From ship to shore: Port Tech
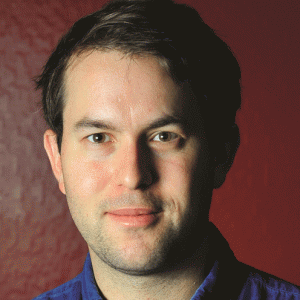
Across the the GCC signficant investment is being made building new ports or expanding existing operations, as economies are diversified beyond oil and gas. The scale of investment should have sellers of equipment to the sector salivating, but are demanding and choosy customers. CMME International Editor Stian Overdahl investigates.
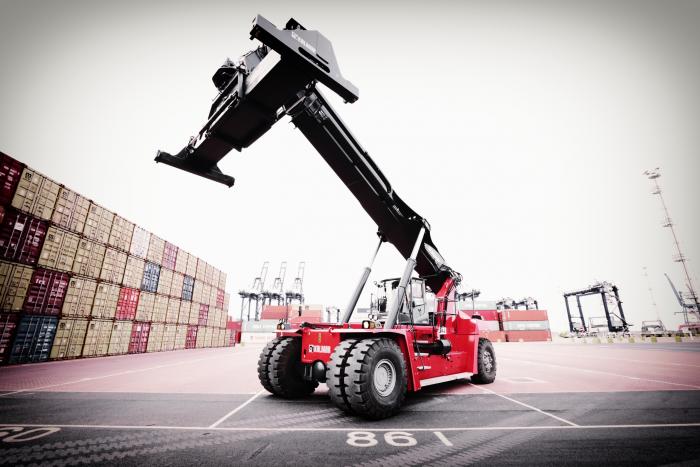
Ports have long been a lifeblood for coastal cities in the desertous GCC nations, and more recently have played a pivotal role in their economic development. Dubai’s Jebel Ali Port plays a major role in the history of the Emirate’s stratospheric growth since it opened in 1979, while Jeddah’s seaport has been able to take advantage of the city’s strategic location on the East-West transshipment route through the Suez Canal.
Currently there is significant investment in the port sector, as existing ports expand their capacity, and new ports open, including, in January of this year, the region’s newest port, King Abdullah Port (KAP), north of Jeddah in King Abdullah Economic City (KAEC). And this is being matched by on-shore developments, include building of rail links with the new GCC rail network, landbridges, as well as the development of new industrial zones such as KIZAD in Abu Dhabi and KAEC. With a steady flow of containers and cargo into the region, the major ship to shore (STS) crane are at the coal face of unloading docking ships, ships that are growing steadily in size. The largest supplier of ship to shore (STS) cranes in the world is Shanghai’s Zhenhua Port Machinery Company (ZPMC), a consequence its economy of scale, and direct access to cheaper steel than is available in Europe, which is the major cost determinant in a crane weighing nearly 2000 tonnes.
Barely a month goes by without announcement of a new delivery by ZPMC to the region. Jebel Ali received four new STS cranes in December from the Shanghai yard, the first of a batch of 19 to be supplied to the new Terminal 3. Once the order is filled, Jebel Ali will have a total of 98 STSs. And in January, Abu Dhabi Ports Company (ADPC) added another three to their existing six at the new Khalifa Port, at a cost of $28 million.
Each super-post-Panamax STS crane is 126.5 metres high and weighs 1,932 tonnes, while it has an outreach of 65 metres (equivalent to 22 containers) and a lifting capacity of 90 tonnes. With nine STSs, the port can now handle up to 315 containers per hour (35 containers per crane, per hour). The port is currently receiving vessels with capacity of up to 14,000 TEU (twenty-foot equivalent unit).
Other STS suppliers include Liebherr, which secured a contract to supply three cranes to King Abdullah Port. The Germany manufacturer has also supplied a mobile harbour crane, and 22 rubber tyre gantry cranes (RTG). Liebherr’s RTG have a hoisting height of 1-over-6 containers, are eight containers wide plus the truck lane, and have a maximum 64 tonnes twin lift. A major point of difference for the German supplier is its unique hoist rope reeving arrangement which results in extremely effective no-sway operation in trolley travel, gantry travel and load skew directions. Liebherr believes its RTGs regularly achieve throughput figures which are 35%–40% higher than those of RTGs with a conventional 2-fall vertical rope reeving arrangement.
At the Khalifa Port in Abu Dhabi, both the gantry cranes and the stacking cranes are rail mounted, an infrastructural design feature aimed at a long life with low maintenance costs. When it commenced operations in September 2012, Khalifa Port was the first semi-automated Port in the Middle East, and this played an significant role in the equipment procurement process. For an automated port, the Terminal Operations System (TOS) is the crucial piece of IT infrastructure that ensures that machines operate efficiently, and that cargo is correctly tracked.
Jan Grinwis, terminal equipment manager at ADPC, says that the integration of the TOS with the automated stacking cranes (ASCs) was viewed as the riskiest interface in terms of equipment. Ultimately, Konecranes won the supply order for 30 ASCs, worth $117 million, since it was able to supply an integrated TOS system. More Konecranes supplied an additional six machines for $42m, with another order the same size to be delivered. As ports increasingly look at the benefits of automisation, software is essential.
“Looking at market developments, more and more full system implementers are developing. Konecranes, Cargotec and Terex. These are global suppliers who can supply a whole range of container handling equipment. Cargotec, who recently took over TOS supplier Navis from Zebra Technologies Corporation and Terex Corp, who took over Demag Cranes, became owner of Gottwald. For the customers this is intended to result in lower overall implementation costs,” said Grinwis.
Recently Konecranes introduced its Automated RTG (ARTG) system to the container handling industry, saying that it had solved the problems that have been preventing the adoption of automated RTG operation. Built around Konecranes’ 16-wheel RTG, the ARTG can handle handle the wide range of yard surface variations, and can handle the multi-dimensional complexity of truck traffic, which flows along the container stacks in an automated operating model. Software was also a factor when Kalmar, part of Cargotec, won an new order this year from DP World to supply two of its new generation reachstackers to the Jebel Ali T3, on top of an existing order for seven empty container handlers, placed in December. Kalmar’s new generation reachstackers, named Gloria, is designed to handle loaded containers and has the capacity to stack 45 tonne (9’6”) containers five-high in the first row.
Gloria’s onboard CAN bus technology is being interfaced with DP World’s local port automation system, the first time this has taken place. The interfacing will provides constant data transfer of the key operating parameters from the machine including fuel consumption, oil and water temperature, speed level, and operating and idling hours.
Other information it sends includes signals on the current working boom lift length and angle, together with the spreader height. For safety purposes, the twist lock/unlock condition and the spreader job type messages are also received.
Suresh Ananthanarayan at Kalmar says that these features, along with the ability to interface with the existing system, would contribute significantly towards safety and operational efficiency.
“As the focus on reducing costs of ownership continues, Kalmar leads the industry through its combination of advanced technology and innovative solutions. Gloria offers unsurpassed performance, and with the CAN bus operational information, our customer now has the critical performance data readily available to help them achieve optimum efficiencies.”
In addition to improvements in productivity, automisation can increase the number of jobs available that are attractive to a state’s citzens. DP World’s Jebel Ali Terminal 3 will be the largest semi-automated facility in the world when it becomes operational. Inaugurated by HH Sheikh Mohammed Bin Rashid Al Maktoum, Vice President and Prime Minister of the UAE and Ruler of Dubai in January, the new operating regime has allowed a signficant number of Emiratis to be employed.
The new cranes are operated by remote control, with operators situated in a quayside operations hub, viewing short circuit camera displays and receiving vital information through instrumentation. Consequently, 30% of the new quay crane operators that have been recruited are Emiratis, and of those, a third are women. The figure is even higher for RMG operators, with 70% of those recruited Emiratis and 70% of that group being Emirati women.
ADPC’s Khalifa Port remains a semi-automated environment, with operators positioned in-cab in the STS and the straddle carriers. In the future there is the prospect for full automation, with all operators removed to the command centre. Ports are highly controlled environments, and as far as equipment is concerned, emissions and evironmental impact are also a factor. The sector is one of the few areas in the equipment market in the Middle East where calculations of emissions are a signficant part of equipment procurement. And in addition to procurement, machinery departments can also consider retrofitting exisiting equipment to improve environmental outcomes.
DP World has successfully electrified eight diesel powered Rubber Tyred Gantry (RTG) cranes at Jebel Ali Port, a switch which it expects will reduce monthly diesel consumption by 109,000 litres in average, saving on energy costs and reducing emissions by almost 2,000 tons of carbon dioxide (CO2) per year. The electrification was supervised by global engineering group Cavotec, who is a proponent of on-going electrification of RTGs, as well as offering shore power solutions, which enable ships in port to switch off their engines and connect to shore-based electrical power supply, thus reducing emissions in ports and surrounding areas.