slack or lose any of its performance qualities over the whole lifecycle of the building,” Vincenz explains.
During the development of Doha’s Museum of Islamic Art — located on a man-made island exposed to high humidity — an insulating material was required that would offer enough durability to withstand demanding climatic conditions; and it was required in bulk to cover a space of 22,000 square metres.
“The external wall of the museum is finished with 6,500 M³ of natural stone work,” says Vincenz, adding: “High temperatures combinedwith high humidity and an open joint application of the facade demanded high quality
in the structure below, especially for thermal protection, because access to the ventilation space is not provided any more.
“The protection Foamglas offers also means HVAC upgrades are never required.”
“Degradation through humidity abortion is the biggest problem in the Middle East for wall insulation, next to fire issues.
“Foamglas is fully inorganic and will not support any fire. With no flame spread and no smoke development it provides the highest safety and ensures the highest standards even in the building envelope,” he adds.
One of a number of research and design projects, the manufacturer is looking at combining Foamglas with photovoltaic solar panels to integrate the panel and insulation. The project began in December 2010 and will be brought to the Middle East in the near future.