Uphill Challenge
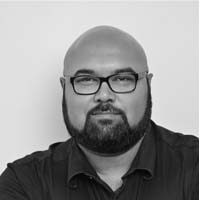
Big Project ME’s visit to the Alila Jabal Akhdar prior to its opening
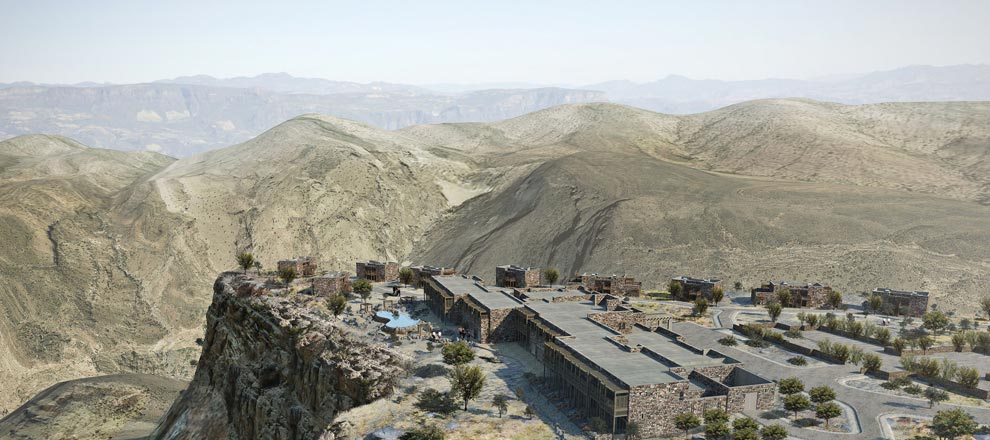
When visiting Oman, most travellers tend to focus on the Sultanate’s many spectacular beaches and pristine diving sites, others tend to be wowed by its ancient culture and landmarks. With its history in the region, Oman has always attracted visitors keen to explore its strange fusion of Arabia, Africa and South-East Asian cultures.
However, over the last decade or so, Oman has been quietly carving out a niche for itself as one of the world’s premier eco-tourism destinations, pushing forwards its credentials as a haven for critically endangered regional wildlife and the millennia old mountains that form its spine.
Following a drive of approximately three hours into the Hajjar Mountains, visitors to Jabal Akhdar will be treated to a landscape that is almost lunar in its nature, with the sense of science fiction enhanced by their first sight of the village of the same name. Clustered together on a plateau, the houses of the village overlook a sheer drop into a fantastical canyon.
This is why Big Project Middle East has come to the Sultanate. For it is here that Omran, the government backed tourism investment and development body, is building an eco-tourism project like no other in the Middle East.
Having identified the area as an attraction for visitors, the government of Oman has backed the development of a boutique hotel that is 2,600 metres above sea-level and well off the beaten path.
Situated a further 45 minute drive away from the village, the Alila Jabal Akhdar is an 86 room hotel that aims to offer its guests a sense of luxury and exclusivity, while also being able to enjoy Oman’s nature at its finest.
“We get a lot of visitors from Oman, the GCC and of course, Europe. So the government has invested a lot in enhancing the infrastructure. We had an evident lack of lodging facilities, it’s as simple as that. There was a hotel that was built in the late 1980s or early 90s, but it had something like 25 rooms. It used to serve the purpose, but there was definitely a demand (for more),” explains Ammar Al Kharussi, site manager for Omran on the project.
“So we started designing and developing the hotel (Alila Jabal Akhdar). We thought that if we were going to design a hotel, it would have to be world-renowned, it would have to be a landmark and we’d like it spoken of amongst the various industries, whether it’s tourism, construction, design or architecture,” he continues.
“We pushed the green button back in 2009 and started detailed design development. At the time, we relied heavily on Atkins for being the architect of record and the lead designers for structural and MEP. Besides that, they were kindly coordinating with our other designers for the kitchens, the IT, the laundry and so on.”
The contract for construction was awarded to Dawood Contracting, an Omani construction firm, on 6 December, 2011, Al Kharussi says.
“It was an exciting time because we didn’t know what we were facing. It’s three square kilometres of land and regardless of how many boreholes you have, you’ll never be able to fully understand the geotechnical features of the site. It was very challenging in terms of breaking the rock and preparing the infrastructure,” he highlights.
This difficulty in preparing the site is understandable, given that it lies nearly four hours away from the nearest major city. The man tasked with ensuring that the project stayed on track and running on time would have quite the job on his hands. Step forward Bijoy Varma, resident engineer for Atkins Oman.
“Construction was 24 months. It was supposed to be finished by December 20, 2013, but in fact, three months from the start of the project, the client gave additional work to the contractor for the back of house, staff accommodation. Because of that, the deadline was increased by three months, added to the original 24,” he explains.
While most projects with a two-year programme would expect to see the pace pick-up in the second year, Varma says that in this case, the project saw 50% of progress completed in the first year. This included excavation, substructure work, and concrete completion and so on.
“We finished back of house first, but this is a scattered construction site and all the fronts were open, so we were working on all fronts,” Varma adds, highlighting the urgency which the project progressed as it pushed to meet its deadline.
However, this urgency was almost scuppered by the fact that the remoteness of the site posed significant logistical challenges to the contractor, project manager and suppliers.
“Logistics was a very big challenge, the government itself wouldn’t allow more than four trips of a trailer coming up. They’d allow only four trips of a big trailer, and that was only at night, not during the day hours. It was complex, and we had to have a specific logistics manager (to resolve issues).
“There was also the problem of getting concrete supplied because there was no concrete ready-mix plants at the top of the mountain. We had to get it from a place down below and it’s a road with many twists and turns, so with mixers and trucks coming in… it was quite difficult to manage things,” he recollects, putting it rather diplomatically.
“Another issue was getting water. Even if it rains at the top of the mountain, the water will always run down. Only a little water will remain and that’s preserved for the local people who still live around here, so we needed to get water shipped up from down the mountain.”
“Furthermore, only four-wheel drive vehicles were allowed, so that meant that we had to train people how to drive them,” he adds, pointing out that working in the area is so challenging, there have been stories about individuals on other projects quitting outright, rather than taking on a project in Jabal Akhdar.
Someone who might whole-heartedly agree with this sentiment is Talal Ahmed Al Shizawi, CEO of Dawood Contracting, the Omani contractor appointed to the Alila Jabal Akhdar project.
“This was our first five-star hotel project. We’re a local Omani company, so we did a joint-venture with HLG (to work on this project). All the manpower and equipment was from our side, the only thing from them was support for us in project management. We had two people from them, the project manager and the logistics manager,” he explains.
“You know about the location of the project, you can see it’s very difficult, and this was a first for us! We’ve done other kinds of projects – offices, residences and commercial buildings – but this was something different,
“To start with, it was very difficult because of the height of the site and also the weather. (This) and transportation was very difficult, even though the construction itself was nothing out of the ordinary. We couldn’t work in 24 hour shifts, especially during winter. During the day, you’ll feel cold, so what about at night when sometimes temperatures would reach -1o degrees?” he asks, not unreasonably.
“During summer, we worked from 6:30AM to 6:00PM. We then kept some teams, not all of them, to finish a task for the day and to give work for other teams the next day. So you could say that work would continue up to the maximum of 10:00PM during the summer. But in winter, we finished at 8:30PM. We have to look after our labour and get them to take rest also, we could not give them more than their capacity,” he asserts.
With 600 staff onsite, managing the shifts, worker accommodation and health and safety, was another challenge for the project management team. Given that trips up and down the mountain would have been time consuming, the team decided to house the labour force on the mountain itself, setting up a camp near the project site. This had the benefit of allowing construction to continue with minimal interruptions.
“There was a half hour break for breakfast at 9:00AM, then it was back to work till 12:30PM or 1:00PM when there was an hour and a half break for lunch and then back to work. At peak, with 600 men onsite, you can’t take them for one and a half hours (together). So what we did was stagger the teams, so that everyone got one and a half hours of rest. On Fridays, sometimes we wouldn’twork, but that depended on progress. We did try to give Fridays as a rest day,” Al Shizawi says.
“From day one, we had logistical challenges,” he adds. “(It centred on) how to take materials from down below to the site. I’ll give you an example: “A truck with 18 cubic metres of capacity, on level ground, it’ll take 18 cubic metres, but to bring that load up here will require two trucks because each truck will only take half the amount. It means that the transportation price is doubled, and that’s just for one item!”
Although they solved this by purchasing their own vehicles and cutting down on rental costs, Al Shizawi and Verma’s problems continued to mount as construction progressed.
“The second problem was ready-mix, it just wasn’t available here. We solved that by working with a company doing road-works nearby. They supplied us, but at the same time, the asking price was always a problem. It was 50% to 80% more.”
On top of all these logistical problems, the team was faced with other challenges. Given that the project was built around an ecological theme, and was in a protected area, the government had given clear instructions that the surrounding area be undisturbed, as much as possible.
Couple that with the sheer drops on either side of the cliff, the project management team had to ensure that the heavy machinery and labour could move freely and safely around the site, while also making sure that the flora and fauna around the site remained undamaged.
“We decided to use a surgical approach,” explains S Masood Raza, the principal architect on the project, from Atkins Oman.
“That means that we didn’t want to do too much to change the landscape, just do what is the minimum required and get it right. If we did mass-scale changes to the site, then it would have spoilt the illusion. So it was a careful balance for the strategy that was to be adopted.”
“There was a safe building line, which was assessed by the slope stability people. So from the edge of the cliff, we needed to leave 20m (for example). If went nearer, then the mitigation majors would have been too much. So the best outcome was to leave 20 metres from the edge and then start building the foundations, so as to have minimum impact to the existing terrain,” he explains, highlighting the care taken to protect the natural flora and fauna.
“There was a site disturbance boundary,” Varma adds. “That’s what we had to protect against the disturbance of the other areas. So all our construction was restricted within this particular boundary.”
He added that since the project is aiming for LEED certification, this approach was crucial, and it had to be reinforced to the staff, with regular safety inductions and lectures being held. This careful approach will also carry over to the guests, with the hotel now open.
“In terms of guest experience, we had a landscape architect working with us. What they did was develop perimeter fencing all the way around, because it’s a very deep fall. It was done with wood and cleats, so as not to obstruct the view. This also keeps wildlife out of the hotel area, for the most part. These safety measures were required from the Royal Oman Police to protect the guests and for municipality approval as well,” Raza chimes in.
The team was committed to using natural materials. This included the rocks they excavated, the use of locally sourced timber and other materials, as the architect explains.
“The vision was to have an Omani version of an alpine resort and a boutique hotel that survives on the service and the locality. It will also create jobs for the local people, use local materials such as the stone that we’ve used, which is all from the local mountain region and is recycled.
“We analysed some of the villages, the use of timber for the railings and the lintels, and how they used large format stones underneath and smaller stones above. This (inspiration) was already there,” he says.
“What we did was take it and do it in a more contemporary way. In a way, we’ve promoted local architecture. And I must say that the local people really appreciate this project. We have not done a ‘skin deep’ thing, it’s not just cladding. The stones in our walls, they are load-bearing because they transfer the load to the foundation. It’s only for bracing – for wind-loads and seismic bracing – that they’re laterally supported by wall ties and on the stud-work at the back. It may look really ‘village-like’ and old, but inside it’s really high-tech and modern, and that’s because we blended it in such a way,” he asserts, highlighting the depth of research and commitment that went into putting this most special of projects together
“My team, the consultants, the subcontractors and the client – everyone felt like this was this baby,” Al Shizawi sums up in conclusion.