Piping Hot – Oil and Gas equipment review
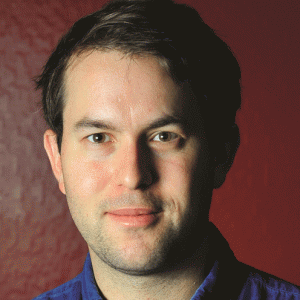
Whether upstream or downstream, pipelines projects are of critical and national significance in the Middle East, and for contractors looking to buy pipelaying equipment there are plenty of options whether buying new or used, writes Stian Overdahl
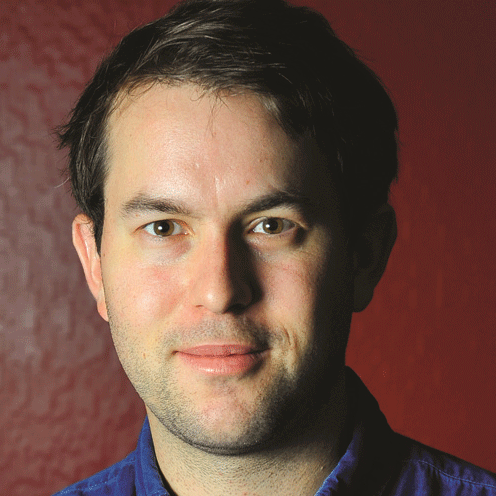

Volvo will follow up the PL4608 and PL4611 with the PL3005D which will launched for the Middle East at the end of this year
Whether upstream or downstream, pipelines projects are of critical and national significance in the Middle East, and for contractors looking to buy pipelaying equipment there are plenty of options whether buying new or used, writes Stian Overdahl
In recent years the Gulf has seen a number of major pipeline projects, including in the United Arab Emirates, Oman, and Saudi Arabia, and wider afield there are major pipeline projects in Iraq. Nevertheless it is market dominated by large projects, and completion of a project can spell idle time for machines. It all adds up to an interesting market dynamic, with sellers of new machines offering improved reliability or even entirely different functionality, while the market for used machines remains buoyant.
At the pipe-laying end of a job site’s work flow, crawler tractor side booms have long been the dominant piece of equipment used. Mounted on a crawler tractor type undercarriage, these feature a sideboom and counterweights, with the boom operating on a single axis of movement. Caterpillar is the most sought after marque in this segment, along with Komatsu, and there are also offerings from Liebherr.
More recently Chinese manufacturers, including Shantui and LiuGong, entered the market in the Middle East. Activity at auction sites in the UAE suggests a busy second hand market too, including a sale at Ritchie Brothers in Dubai in December last year with 62 sideboom PLs, as a single company disposed of its entire fleet. Ages range to 30-40 years, or beyond, and Caterpillar machines, followed by Komatsu, dominate the sales lists.
Marco Jannuzzi, pipeline manager for Caterpillar, and Caterpillar’s representative on the Board of Directors IPLOCA (International Pipe Line and Offshore Contractors Association), says there are multiple reasons why so many Cat PLs change hands in the used market.
“First of all, the population of Caterpillar pipelayers is by far the largest compared to any other manufacturer, therefore it is logical that you see more Cat than other brands. Secondly, the durability of Cat pipelayers is truly outstanding.
“Clearly, during such long useful lives, these machines change owners many times, probably six or seven times, and often this operation is handled through auction houses. However, as many Cat pipelayers as you may see at auction houses, the vast majority of these machines are actually at work on projects and jobsites!”
On the question of aftermarket service and support, Jannuzzi says that Caterpillar dealers are well equipped to support the pipeline industry.
“Caterpillar stocks spare parts for ten years after a model has been discontinued. For older Cat pipelayers, our specialised, global pipeline dealer, PipeLine Machinery Inc. can provide older spare parts out of their inventory, or as made per order.”
With project duration generally between six-18 months, machines will often seen intensive use, followed by a period of idle time as contractors wait for the next job. This time is often used for scheduled regular or preventive maintenance and service, he says.
“For pipeline projects in particular, which are generally in remote areas, machine up-time is critical to avoid catastrophic delays and costs. It is therefore not by chance that the vast majority of contractors prefer Cat pipelayers which have the best reliability and the most effective dealer network.”
On the resale value of used machines, Keith Lupton, VP of regional sales at World Wide Auctioneers (WWA), says that even on older machines prices hold up well.
Vivid examples are a 1949 D7 Caterpillar crawler pipelayer which sold for $8,000 in July this year at a Ritchie Bros auction in Dubai, and a 1946 D7 pipelayer selling at the same auction for $5,500.
“When the pipeline contracts go quiet many operators keep their machines lying waiting for the next up swing in the market, and the older machines are still doing the business. Larger units, despite their age are doing big dollars,” says Lupton.
Despite the age of machines, many side booms will not rack up large hours, compared with standard earth-moving equipment, as they are moving only alongside the pipe trench, which is not a high wear and tear action.
When apprising used machines, undercarriage condition and draw works condition are paramount in the buyers’ mind, says Lupton, as well as looking for good clutches, as the pads usually have a long life. Also available for contractors is the option of converting a standard crawler tractor into a side-boom pipe layer with a retrofitted kit. The best known provider is Midwestern, which introduced the world’s first hydraulically operated sideboom pipelayer attachment in 1953, and since then has provided thousands of pipe layer attachments. The sidebooms fit on Caterpillar, John Deere, Case, and Komatsu tractors, with lifting capacity from 4 to 104 metric tons. In the UAE, Global Pipeline Supplies, based in Jebel Ali, has operated a pipe-layer conversion programme since 2005, with more than 50 Caterpillar crawler tractors (D7G, D8K and D9H) converted into fully hydraulic drive pipe-layers using Midwestern kits.
Machines are prepared (bare tractor rebuilt works and hydraulic kit installation) in the company’s workshop, and tested by a third party institute to verify compliance with the requirements of applicable international standards for side-boom tractors.
According to the company, converted pipe-layers provide equivalent lifting capacities to the same classes of Caterpillar factory made units.
Lupton notes that from a used machinery perspective, there is a price premium on original machine built as side boom by Cat, “as the stress is designed for side operation, whereas a D8 dozer frame design is designed for stress traveling front to rear of the frame”.
Commenting generally on used Cat sideboom machines, Jannuzzi says that the company does not condone ad hoc modifications: “In some cases, there have been contractors or local workshops who have converted old bulldozers into pipelayers, and we have seen this type of machines for sale at auction houses or equipment brokers.
“Caterpillar does not encourage nor recommends this practice, because a machine modified from its original design will not perform as an original one, in terms of work capability, performance and most importantly safety. This practice is also reflected in the lower value that converted or modified machines can obtain at auctions.”
Meanwhile, challenging the dominant orthodoxy of the crawler tractor sideboom is Volvo Construction Equipment’s range of pipelayers, which are based on an excavator undercarriage, and offer 360 rotation for the boom. First rolled out in North America and then globally, the machines are used in markets as diverse as Papua New Guinea, Sweden and the UAE.
The machines feature a number of innovative design features that Frank Schmitt, pipeline business development manager, international region at
Volvo CE, says significantly improve contractor work practices, both in terms of efficiency and safety.
Notably the upper structure swing is put to good use when traversing hilly terrain while carrying a pipe length. Swinging the boom to the front of the machine while carrying a pipe allows the centre of gravity of the machien to be balanced, compared to side booms which have a single axis of boom movement, and one which, while on a slope, the pipe will swing away, or down, from the centre of the machine. The design allows the Volvo machines to work on grades of up to 35O, and they have the highest tipping capacity for the segment in each of their respective size classes. Performance features include elevating cabins (a favourite with operators), as well as a factory fitted load management system, which uses in-built sensors with a simple green-amber-red ‘traffic light’ warning system, visible from both an LCD screen within the cab, and from outside the machine with lights place on the boom.
This means that adjacent machine operators on the line can take more of the load if one machine goes to red. The biggest significance however is to the laying in, where the foreman and linesman can watch the boom lights, and direct the action based on where he sees any difficulty cropping up in terms of balancing the load along the line. Another advantage of the machine says Schmitt is faster set up time, especially important when there is a site with a lot of crossings, where machines have to be disassembled, transported and then reassembled. The machine itself is also able to be converted into a normal Volvo excavator in a single day’s work by two mechanics.
In the Middle East the PL4608 and PL4611 pipelayer are available, 80 and 110 tonne respective capacity models. The number of projects needing machines of this size is limited, says Schmitt, though already there are units working in Oman, UAE, and Iraq.
Rolled out last year elsewhere, the PL3005D will launched for the Middle East at the end of this year with a Tier 3 engine, with the model going into production in Q4. Schmitt says that customer indications are that the PL3005D will be eagerly received, with its 50 tonne rated capacity. This machine will be suitable for pipeline projects up to 36 diameter, which is quite a lot of pipelines, including oil, smaller pipelines going in or out of refineries or processing plants, as well as in countries where there are not huge resources, such as Oman. The shift to Al-Futtaim Auto and Machinery Co. (FAMCO) distributing Volvo CE in Saudi Arabia, with an emphasis on widening the support network and increased levels of service, opens the market there, and Schmitt expects that they will see greater activity in the Kingdom.
“After the reorganisation we feel absolutely at the right level now to secure the aftermarket support for these pipelaying contractors.”
The efforts will kick off by showing Volvo CE pipelayer concept at the SAOGE (Saudi Arabia Oil and Gas Exhibition) taking place this year in Dharan, in Eastern Province, along with FAMCO, which will include live demonstrations modeled on the show at Bauma earlier this year, and the new PL3005D.
“We feel and we are 100% sure that we will significantly increase the population in the Middle East with this machine.”
Globally pipeline diameters have been rising, and Lupton says that in the second hand market, for a long time the main swing has been away from ‘D6’ and ‘D 7’ size units for the ‘D9’ size to cope with the larger diameter pipes.
“This over the years has been the major change certainly in the second hand market. At one time D9 size were most difficult to sell once a job had finished, now it is the other way around.”
Last year Caterpillar updated its PL range, launching the new PL83 and PL87 models, with respective lift capacities of 72.5 and 97t, in addition to its smaller 18.1t model, the PL61. Jannuzzi says that the upgrades were very well accepted by contractors, simply because the improvements introduced with these new models were coming directly from customer suggestions and comments. Both models were boosted to larger capacities than the previous iterations. While used machines are obviously popular, with reliability and machine up-time critical on pipeline projects, contractors continuously add new machines, he says.
“Contrary to older models, new machines also meet the most stringent and updated requirements on safety, operator environment and engine emissions. In addition, they are much more fuel efficient than older models, and come equipped with high-tech devices such as Cat Product Link, which allows remote equipment management by the contractor.”
Going forwards, Jannuzzi expects that tech options will play an increasingly large role in the pipelaying industry.
“The big shift I see is in the application of technology, including machines which are used on pipeline projects. Product Link provides remote access to vital machine data (its exact location, plus data on key components).
“The Connected Worksite technology allows electronic management of entire fleets of machines, which improves jobsite efficiency enormously and reduce contractors’ cost dramatically.”