Germany construction technology
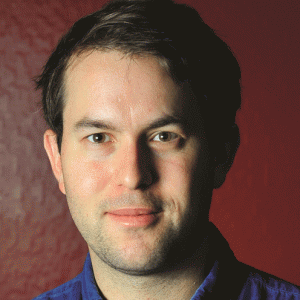
In the globalised world of construction machinery and heavy vehicles manufacturing, do German companies retain a technological edge? CMME finds out.

We have reached the moment where you can step on to a factory floor in almost any country in the world and see ultramodern processes building products to the highest standards.
In the consumer markets it seems the remnants of the stigma around the ‘Made in China’ label have faded, with prime examples of accepted items being Apple and Samsung smartphones. And in the construction machinery industry many of the most modern factories in the world are found in China, partly because these factories are newer than those built many years ago in Europe, Japan, North America and elsewhere.
There are also major clusters of high-tech vehicle and component manufacturing in countries such as Thailand, Mexico, and Indonesia.
And so while it may not be so important to consider in which country a particular machine model was produced, or even in which country sits the ownership structure of a brand, the best-known construction machinery manufacturers have a long history of research and design, a specific culture, and a recognised value alignment for their products. And German brands have been in the thick of it, engineering high tech and durable products that have been well-received in the harsh operating environments across the GCC and Middle East.
German manufacturers in the industry include major brands such as Liebherr, Putzmeister, Wirtgen Group, excavation specialists Bauer and Wacker Neuson.
Each has their own niche and approach, but it can be said that there is one feature that is common to them all: the need to remain competitive, both against other premium brands, as well as being competitive in newer markets where buyers are more price sensitive. There are several major trends being played out within the manufacturing worldwide especially the construction machinery industry.
Across the spectrum you can see consolidation of multiple business lines within established companies; refining of premium products to reduce total cost of ownership and improve performance and servicing; and the launching by premium brands of ‘value’ products to remain competitive against the less expensive brands from China and other markets such as Korea and Turkey.
Both are seen as necessary to survive in the competitive market place.
Last month, Wirtgen Group announced that it had acquired a 70% share in a German company specialising in the production of asphalt mixing plants, Benninghoven. Wirtgen Group is a major manufacturer of road building, surface millers and crushers, concrete and compaction equipment, translating into the well-known brands of Hamm, Voegele, Wirtgen and Kleemanns, equipment that can be see across the region, whether in road building, port construction, or quarrying and mining. But with the addition of a asphalt mixing plants, it now offers a complete product range across an entire material process chain, or its own words, “a complete solution for customers including all processes starting with the crushing of rocks, through to the mixing of asphalt to laying, compacting and rehabilitating pavement structures”.
World-wide there are 55 subsidaries and 150 dealers for Wirtgen Group’s brands, including GENAVCO in the UAE (Hamm, Voegele and Wirtgen) and Bakheet in Saudi Arabia (Hamm, Voegele and Wirtgen), and it is these dealers which will “step by step” open new markets for Benninghoven.
This strategic acquisition should come as no surprise to industry insiders, as many companies pursue a ‘full liner’ approach.
Other recent acquisitions include Liebherr’s purchasing of a concrete pump manufacturer in 2012, and Putzmeister’s acquisition of a concrete batching plant manufacturer in 2013, and a mixer trucker builder the previous year.
Similarly, Swiss company Ammann Group announced the acquisition of a concrete plant manufacturer earlier this year.
Moves to expanding a product line have advantages for customers; as acquired brands are often full or partially engineered to improve spare parts and componentry commonality; and the previously-small brands then benefit from a rigorous and expanded aftermarket service.
After Liebherr acquired pump manufacturer Waitzinger in 2012, it then embarked on a programme to refine and improve the product. It culminated in the launch earlier this year of a new 37 metre truckmounted concrete pump, the 37 R4 XXT.
The German-built pump has a four-section, rollfold distributor boom has a reach of 37m, and can be equipped with pump units featuring three different outputs ranging from 125 m³/h to 163 m³/h.
Built over four axles, with a THP 140 H pump, it features a Liebherr-patented XXT-narrow outrigger, and an extremely torsional-resistant boom, which ensures reduced vibrations when manoeuvring the boom during onsite applications. To reduce complexity and cost, the pipe bends are predominantly of the same type, minimising the need to stock diverse replacement parts. Numerous design-related features optimise servicing tasks by simplifying the replacement of wear parts.
Putzmeister celebrated the handing over of its first M 56-5 concrete pump in Dubai, to Al Ghurair Construction Readymix LLC, in a ceremony held at the facility of its UAE dealer, German Gulf Enterprises (it is also marked a significant coup over its German rival and long-term supplier to Al Ghurair, Schwing).
The M 56-5 is part of Putzmeister’s new range of concrete truck pumps (including 36m, 42m, and the 56m booms), which it has been completely redesigned.
With fierce price competition, the 56 metre boom pump is built over only four axles, rather than the five which would be customary in this boom class, which saves the customer considerable money, since a major cost of a truck mounted pump is the truck itself, and each additional axle multiplies that cost.
And Putzmeister claims that its M56-5 is the longest boom on four axles.
Other engineering features of the new range of pumps, designed to save customers’ money, is reduction in the number of types of elbows, higher commonality of spare parts, a design with a preference for bolts over welds, and the use of less hydraulic fluids.It’s well-known that durability is one of the most important product attributes in the GCC, if not the most important. And it’s proven at auction: with brands that are long-working selling at higher prices. Thus it is that simplicity over complexity, and hydraulics over electrics, can be a boost for a machine’s desirability for buyers in the region. One German manufacturer that has taken this to heart is Sennebogen, which builds mobile cranes, port and material handling products. It specialises in cranes where hydraulics are utilised with preference over electronics.
The company’s 673R is a telescoping crawler crane, with a 36m four section boom, with a maximum lift weight of 72 tonnes, as well as jib and fly extensions up to 15 metres with 0°/20°/40° offset angles. The four stage hydraulic boom is continuously telescoping.
Using a telescoping crawler rather than lattice boom means a faster set up time on site, and more site flexibility, such as retracting the boom when travelling underneath a bridge or obstacle. For pick and carry it can travel under up to 90% of its maximum load.
It also boasts fast set up time, and improved transportability, including a track gauge of 4.1m, yet only 3m transport width, with extendable telescopic crawler pads. And for a mobile crane, especially in the rental sector, faster rigging time means improved utilisation and job site performance, and ultimately more jobs per year. As far as maintenance is concerned, the 673R has a central lubrication point covering the slewing ring, boom pivot point and rocker cylinder.
With some of the most architecturally exciting projects in the world being executed in the Gulf, special requirements can emerge for equipment, where German companies have been known to step in. Putzmeister still hold the world record for the highest vertical concrete pumping height, of 606m, carried out by a special 14000 SHP D super high pressure concrete pump, used by a local ready mix company, Unimix.
And on the Kingdom Tower site in Jeddah, currently under construction Bauer, a company headquartered in the Bavarian town of Schrobenhausen in southern Germany, trenching machines were used to lay the foundations for what will be the tallest building in the world.
Bauer, through its contracting arm Saudi Bauer Foundation Contractors, sank 70 piles to a depth of 109m, at 1,500mm and 1,800mm in diameter. It also installed 200 further piles at lengths up to 90m.
Schwing, which hails from the ‘land of coal and steel’ state, Westphalia, was announced as the concrete equipment supplier to the project last year at the Bauma trade fair in Munich. The new Schwing SP 8800 Container stationary pump will be used, and up to a total of five other stationary concrete pumps and four separate placing booms from Schwing will be in action.
Whether the Kingdom Tower will result in a new record for vertical concrete pumping remains to be seen, but is likely given the tower’s expected height of one kilometre, another chance for German manufacturers to prove the performance value of their products