Site visit: Lu’Luat Al Raha, Abu Dhabi
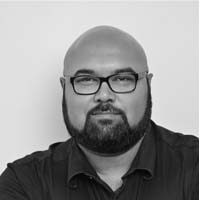
Phase one of construction has begun on the ambitious mixed-use development

As the GCC looks to modernise and create cities that measure up to any in the Western world, there has been a shift across the region towards developing master planned communities that fulfil both residential and commercial needs, while also meeting the requirements of municipalities and governments in terms of sustainability and urban planning.
One city that has perhaps done this better than most is the UAE capital of Abu Dhabi, which is rapidly gaining a reputation as a global capital city thanks to its many developments along the coast of the emirate, as one enters the city travelling from Dubai.
While there has been considerable focus on projects such as Al Reem Island, Saadiyat Island and Abu Dhabi Capital District, one that has escaped the attention of the general public is the Al Raha Beach development, situated alongside Aldar’s distinctive headquarters.
Built on 5.2 million sqm of natural beachfront, the Al Raha Beach development is set to be a mix of residential, commercial, cultural, entertainment and public facilities, and will ultimately house more than 120,000 people.
This massive development is set to spawn a number of projects that will have a significant impact on the construction landscape of the capital. One such project is Lu’Luat Al Raha, a mixed-use development at the core of the vision for Al Raha Beach.
Developed by International Capital Trading, a private Abu Dhabi company that owns a number of real estate developments in the emirate and around the world, the Lu’Luat Al Raha project is a reclaimed island that will be home to a number of developments, ranging from beachfront villas to mid- and high-rise towers. It is expected to have more than 6,000 residents, with a daytime population of up to 13,000 (including visitors to the island).
Situated opposite the existing Al Raha Beach Hotel, the Lu’Luat Al Raha project will be surrounded by the Khor-Al-Raha, a creek giving residents access to their own beaches and marina. In addition, the site is being designed to be pedestrian- and bicycle-friendly, with a continuous promenade running around the whole island away from car traffic, connecting the entire development.
With the project situated at the core of the Al Raha Beach Development, it is being designed to provide the community with easy access to both Abu Dhabi and Dubai. It is a 10-minute drive from the future Capital District and is accessible to all emerging developments in the area. In addition, it is just five minutes from Abu Dhabi International Airport, 10 minutes from Yas Island, 65km from the Dubai border and 75km from Al Maktoum International Airport in Jebel Ali, Dubai.
The project will be further connected through the development of public transportation systems, such as a planned light rail Transit (LRT) network and water taxis that will connect the entire community.
Phase One of the project began on January 6, 2015 and is currently well underway, with infrastructure and utilities being installed. Big Project ME paid a visit to the site offices of Mouchel Consulting, the construction supervisors and concept and landscape designers for the Lu’Luat Al Raha project.
Built on reclaimed land, the project posed a number of challenges for Mouchel and the rest of the construction team, as Leighton Greenland, infrastructure director (UAE and Kuwait) for Mouchel Consulting, explains during an interview prior to a tour of the site.
“We actually designed the whole island – Phase One and Phase Two. Phase One is now in the construction phase. We looked at all the utilities, as well as the roads, the sewage, the storm water drainage, the irrigation, potable water, landscape and the marina. We also had the bathymetric surveys done to make sure that everything works and flows properly. The total area of the island is 82.4 hectares, so it’s going to be a significant development in the area.”
David Dunn, technical manager, and Asaad Ali, resident engineer, are also present at the meeting and explain the impact of the project further. “There’s about 850,000sqm of GFA. It’s a mixed-use development and comprises residential, commercial and also leisure. Approximately 250,000sqm of the site is reclaimed land, and it’s one of several islands that are going to be built along this stretch of coast,” says David.
“We’re undertaking Phase One of the construction at the moment, and our role is to provide all the infrastructure design. We’ve also been involved in the land reclamation. At the moment, the roads design is there, and we’re putting in all the utilities, starting with the deep utilities and then working from there.”
As resident engineer, it is Asaad Ali’s job to ensure that all of these jobs are being carried out by the contractor – Trojan General Contracting – and subcontractor – National Projects and Construction. In addition, he has to watch over the other contractors, such as Gulf Dunes, the subcontractor for landscaping works.
With work on other construction sites also going on around the Lu’Luat Al Raha area, there is limited margin for error. Ali has to ensure that everyone, not just the construction team, but everyone involved in this project, even tangentially, is kept up to date.
“On a weekly basis, I conduct coordination meetings with Aldar. All of their construction team is represented and we share information about where we are and where they are. We share our drawings, match their requirements and conduct joint surveys between their construction team and ours, so as to make sure that all our efforts are on the same page,” Asaad Ali explains.
“This is a continuing process. If they have any issues, or if we have any issues, we can discuss them during the meetings.”
These meetings are crucial to the success of the project, the Mouchel team says. They point out that the Lu’Luat Al Raha development is part of a much larger master plan, and as a result, alternative design solutions are sometimes urgently needed to meet the changing locality.
“Some of these challenges have been simply because the whole development – the whole area – is being worked on. It’s the 2030 Vision that they’re looking at. But some places are a bit slower than others. There have been challenges; making sure that everything fits within the master plan [is difficult] because you’re relying on other areas being developed as well,” David emphasises.
“We’re fortunate in that we have a very good client here. ICT are great at assisting us with the authorities when something in the approvals process stalls. Building relationships with the client, over a period of time – from the very start of design through to the construction supervision stages – has been the main point of what we’ve had to do and has paid dividends in the delivery of this project.”
The scheduled completion date for Phase One of the project is September 1, 2016 and Asaad Ali praises the role Trojan General Contracting is playing as contractor, in making sure that the deadline will be hit.
“They’re achieving the programme, and they’re progressing as per the current available area for their work. Hopefully, we can deliver it ahead of time. That’s been their target for the last couple of months – they think that they can deliver the project ahead of schedule.
“We have the contractor monitoring plan and we have the procurement plan. That means that whatever the materials, whatever the logistics, all of it is planned. Initially, we planned that we would have to get all the heavy logistics – the bridge works, the pipes – they all had to be completed within eight months. That’s because, on the other side [of the island], we received information that they had started their construction, so it would be difficult to pass heavy vehicles from there. We closely monitor our logistics plan.”
With an access bridge being built across the creek, coordinating the movement of vehicles, equipment and materials to and from the site will become a lot easier. Work on the bridge is nearing completion, with a finish scheduled for May 2016, the trio say.
In the meantime, work on Phase One continues apace. Alongside Mouchel’s team of 12 engineers, there are between 300 and 350 workers on-site, from both contractor and subcontractor. By the time peak operations are reached in November/December this year, there will be as many as 800 workers on the island, Ali says. This is in addition to the 57 staff – engineers, safety officers, foremen, etc – on Trojan’s team.
Having so many people on the island poses an interesting health and safety challenge for the team, and part of Mouchel’s construction supervision remit is ensuring that HSE standards are adhered to. Ali and his on-site team have a fairly complex task on their hands.
“Mouchel has its own policy for HSE, which is SHEQ – Safety, Health, Environment and Quality. We use it across the UK, over here and in Saudi Arabia. It’s a tried and tested plan. We have on-site inspectors who look after health and safety, and we have HSE teams,” says David.
“At any time, when we find something that’s not quite correct, we talk to the contractor’s health and safety team, we talk to their management, and it’s brought to the attention of the likes of ICT during the weekly meetings.
“We also have a monthly SHEQ committee meeting that looks after all our offices and sites in the Middle East. We share knowledge of things we have found on-site, which are then shared with other sites so that we can develop a new plan, as we can now see things that may happen in the future [on other Mouchel construction sites].”
Leighton adds that the on-site inspectors provide feedback on a project’s HSE issues to the Mouchel offices, and it is then distributed to the entire senior management team. The information provided is then disseminated back to the project teams, with suggestions for improvements if necessary.
“I have one safety engineer, and for the contractor, they have the complete safety team, including a safety manager and three safety engineers. On each area [of the site], they’ve distributed their people, and on a daily basis – three or four times a day – our safety engineer is available on-site to look at safety procedures. These include safety tool talks and safety inductions around the staff. It is part of their usual procedure,” outlines Ali.
These different levels of HSE are particularly pertinent due to the site being an island. Not only is excessive humidity a major concern, the team also has to be aware of construction works taking place around the promenade of the island.
“That’s a major challenge. They have to make sure there’s the proper protection and that all the workers have their hazard belts, and that the proper barricades are all around the promenade, wherever people are working,” Ali says.
David adds that because they’re working in a primarily sand-based work environment, care has to be taken around deep excavation sites to ensure that there is proper shoring and earthworks benching in place and that the contractor is working safely in conditions that do not lead to any ground disturbance that could potentially cause harm to the workers.
However, these are far from the only challenges the construction has to overcome. As part of the utilities infrastructure currently being laid out, the Mouchel team has to ensure that the correct levels are planned for and laid out, so that everything works smoothly when complete.
“You have the services such as sewage and storm water drainage. They’re gravity-mains, so you’ve got to make sure that you have the correct gradients on the networks for it to function efficiently. Getting the correct levels means that we have to grade the reclaimed land with imported material,” says David.
In addition, the team has to ensure that all the infrastructure and utilities on the island link up with those on the mainland. In order to do so, Ali explains that they had to take great care to ensure they met all requirements from authorities.
“The main challenge was with the main potable water line and the sewage line. All the existing connections are there, but they’re all going through the bridge. So, for the bridge, all the authorities have certain requirements when you’re passing rising mains through a bridge. All our utilities connect with existing utilities, which are [across the bridge]. That is a major challenge; everything needs to match the exact criteria.”
Another major factor in the development of the island is sustainability. With Abu Dhabi’s Vision 2030 taking shape across the emirate, ICT and the Mouchel team are determined to ensure that the Lu’Luat Al Raha project lives up to the ideals espoused by the government.
“There’s a Pearl rating for this site as well, and we’re pushing towards that,” says David. “[The types of] construction materials used, the reuse of materials, it’s all prominent on the site. We need to meet these Key Performance Indicators. It’s difficult, because not everybody is familiar with Estidama. It’s still a maturing objective, but we’re certainly pushing for this within the site, and it’s certainly something that the client is looking at as well.”
A large part of the coordination and collaboration between all stakeholders on the project entails meeting these sustainability targets. By working together and keeping everyone informed, they ensure that the right materials are used and that the design and installation guidelines are followed to the letter, so that there is no need to go back and fix things, wasting materials, resources and manpower.
“ICT have a vision of an extremely high-quality project, and Mouchel has embraced that vision in its design. This is central to the whole island, it’s central to Abu Dhabi’s way of doing things, and it’s central to the technology progressing, with really good building standards,” says David.
“It’s fortunate that we have a client who has the foresight to look at it [like this]. It’s a good vision and it’s progressing the way Abu Dhabi will be seen from elsewhere, within the GCC and further afield. I think it’s a project that, once it’s completed, will look absolutely stunning,” he concludes.
ISLANDS ON STREAM
As part of the sustainability targets for the Lu’Luat Al Raha project, Mouchel has engaged a subcontractor called STREAM to develop an automated waste collection system, as Leighton Greenland explains. “We have an automated waste collection system that is a vacuum system that goes to one compaction site, where the waste will be compacted and taken away.” Rather than having the traditional open bins or waste collection bins outside apartment blocks, the STREAM system uses a chute where everything goes down and is vacuum-driven to a collection site, where it is compacted and readied for collection in bulk. “That will be in operation when the residential developments are here. Residents will have a waste disposal system that’s automatic, and the entire process is automated, which means you won’t have a lot of refuse collection vehicles around the island,” Leighton says. In addition, the process separates recyclable waste and non-recyclable waste, with subcontractors engaged to use the recyclable waste in a safe and environmentally friendly manner. “This is in line with the Abu Dhabi waste management policy for recycling. They’re trying to get recycling at a level where it’s more compatible with the likes of Europe,” says David. “This is a very good way of doing it.”