A Material World
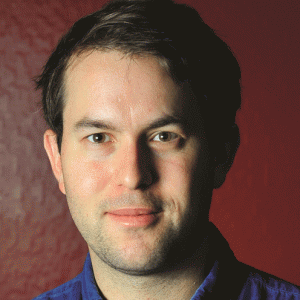
The quarry and mining sector in the Middle East is in good health, especially following the recovery of the construction sector with increased demands for aggregates, discovers CMME International Editor Stian Overdahl


Emilio Lens, business development director – emerging markets at Terex Finlay, says that they have seen business pick up in the past 12 months
Quarrying and mining are among the oldest of human industrial activities, and the Gulf nations possess significant deposits of valuable materials, from gabbro and limestone in the UAE, stones, gypsum and copper in Oman, and aluminium, gold, phosphate and other minerals in Saudi Arabia.
Servicing this market are a formidable group of equipment manufacturers, but as lucrative as mineral and aggregate extraction can be, there are heavy demands on the machinery, with long working hours, high tonnage rates, and hot and dusty conditions just par for the course.
For the quarrying of aggregates, where one of the primary uses is construction and infrastructure, the drop off in activity in the UAE after the 2009 crash saw the price of aggregate in the Emirate fall to levels that were almost not sustainable for producers, especially at the smaller sites. Where larger quarries often have a lower production cost, they can also benefit from a more diverse customer base, and the steel industry in India is a major buyer of high quality limestone from the UAE.
With the high levels of investment in infrastructure and construction project in Saudi Arabia, the industry there did not experience the same drop-off, and indeed Saudi ceased supplying materials to Qatar in order to meet its domestic market demand. With the construction market in the UAE having recovered, and increased demand for raw material in Qatar, and continued high levels of demand in KSA, has seen prices recover to a level where many quarry operators are again looking at investing in new machines.
Emilio Lens, business development director – emerging markets at Terex Finlay, says that they have seen business pick up in the past 12 months – with confidence in the UAE, Oman, and Saudi Arabia. The company produces a range of mobile, tracked crushers and screens, and thus seeks to convince quarry operators of the benefits of using a mobile plant located at the blast face, as opposed to a static plant, which are generally located at the bottom of the quarry. A mobile crusher can be loaded directly at the quarry face.
Lens says they’re seeing a transition towards mobile plant by many quarry operators, following trends elsewhere in other markets including Europe. He believes it’s a natural trend as a quarry market develops, rather than being a move forced on operators by lower prices. Mobile plant can also be sold second hand, while a static plant is less easily sold to a new user. Mobile machines generally have a lower capacity than a large static plant, and so the advantages of fixed versus static will depend on an quarry’s production goals.
Key models for Terex Finlay in the region are the I110, I130 impact crushers, and the 694 screen. With a transport weight of 49,000kg, the I130 incorporates an impact chamber with direct drive and advanced electronic control system. A large hopper features a variable speed pan feeder and independent pre-screen with constant RPM for optimum separation even if feeder speed is reduced. The benefits for operators include high material reductions ratios and the production of a consistent product shape.
Another seller of crusher and screens seeing an increased uptake in mobile plant is Qatar-based Agg-Pro, while sells McKloskey and Gipo brands.
“Most track mounted machines are sold onto construction sites or allocated rock deposits close to a specific road project. These are short term projects and the mobility is key factor. Mobility allows for easy planning permission, ease of moving around the site and also to another project after the initial project is finished,” explains general manager Charlie Eastwood.
Nevertheless, with a with a combination of the lower initial cost of a fixed crusher and low fuel prices for the quarry trucks compared with Europe, the static crusher concept is popular in the Middle East.
“It has been challenging to change the mind-set of the quarry owner,” says Eastwood. “But we are seeing more and more Arab quarry owners visiting European exhibitions and a few are embracing the long term benefits of the track mounted crushers and screens for quarry operations.”
They have seen recent success in Saudi Arabia, selling a mobile impact crusher and S190-3 triple deck screen to Dammam, where the customer has been happy with the result and is considering two additional set-ups. And with the quarries closed in the Jeddah area, new quarries have been opened 200km from the city. Eastwood says that they have also recently secured a deal for a large primary jaw crusher, two cone crushers and three S190 screening plants for one of the new sites.
“The mobile machines will help open up the new quarry and we feel this will start a trend for track mounted crushers and screens in this region of Saudi Arabia where fixed crushers have been the norm.”
Rock conditions in the Middle East vary, but can in some areas be very hard, requiring special solutions. In Qatar, some areas have rock strengths as high 150Mp, and Eastwood says that they’re able to offer equipment to suit the customer’s end use.
“Depending on each contractor’s specific requirement and the rock type being processed, we offer a variety of crushers from our heavy duty jaw and impactor range. We would offer a jaw if the requirement is a large course product 0-180mm for example or if the customer wanted to maximise on small aggregate we have used jaw crushers as a primary crusher then feed the crushed rock into a secondary impact crusher.
“We also have a range of heavy duty primary impactors which we have used for high tonnages and where a specific gradation is also required, usually for a high quality sub base required for a major highway.”
In Egypt, Sandvik Construction recently implemented a solution at a quarry where highly abrasive aggregate is being processed – a very hard 99% Silica rock, which was hard wearing on the liners of the cones of the Sandvik CH 430 and CH 440 stationary cone crushers in use, at a site owned by Rodan Group. With 150 mtph production, the liners were lasting an average of only twelve days of continuous fifteen hours daily operation.
Through its local dealer, Stallion for Investment Co, Sandvik supplied a Flexifeed mantle, which allows for a more efficient crushing operation through its chamber design.
With the Flexifeed mantle installed the crusher is able to accept over-sized material in part of the chamber, while reducing the chamber profile in the opposing part of the chamber, permitting operation at a tighter setting, for a finer product being produced on a ‘first pass basis’.
“On the CH440 the liners lasted a great deal longer, even though the Flexifeed is a heavier mantle with more material in it. Based on our advice the customer used to operate their jaw and a cone at any given time so we were able to switch between the CH430 and the CH440 whenever the liners wore down, thereby giving us time to change the liners of one cone while the other was operating, thereby providing almost continuous production,” said Tarek Youssef, general manager at Stallion.
“The difference the mantle makes is essentially improved crushing efficiency. That means, in simple terms, we get better productivity and lower cost per tonne.”
For sellers of mobile equipment such as loaders and excavators, a slow down in the quarry business typically means that customers will seek to extend life cycles of their machines, and hold off on new purchases. Following the drop in activity in the Emirates, Caterpillar saw a lengthening of the replacement cycle for quarry equipment there. Nevertheless, customers were able to look at rebuilding their machines through the company’s certified rebuild programme. The requirements of individual machines are determined prior to disassembly through an evaluation of the machine. The rebuild can then include automatic replacement of parts such as hoses, belts, seals, gaskets, bearings, knobs, wiring, switches and gauges. Machines can also benefit from technological and engineering improvements that have been made since the original model launch, while retrofit packages are available to bring new features to older machines.
The operating hours on some of these machines can be staggering, with the Caterpillar load and haul equipment such as large wheel loaders and off-highway trucks, designed to last through multiple lives, with chassis designed to deliver over 40,000 hours and allow multiple power train rebuilds. As an example, the highest recorded service meter hours for a 773 off-highway truck is 213,000h. For a 988 wheel loader, it is not unusual to find units with more than 50,000 service meter hours.
In the competitive market for quarry machines, manufacturers who have a full range can point out the benefits of using both a loader and a dump truck, since the heights and capacities are often well-fitted. For example, Caterpillar has newly launched its 986H loader, designed to be used with the 772 rigid truck. The larger 988, now its its 50th year of production with the new –K model, is fitted to the 775 rigid truck.
The number of companies producing extremely large mining trucks is relatively small, and so Volvo CE’s planned acquisition of Terex’s hauler business unit will be watched with interest.