Site visit: Al Maryah Central, Abu Dhabi
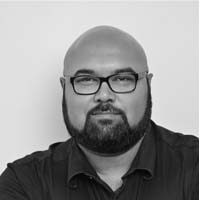
What it takes to bring Gulf Related’s vast project to fruition.

Approaching the Al Maryah Central construction site, the first impression is of its massive size. With hoardings stretching out 600 metres along the main thoroughfare, around all four sides of the site, the scale of the project becomes very apparent, very quickly. Even more so if you’re a confused construction journalist with an unreliable sense of direction, looking for to the project office.
To get there, one must descend through the service roads that run under the main highways that encircle Al Maryah Island, bringing visitors down to sea level, which is where the true mastery of the island’s engineering is revealed.
IN PICTURES: On site at Al Maryah Central, Abu Dhabi
Driving past the forest of columns holding up the elevated roadways above, it quickly becomes apparent that any sort of construction work in the area requires careful planning, execution and delivery due to the space constraints around the site. It’s easy to see why the idea of building Abu Dhabi’s premier retail destination in such a confined space would be daunting to even the most skilled contractors.
Perhaps this is why Gulf Related, the developer behind the Al Maryah Central project, decided to award the construction contract to Brookfield Multiplex, known for its vast expertise in building challenging projects to tight deadlines and specifications.
In August 2015, it was announced that the international contracting firm had been awarded a $425 million contract to be the main contractor responsible for the completion of the $1 billion shopping mall. With the development having broken ground in November 2014, excavation of the site and foundation construction work had been completed before the contractor began operations on-site.
With the mall scheduled to open in March 2018, the pressure is now on Brookfield Multiplex to meet that delivery date. With seven months now passed, Big Project ME decided to head down to Al Maryah Island to find out how work is progressing on the massive project.
“The project itself is close to 450,000sqm of retail space. There are two anchor tenants – Macy’s and Bloomingdale’s. We call them the bookends,” says Matthew Hewitt, project director for Brookfield Multiplex on Al Maryah Central. “There are another 400 individual shops, food courts, eateries and retail within the main mall.”
IN PICTURES: On site at Al Maryah Central, Abu Dhabi
All of this will be housed in 288,000sqm of mixed-use development at the centre of Al Maryah Island. Home to the first international Macy’s department store, Abu Dhabi’s first Bloomingdale’s and a multitude of high-end retail, hospitality and entertainment options, the project will also offer two 37,161sqm integrated towers that will comprise hotel serviced and residential apartments and luxury residences. Furthermore, the mall will link up with the already existing The Galleria development, which is adjacent to the construction site.
Interestingly, these were not the only challenges the team had to face, Hewitt says. The construction team had, and have to, work around a host of constraints.
“There are four stories of basement, and the unusual aspect of Al Maryah Island is what they consider ground floor is actually +14 (which refers to 14 metres above sea level – the level of the elevated roadways around the project). This is entrance level to the mall, also referred to as ground floor or podium level. So the elevated roadway, that’s actually the ground floor, and the basements start thereafter.
“We’ve got three floors of basement that are actually above ground, but they’re below the roadway. Then we’ve got one sub-basement level, B4, which is actually below ground. That actually touches the water table, because we’re that close to the sea, so obviously that presents some significant challenges with the water table, waterproofing and so on.”
Peter Anderson, executive vice president of Real Estate Development for Gulf Related, adds that this is a prerequisite for the island, with no car parking garages allowed above the +14 level.
“The requirement of a shopping mall of our size is to have a minimum number of car spaces available, which means that on the footprint that we have, we had to keep going down until we could accommodate that. It pushed us down to the four levels that we have at the moment,” he says.
Given the nature of the island, working below ground level meant that the team faced challenges due to the proximity of the sea. However, what helped enormously was the advance planning Gulf Related had done with regards to the ground work and foundation. With the developer having already started foundation works ahead of appointing the main contractor, using their in-house team, Brookfield Multiplex’s task was made much easier, as Hewitt explains.
“When we arrived on-site after being given notice to proceed, all the piling, the second piling and the main foundation piling had already been done. Our first tasks were to do the detailed digging around the piling, the crimping and cutting away of the pile-heads, start the sacrificial blockwork and actually start the pile cap process. Because a lot of work had already started, that gave us a flying start into actual construction activities,” he says, estimating that the team’s mobilisation period was reduced by at least 50%, if not more. “We were actually pouring concrete within six weeks of being on-site.”
“Our approach to the project has always been to have an aggressive schedule for delivery of the project. To accommodate that, Gulf Related let two early work packages out, separate to the main contract. We managed that ourselves,” Anderson chimes in. “The two early works packages were an excavation package and a piling and shoring package. We ran and managed those ourselves with a different contractor.”
IN PICTURES: On site at Al Maryah Central, Abu Dhabi
He adds that this approach had two benefits – firstly, it allowed them to finish negotiations with the tenders they’d called for the project’s main contractor works, and it also allowed Brookfield Multiplex to hit the ground running when the time came to start construction.
“The biggest aspect, from our side, was that when we were notified that we were the preferred contractor, we immediately commenced working on the project. Even before the execution of the main contract, my immediate team and I were working on the project for about two months before that. It allowed us to get an understanding of the job and to get integrated with the client team. Particularly, it also allowed us to get integrated with all the major third parties, which is a major part of the project,” says Hewitt.
“On this island, there’s the master developer Mubadala. Anything we do is as the next level developer. While we’re actually developing the site, Mubadala hold the masterplan for the entire island. So we have an authority approval process with them for everything that we do,” Anderson adds.
“On top of that, we have the Urban Planning Council [UPC], which keeps the vision for 2030. We then have the Abu Dhabi Municipality, which looks after all the rules and regulations associated with buildings and makes sure that you build them to the codes and standards.
“And in conjunction with that, you have all the utility authorities, where you generally need NOCs to progress with any form of construction, either on the site or where we touch on the public realm around the site.”
Anderson adds that on top of all of these considerations, the project is also right in the middle of an investment zone, and as such they are answerable to yet another authority in the shape of the Abu Dhabi Global Markets.
“This is less to do with the construction, but more to do with the development side of the project, but that’s another authority level that we have to go through as well. It’s fair to say that the critical path for construction definitely runs through the authority approvals that we have to get.”
Hewitt points out that because the island is already quite well established, with a lot of development already underway or scheduled to start soon, the construction team has to be mindful of what’s going on around them.
“A lot of these infrastructure and major assets are going through an adoption process as well, where they’re changing hands from the master developer back to Abu Dhabi Municipality, the Department of Transport or to the localised utilities – Etisalat, Tabreed and all those. Because of that transition process, we could be dealing with one entity [at the time], or within a couple of weeks we could be dealing with another entity entirely [for the same thing].
“There’s no point in pursuing something that’s in the midst of being handed over, if it isn’t super-critical. Especially when we can actually physically wait for it, or be led by our client, who have agreed, in certain areas, that the adoption process can wait,” he reiterates, highlighting just how much the project affects the rest of the island.
IN PICTURES: On site at Al Maryah Central, Abu Dhabi
This translates into certain aspects of the project being pushed back and put on hold, while others have been allowed to go through at an accelerated rate. Gulf Related has also looked to adopt part of the island’s light rail system for the project’s benefit, Hewitt reveals.
“That’s just for the period of the project. It gets handed to us and we can facilitate additional works, logistics and management within our own domain. That’s really been the key – the collaborative work between us and the client.”
That collaboration certainly shows on-site, given that the team is only seven months into the contract but is already pouring, on average, 4,500 to 5,000 cubic metres of concrete weekly. Working together, staff from Gulf Related and Brookfield Multiplex were able to track the approvals process and understand how it could be overlaid and integrated into the aggressive construction programme.
Furthermore, Hewitt says, this also allowed them to cope with one of the most challenging aspects of the job: the location of the site and the congested areas around it.
“The site set-up was absolutely key. [We had to consider] how were we going to deliver materials and how we were going to move men and materials. Because the site is such a large-scale project, and because of the number of sub-trades we’ll have on-site, procurement was probably next on our critical path, as was our ability to buy those trades in time to meet the aggressive programme.”
As part of Brookfield Multiplex’s contract obligations, the team has had to bring in a number of domestic trades, while there is also a large proportion of provisional sum trades that they have to buy collaboratively with Gulf Related.
“We need to achieve not only budget, but aesthetic and design intent, because they are often the packages that achieve the finishes. But you know, eight months in, we’re 96% through procurement, so from that perspective, I’m very happy. And from a production perspective, we’re definitely within target of where we need to be on the entire project,” Hewitt asserts.
Another way the team has managed to work around the logistical issues it faces on-site is through the development of what Hewitt calls the “best-in-class welfare, logistics and off-site management facility”.
IN PICTURES: On site at Al Maryah Central, Abu Dhabi
This 70,000sqm plot of land deals with three key issues for Brookfield Multiplex – processing labour to get them on- and off-site, keeping an accurate record of everyone who goes on- and off-site through a state-of-the-art biometric palm scanner system, and finally the management of material required on-site.
“We realised very early on that we would need extra storage area outside the site boundary. There was an amount allowed for in the contract. Through careful petitioning and demonstrating the benefits of it, Gulf Related were able to assist us in getting more laydown area than we first anticipated,” he says.
“A lot of our material will come in as an on-site delivery service. The more storage and processing area that we have outside, the more we can assure ourselves of two key things: one, that we’re keeping programme and delivery dates, and secondly, that we’re lessening the impact on the island as we’re not blocking up roads.”
From a health and safety perspective, and from an emergency evacuation perspective (in keeping with Urban Planning Council guidelines), the biometric palm scanner system allows the team to keep track of the 3,500 men moving in and out of the site on a daily basis. At peak construction, that number is expected to be closer to 6,000.
The effort to develop the massive laydown area is part of a company-wide initiative that puts worker welfare and worker rights in the spotlight for 2016. So seriously is this being taken that the contract for the project explicitly lays down the set criteria that have to be achieved.
“What we’ve been able to achieve out here, both from a management perspective and just as a general processing facility, is that we’re getting very beneficial reports on employee engagement. There’s just a general level of appreciation and happiness,” Hewitt states proudly. “Apart from validating what we’re trying to do, it does make you feel good that you’ve actually achieved what you’ve set out to do, right from the outset.”
Impressively, the team has recorded more than two million man hours without any significant HSE incidents, testament to the way things are being run on-site.
“No one has to step outside what we call the ‘back of house’ and affect footpaths or even the underground levels that are used to access the site. That’s public highway, so we don’t walk across there. In fact, we don’t need to walk across there,” the project director says.
“From our facility – where we can sit 3,000 men at any given time – we can funnel workers through the biometric palm readers, up a flight of stairs, across an underslung bridge that sits under the main highway and straight onto the site. There’s obviously an expense that comes with that, but we think the benefits far exceed the initial set-up costs.”
Anderson fully endorses this methodical and considerate approach, telling Big Project ME that Gulf Related is very conscious of the difficult conditions the team is working in.
“We’re very committed to what Brookfield Multiplex is doing, and we’re trying to raise the bar on that sort of thing. We have our own health and safety officers, two actually, who are full-time employed by us. We also have a number of incentives that we run independently of what Brookfield are doing to motivate and reward people on-site.”
IN PICTURES: On site at Al Maryah Central, Abu Dhabi
This rigorous approach to health and safety paid off in spectacular fashion in March, when a massive thunderstorm hit Abu Dhabi and Dubai. With severe flooding and high wind-speeds causing chaos around the cities, workers on the Al Maryah Central site were kept safe and secure due to the planning put in place by Hewitt, Anderson and their teams.
“We had no reportable injuries with 3,500 men on-site, so I was very happy with that. We were actually pretty empty before we even got the Abu Dhabi Municipality bulletin that all sites had to be closed,” recollects Hewitt.
“Once the storm was over, we went through on-site engineering and safety tests all of the next afternoon. We were given a clean bill of health to reopen on the following day, and were back pouring concrete by the next evening.
“The formwork systems that we’re using actually stood up to the storm really well. We did have water ingress, but because we’ve finished most of the basement level, 3,000 men were able to weather the storm in the basement before we had to pull them out. That was probably the biggest saving grace that we had – the aggressive nature of the programme allowed us to have a basement where the guys could go. And then we had the facilities where we were able to transport them off the island within two hours.”
While Brookfield Multiplex is undisputedly in charge of operations on-site, there is a clear sense of collaboration and cooperation between all the partners on the project. Rather unusually for a GCC project, this process is led by the developer, who has taken the initiative to make sure its consultant team and main contractor are communicating clearly with each other.
“We’re working with AECOM, who are a locally based firm. We’re working with Elkus Manfredi, who are our design architect, while our structural and MEP engineers are Thorton Tomasetti and WSP | Parsons Brinckerhoff respectively. Faithful + Gould is our cost consultant, and obviously Brookfield Multiplex is our main contractor,” recounts Anderson.
“They’re all international, well respected consultants. We’ve worked very hard and long to pull together a consultant team and a contractor who could deliver this project to the quality aspirations, and to the schedule that we’ve set down.”
Hewitt is quick to give credit to Gulf Related for the atmosphere of cooperation surrounding the project, pointing out that the developer has allowed Brookfield Multiplex to closely assist their design team in certain instances. In return, the developer has been integrated into the contractor’s supply chain so that they can be involved in the selection process and be comfortable with who is chosen to come on-site.
“I walk the site every morning at 6am with the vice president of construction for Gulf Related,” says Hewitt. “That way, I know what’s on his radar for the day and he knows the issues that I’ve got for the day. Then we collectively work to get over them.”
“You hear it all the time: collaboration, collective motivation and all those catchphrases. But this project is truly – from our perspective – a partnership. We’ve got an aggressive programme, and both sides of the fence recognise that. Anything that we can do to get over that, we try and do.”
“A successful construction team is not all about how you build a project,” says Anderson. “It’s about how you react to issues on-site, and at a major construction project, it’s all about the way you react. And the way you react will determine how quickly and how well you go forward.”
“We have a number of forums between ourselves and the main contractor. At a senior level, at the next level down and the next level below that. We continuously talk about issues on a daily, weekly and monthly basis. There’s a forum of the four senior guys from Gulf Related and the four senior guys from Brookfield Multiplex. This goes all the way up to the managing director for the region. We meet on a monthly basis, we talk about high-level issues and try to address them proactively.”
IN PICTURES: On site at Al Maryah Central, Abu Dhabi
That cascades down through to the site team, Hewitt says, explaining that progress meetings between all stakeholders are held once a week, in addition to a collective programme meeting and two main design coordinating meetings a week.
“And there’s breakouts from that! There would probably be 14 different coordination disciplines that are carried out during the week. So all of these are either facilitated in the Brookfield Multiplex site office, or 25 feet away at the Gulf Related office. It’s all part of the original thought process.”
“There’s a method to the madness!” both say, almost in unison, summing up just how intertwined these companies are when it comes to delivering this fascinating and complicated megaproject to the people of Abu Dhabi.
Project Details
Developer: Gulf Related
Main Contractor: Brookfield Multiplex
Main Consultant: AECOM
Design Architect: Elkus Manfredi
Structural Engineer: Thornton Tomasetti
MEP Engineer: WSP | Parsons Brinckerhoff
Cost Consultant: Faithful + Gould
MEP Subcontractor: JLW Middle East
Tower Cranes: Brookfield Multiplex Plant & Equipment
Earthworks: Emirates Landscape
Structural Steel: Eversendai Engineering
Commissioning Manager: AESG Green Building Consultant
IN PICTURES: On site at Al Maryah Central, Abu Dhabi
Building through the Building
There are several different types of formwork systems used on the Al Maryah Central project, to allow the team to meet different challenges on-site.
Given the design of the mall, there are very big open high-level spaces, with floor heights changing from single to double. In addition, there are loading docks, main atriums and structural steel elements to consider as well, making construction a challenge for the Brookfield Multiplex team.
“To achieve that, you need different types of formwork. You can’t just rely on one. We’re using a type of formwork that’s very malleable, which is the tablet system. We’re also using the more traditional ones to achieve the high-level and heavier construction work,” says Matthew Hewitt.
Interestingly however, the biggest innovation on-site comes through the use of the six tower cranes in operation, he reveals.
“They’re our lifeline, absolutely. We looked at having more, but the potential for clash and downtime because of that [ruled that out]. It would have been nice to have that redundancy, but it just didn’t make economic sense from a time perspective. Six cranes can work here, 100% of the time, all the time.
“[However], we’ve got to achieve two completion dates on the project. We’ve got to achieve a completion date (which we’ll call BCC 1) for the two anchor tenants. We’ve got a 13-month fit-out period for them, and then we’ve got BCC 2, which is a seven-month fit-out for the rest of the mall.”
In order to achieve either of these dates, the basement of the mall has to be completed, with all the essential life safety and plant equipment in place. Complicating things, however, is the presence of the six tower cranes which go straight through that basement.
“Our intention is that all six of the cranes will climb up through the lower levels, climbing through the mall frame,” explains Hewitt. “That way, we can progressively pull them out of the basements and infill them as we go up, and then take the cranes out as they’re not needed.”
Figuring out how this can be achieved is down to the team at Brookfield Multiplex’s in-house Plant and Equipment division, says Hewitt, who readily admits that it is vital to the successful completion of the project.
“Without the in-house facility, I don’t think that we would have achieved anything near [what we have now]. We couldn’t have been as aggressive, because when you rely on a third party, you can’t guarantee that level of service. With an in-house division, I can guarantee that. They’ll allow us to pull it out, infill it and allow the basement to be handed over. Then we’re just dealing with the different sections.”
Having an in-house team on board also improves the safety and security of the tower cranes. In light of the recent incident in Saudi Arabia, it’s understandable that Hewitt and his team are extra-cautious about this. To that end, a comprehensive system of checks has been put in place to ensure that the cranes can withstand severe winds and other pressures, as the project director explains.
“All our equipment, particularly our tower cranes, are installed by our in-house division. Then we go through a rigorous third-party check. And that’s not just on the installation, they also go through a comprehensive check that the crane is working properly, and that all of the engineering behind it [is sound]. The base, the piles and the connections are all third-party checked by an independent engineer, who is not part of the project.
“Once we get that tick in the box, that would mean that we’ve had three engineers to run through it – the P&E engineer, the additional base engineer and then our third-party engineer. As an additional rigour, we then send it through to the client’s design team, Thornton Tomasetti, who will also have to give it a clearance. From that point, we all know that the cranes are solid,” he concludes.
IN PICTURES: On site at Al Maryah Central, Abu Dhabi
Concrete Boom
The other big challenge facing the construction team is the pouring of concrete on-site, which is more more than half a kilometre in length.
“It’s huge. From a concrete perspective, it’s not so much the volume of concrete, it’s the amount of area that we have to cover,” says Hewitt. “We’ve got upwards of 12 placement booms that cover approximately 95% of the entire job. That will allow us to climb with the job, and will also give us 12 areas where we can offload concrete.”
This has the added advantage of not restricting the team to just one or two entrances to the site, but in fact giving them 12 access points, thereby limiting the disruption to traffic flow on the surrounding roads.
“We’ve got better coverage. That means we can put more trucks on the road, while having less of an impact and being able to pour more concrete. We can dispatch, on any given evening when we’re pouring concrete, anywhere between 100 to 200 wagons an evening. Logistically, that’s a lot to deal with!”