Rockwell Automation serves up integrated strategy
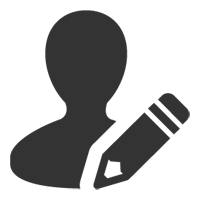
Rockwell Automation showcased its ability to deliver end-to-end projects for the oil and gas sector at ADIPEC 2014

In the Rockwell Automation stand at the Abu Dhabi International Petroleum Exhibition and Conference (ADIPEC) last month, the company’s vMonitor offering occupied the pride of place with its other signature product for the oil & gas sector, the PlantPAx.
vMonitor, one of the global technology leaders for wireless solutions in the oil and gas industry, was acquired by Rockwell Automation a little more than a year ago. The company’s technologies include an all-wireless portfolio of wellhead sensors and transmitters, RTUs, gateways and modems as well as turn-key monitoring and control systems and services. These offerings cover a broad range of applications from oil and gas wells, pipelines, pumping and lift stations, to refineries and tank farms.
The acquisition was intended to strengthen Rockwell Automation’s ability to deliver end-to-end projects to the oil and gas sector. At the time of the acquisition, vMonitor had the world’s largest installed base of wireless wellhead monitoring systems for natural and artificially lifted wells with more than 6,000 well sites for major oil and gas companies around the world.
While Rockwell Automation had successfully targeted the oil and gas upstream and midstream segments through its PlantPAx process automation system, the company never had a system at the well head. The vMonitor acquisition helped close that gap, and the technology is now a key component of the PlantPAx system.
Pankaj Shrivastava, Field Business Leader, Rockwell Automation said: “Once you automate the well heads and start collecting the data, you need tools to optimise that data, to understand whether the well is performing well, what decisions need to be taken. On the plant or downstream side, it is the same thing. You have to get data from the OEM skids for water treatment or oil treatment. All that data is actually available, transmitted and collected so that you can take action, and this is possible thanks to PlantPAx.”
vMonitor has been creating the digital oilfield with its extensive application knowhow inclusive of wireleslemetry, hardware, software, sensors and the ability to seamlessly integrate solutions.
“We have applications that have been developed for artificial lifts to optimise production,” said Khojema Netarwala, Engineering & Application Manager at Rockwell Automation. “They are suited for all kinds of wells like natural flowing, gas lift and Electric Submersible Pump (ESP) wells.”
In most oil wells, the well head information is taken manually, going into the system later in the day. That’s when the reservoir engineer gets to read the information and assess whether or not the well is performing followed by corrective action, with the entire process taking two-three days.
A digital oil field, on the other hand, is a real time system. It reads the real time data, takes decision on behalf of the operator and gives alarm to the operator on the action taken so that the operator can validate it.
“You can see the actual performance of the well, and if it is not optimised to the right conditions, then the system automatically gets it back to the correct range,” said Netarwala. “For each application, there is a certain criteria to get maximum production while maintaining the health of the pump. For example, for an ESP, there is an efficiency curve. So on the well head itself, the decision is made on whether the well is working is in the optimal range or is going out of it.”
He pointed out that the benefits of digital oil fields go beyond increases in production.
“In places where they have implemented the digital oil fields concept, production has increased from 8-10%,” says Netarwala. “But there are associated benefits as well in terms of security and better co-ordination.”
In conventional oil wells, if anything happens at the well head, unless there is a physical presence, operators don’t come to know about the threat. But the well head readings, transmitted wirelessly to the control room, can tell the operator whether the well is working or if there are issues. Also, digital oil fields also enable better coordination between production and maintenance departments.
Netarwala explained: “You can optimise your production by sending personnel only to those wells that need to be attended to rather than sending them out every day to the field, which helps optimise opex.”
vMonitor coupled with PlantPAx allows Rockwell Automation to offer a seamless integrated solution that meets the unique needs of the oil and gas industry.
PlantPAx has been designed to address the need of modern production facilities in the oil and gas industry, which require much higher flexibility through modular design and significantly higher levels of integration.
Rockwell has positioned PlantPAx as a modern DCS, which allows users to optimise their production, while helping to reducing risk and lower total cost of ownership. PlantPAx provides a scalable and modern DCS that allows the smaller systems used for small skids to be easily integrated.
Shrivastava explains: “End of the day, most of your I/Os are controlled not by the main DCS but by the skid packages. Where they come equipped with our system, it becomes easier for the end user to integrate those skids into the overall system.”
At the core of PlantPAx is Integrated Architecture, which makes integration a trouble-free affair.
Elaborating on the benefits of Integrated Architecture, Shrivastava said: “Irrespective of where you buy the system, there should be certain common elements across that platform which eases integration from an end user point of view. This is important from the end user’s standpoint because of the data lying in the plant. Earlier, it was difficult to access that data even if you wanted it. With Integrated Architecture, that data can be made available to the end user.”
Rockwell Automation supplies the tools needed to convert that data into information for the operator, supervisor and manager, who can then analyse that data and take decisions
As process control systems provide more and more options, information is key to translating this to meaningful information for the operators. PlantPAx can provide advance diagnostics and PID information to the operators in order to reduce MTTR (Mean Time To Repair) and improve production outputs.
Safety is an integral element of PlantPAx thanks to the trend of integrated control and safety. The electrical components – drives, soft starters, MCCs – are also totally integrated into the PlantPAx system. Advanced Process Control (APC) is also offered with PlantPAx through Pavilion Software.
Designed as an open platform, PlantPAx is available from either systems integrators or the Rockwell Automation solutions group, giving users a choice of partner. All PlantPAx components are standard, off-the-shelf products, with Logix hardware and software solution at the core.
Shrivastava said: “We can do the implementation for you or our system integrators or OEMs can do it for you. The end-user gets a wide choice as they are not tied down to a certain company.