Site visit: Siemens gas power plant, Germany
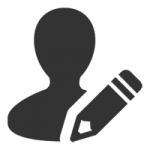
The Lausward gas power plant in Düsseldorf is set to be one of the world’s most efficient
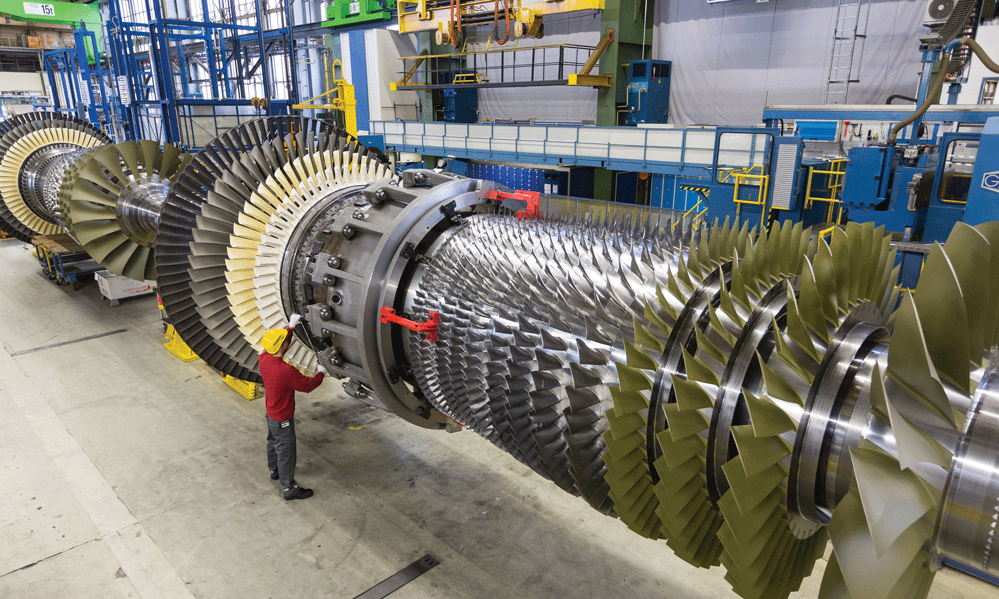
As the population in the Middle East continues to grow and cities in the region expand, it follows that governments will have to invest more in infrastructure – everything from public transport to healthcare and education – to cope with the scale of growth.
Hardly any urban expansion is possible, however, without electricity. The region will need not just more energy, but cleaner and more efficient ways of generating it.
In a typically fossil fuel-dependent region, it will be a while before renewables contribute significantly to the energy produced. However, due to possible fluctuations in the output of renewable energy, clean plants powered by conventional sources could be key to satisfying base load requirements. For this reason, it’s worth looking west to see if some lessons from Europe – which leads the way in clean energy – can be adopted.
Big Project ME was recently invited to tour a combined cycle power plant currently being built by Siemens in the German city of Düsseldorf, which is expected to be among the world’s most efficient and environment-friendly facilities of its kind. The Lausward power plant, named Block Fortuna, will replace an old coal-fired plant and will be a combined cycle gas turbine (CCGT) plant scheduled to enter service in 2016.
IN PICTURES: Inside Siemens power plant being built in Germany
READ MORE: Siemens sees opportunities in Middle East wind energy
READ MORE: Sisi in Germany as Siemens signs $9bn power deal with Egypt
READ MORE: Dubai’s DEWA awards Siemens $400m power plant contract
In combined cycle power plants, the gas turbine generates electrical energy and exhaust heat from the turbine is then used to generate steam. This then drives a steam turbine, generating additional electricity and increasing efficiency.
Companies are often eager to talk about how eco-friendly their operations are. Siemens, however, is going a step further and looking at breaking three world records for output and efficiency. The plant will have an electrical output of 595MW, the highest ever for a single combined cycle unit. Its net energy conversion efficiency will be over 61%, also a first, exceeding the previous record of 60.75% achieved by the Ulrich Hartmann CCGT plant in the town of Irsching in Bavaria.
Additionally, the Block Fortuna plant’s waste heat energy will be used for district heating in the city of Düsseldorf, further boosting its efficiency. The new plant will allow up to 300MW of thermal energy to be extracted for district heating (the third world record), raising the overall efficiency of the natural gas fuel to around 85%. Another advantage of the plant’s location on the banks of the Rhine is that river water can be used for cooling, further boosting efficiency, Siemens executives say.
When the tour bus finally reaches the power plant and the facility comes into sight, it’s unsurprisingly not the most visually appealing of structures at first glance. However, this will be addressed by the inclusion of an architectural highlight in the project designed by German firm kadawittfeldarchitektur: a glass tower that will be a ‘window’ to the city of Dusseldorf, open for public viewing and offering a bird’s eye view in the heart of the city.
Before the tour of the facility begins, we are given a comprehensive safety presentation. After all, on-site safety is taken very seriously at the power plant. Last October, the project celebrated more than a million working hours and 500 days with no reportable accidents or injuries. The track record continues this year, with an impressive 1.78 million working hours achieved without incident.
IN PICTURES: Inside Siemens power plant being built in Germany
READ MORE: Siemens sees opportunities in Middle East wind energy
READ MORE: Sisi in Germany as Siemens signs $9bn power deal with Egypt
READ MORE: Dubai’s DEWA awards Siemens $400m power plant contract
Once the safety presentation and Q&A session for journalists have concluded, the tour kicks off. It’s surprisingly quiet for a construction site, probably because the project is nearing completion and progress currently stands at about 95% complete, says Andreas Senzel, project manager for the site. Work is progressing smoothly, and roadwork is ongoing. The workforce currently on-site is about 150-200 people.
The client for the Lausward power plant is Stadtwerke Düsseldorf (SWD), a utility company founded 145 years ago. In 2012, SWD awarded Siemens Energy the order for turnkey erection of the Lausward plant, to be built at the Düsseldorf port on the existing Stadtwerke Düsseldorf power plant site.
After the old coal plant was demolished, the site was cleared and handed over in July 2013, since when work has been ongoing. The value of the contract awarded to Siemens, including long-term maintenance for the supplied components, is around $562 million.
The H-class turbine
While the exterior of the plant may not currently be too exciting, as with many other things, it’s what’s inside that counts. At the heart of the plant rests the latest in Siemens’ power generation technology: an SGT5-8000H gas turbine. The turbine, which is 13.2m long, 5m high and 5.5m wide, weighs 440t. For perspective, that’s as much as an Airbus A380 with full fuel tanks.
The gross power output of the H-class turbine is now 400MW, capable of providing electricity for more than 1.3 million people. In combined cycle mode with a steam turbine, however, the gross power output rises to 600MW, which can provide electricity to a population of over three million people.
Despite its power generation capacity, efficiency and sustainability are at the core of the turbine. Compared to previous combined-cycle power plant standards, the H-class can reduce CO2 emissions by 43,000t annually, the equivalent of taking over 10,000 cars off European roads. Moreover, the new generation of combined-cycle power plants needs about one-third less natural gas per generated kilowatt-hour than the global average of installed combined-cycle power plants.
The turbines are produced in Siemens’ factory in Berlin, which has delivered over 950 machines so far. Sixteen of the H-class turbines it manufactured are already in successful commercial operation worldwide. Alongside production, the Berlin factory also offers field and factory repair and maintenance, specialty services and diagnostic solutions.
From the Berlin factory, the turbine to be used in the Lausward plant was loaded onto a vessel and shipped along the Rhine to the Dusseldorf harbour – not an easy task, given its sheer size, Senzel says.
Besides the SGT5-8000H turbine, Siemens will also supply other main components as part of its contract: an SST5-5000 steam turbine, an SGen5-3000W generator and a Benson heat recovery steam generator.
IN PICTURES: Inside Siemens power plant being built in Germany
READ MORE: Siemens sees opportunities in Middle East wind energy
READ MORE: Sisi in Germany as Siemens signs $9bn power deal with Egypt
READ MORE: Dubai’s DEWA awards Siemens $400m power plant contract
Challenges
Although work on-site has been smooth, the project isn’t without its challenges. Building the power plant on the site of an earlier plant posed some constraints, Senzel acknowledges. The power plant had to be built on the narrow space occupied by its coal-fired predecessor. This affected the layout of the building and the efficiency of the design.
The high pressure steam pipes, for instance, have to be laid over a longer distance, which isn’t ideal. “The optimum arrangement would be to place the buildings as near as possible around in order to have short ways of the electrical lines, of the steam lines. But here in Lausward, we don’t have the place for it.”
Interestingly, however, one challenge that was anticipated but not actually faced was local resistance to the project, Senzel notes. Although there was initially resistance to plans to build another coal-fired power plant, the decision to build a gas-fired combined heat and power plant drew broad public and political support from the outset. Thus, subsequent efforts to reach out to the public and get them on-board were found to be unnecessary, proving to be a pleasant surprise for Siemens, he says with a smile as the tour draws to a close.
Project timeline for construction of the Lausward Power Plant
May 18, 2015: Gas turbine achieves first firing
May 30, 2014: Arrival of the gas turbine
February 26, 2014: Presentation of the gas turbine at the Siemens plant in Berlin
February 20, 2014: Presentation of the nearly finished steam turbine at the Siemens plant in Mühlheim
February 19, 2014: Installation of the surrounding walls of the heat-recovery boiler
January 8, 2014: Construction of the steel smokestack
January 8, 2014: Steel construction of the large machine floor
November 5, 2013: Construction of the stair tower
October 16, 2013: Completion of important foundations
July 31, 2013: Construction site handed over to Siemens
May 16, 2012: Stadtwerke Düsseldorf AG selects Siemens to build the facility
IN PICTURES: Inside Siemens power plant being built in Germany
READ MORE: Siemens sees opportunities in Middle East wind energy
READ MORE: Sisi in Germany as Siemens signs $9bn power deal with Egypt
READ MORE: Dubai’s DEWA awards Siemens $400m power plant contract
A long way since Gutenberg
The invention of the printing press in the 15th century was probably one of the most significant technological breakthroughs of the modern world. Centuries later, the process of printing is no longer confined to two dimensions, and 3D printing is increasingly finding applications across the board, even in the manufacture of gas turbines.
As turbines become more complex, their parts and components grow increasingly sophisticated. With 3D printing, shapes can be produced that would be impossible using traditional processes like casting and drilling, Siemens says. The German engineering firm is already using 3D printing to produce small parts for its turbines, which increases the speed with which components can be manufactured.
Someday, it may even be possible to print turbine blades with delicate internal air ducts, which would improve blade cooling. This permit higher temperatures in the combustion chamber and thereby increase efficiency.
In the process, a laser beam hits a bed of atomised metal powder, releasing high energy in the form of heat and melting the metal, layer by layer. The metal then cools relatively quickly into a solid shape. This is quicker than pouring hot, liquid metal into a mould and waiting for it to fully solidify and cool.
However, this is an advantage of conventional production methods, because slow cooling increases ductility. Researchers at Siemens are now working on processing techniques that would also endow 3D printed objects with high ductility – a requirement if turbine blades are ever to be printed. High ductility is required because of the high centrifugal forces acting on turbine blades.
Despite the limitations at the moment, it’s hard to deny that 3D printing is the way forward for Siemens. The process allows for rapid prototyping, repair and manufacturing. The time required for developing prototypes is cut by 75%, while repair times can be reduced by up to 90%, with cost savings of 30%.
IN PICTURES: Inside Siemens power plant being built in Germany
READ MORE: Siemens sees opportunities in Middle East wind energy
READ MORE: Sisi in Germany as Siemens signs $9bn power deal with Egypt
READ MORE: Dubai’s DEWA awards Siemens $400m power plant contract