Safety rules over company culture
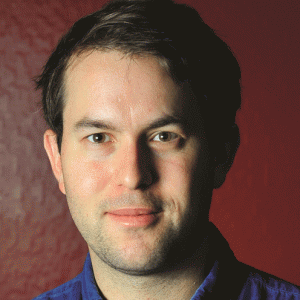
Construction companies and work sites in the GCC must be some of the most diverse work places in the world, with staff ranging from the Middle East, Europe, Asia, Near East and Australia. It is an environment in which knowing how to manage your communication processes can be just as important as knowing how to put up a building, for the project to progress as planned.
On the topic of safety, it’s not uncommon to hear construction managers or people in similar positions who have begun their career in Western countries grumble about the attitudes to safety amongst their workers.
Sometimes people will go so far as to voice the opinion that the Western mindset is innately safer than that of some of the other cultures present.
But it is worth keeping in mind that there is nothing ‘innate’ about a safe work place, these come about through well-designed safety plans, robust implementation of these, regular checks that the plans are being carried out and staff training, all of which come at a cost to the company.
In Europe and elsewhere, workplace safety practices and regulations are a result of a long chain of horrific accidents stretching back decades if not centuries. Injuries and deaths are investigated, and new processes developed, which over time have result in the cultures of safety.
Nevertheless, it only takes one lax company to forget the reasons behind safety practices to have disastrous results. An underground coal mine explosion killed 29 workers in New Zealand in 2010, and reporting on the inquiry into the causes of the explosion I saw the way a company can disregard well known lessons from the past, to the detriment of its workers. Underground coal mining is an entirely different beast from construction, but the signs leading to that disaster are instructive: a company that ignored or had little regard for its own safety procedures, which prioritised production over safety, and did not empower its workers to not speak out or act over safety issues.
In the Gulf, it is true that there are additional obstacles for companies when it comes to safety, including inexperienced workers with lower skill-sets, and different cultural backgrounds.
On the one hand, all companies perform a cost-benefit analysis on the problem of unskilled staff, and there are naturally limits on the amount of time and money that can be spent on training. But at the same time, I’ve visited companies in the GCC that were particularly proud of their efforts to engage with their workers, and train their workers to always be thinking about the job they were doing. This could involve telling workers to make their own decisions in certain situations, meanwhile assuring them they wouldn’t be punished for making a ‘wrong’ decision. It’s to be assumed that a medium-sized company would have the advantage in this kind of endeavour, but it is always heartening to see companies taking an enlightened and proactive approach to their staff.
As a construction industry journalist, I’ve seen photos of various work place accidents in the GCC – all of which involved loss of production time rather than human life – which can only have been the result of workers rushing to meet production targets, or were too afraid to halt work for safety reasons.
One of the principles underlying Toyota’s Kaizen practice (or ‘continuous improvement’) is that staff on all levels are able to make suggestions, and look out for ways of improving production and workflows (and we all know that a construction site has a lot in common with a manufacturing plant).
In the Middle East context, companies that seek higher responsibilities from their staff should be rewarded with fewer work place accidents, whether injuries or simply production mistakes. In these work conditions, staff are more alert to the site conditions, and also more likely to take action if they see a potential accident unfolding. While different national cultures are a feature of construction work sites in the Gulf, companies should look at the variable they can control, which is also the most important: their own internal company safety culture.