Volvo Penta aims for efficiency
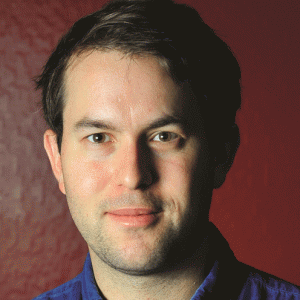
OEMs are on the look out for solutions that will increase their machines’ fuel efficiency
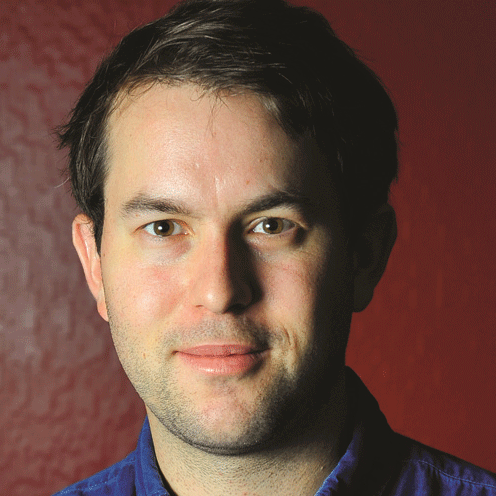
For Volvo Penta, building engines to be used by construction machinery OEMs in their equipment isn’t simply delivering a ‘one size fits all’ product, but involves a programme of improvement and adaption for its customers.
To help customers get the most out of their engines, Volvo Penta works with key OEMs across a range of segments and applications to determine how to maximise engine fuel economy in a variety of machines, including forklifts, reach stackers, log stackers, terminal tractors, cranes, crushers, shredders and mining equipment.
With oil prices at high levels historically, and with little sign that prices will abate, OEMs are on the look out for solutions that will increase their machines’ fuel efficiency. In many segments fuel will be the biggest expense incurred throughout the lifecycle of a machine.
“What we’re trying to do is very simple,” says Magnus Larsson, acting manager of Volvo Penta’s application engineering department. “We want to get the most power out of the fuel we use—regardless of machine application.”
Nevertheless, with so much variety in the application Volvo Penta engines are used for, providing low fuel consumption in all cases can be tricky,” Magnus says.
However common threads can be found within equipment segments.
“In mining, for example, fuel economy is not as important as uptime and ventilation rates. So we aim for the lowest emission engines possible for that segment. In material handling, however, fuel efficiency is highly important—but is often dependent on operator behaviour. So we work with those OEMs to come up with fuel-saving operating techniques,” he explains.
Volvo Penta takes these factors into account when performing field tests in the most common applications of its prioritized segments. But first it collects the analysis that OEMs have already done. “Then we do our own calibrations and run field tests with prototypes, logging fuel consumption continuously. We fine-tune as we go, taking into account the feedback we receive,” Magnus says.
For the most part, optimisation has to do with the relationship between engine and transmission. “It’s important to look at the complete package — not just our engines — when we’re running optimisation tests. The wrong transmission can cause a fuel-efficient engine to end up consuming quite a lot of fuel,” Magnus says.
“We try to provide as much information as possible to the OEMs so that they can install the transmissions that work most effectively with our engines.”
A recent example saw an air compressor manufacturer challenge Volvo Penta to reduce its customers’ total cost of ownership by repowering its machines. ‘
Volvo Penta fitted the compressor with a Volvo TAD1642VE engine — with the result that the manufacturer’s products saved an average of 10 litres of fuel per hour, experienced longer maintenance intervals, reduced noise, burnt less oil and experienced lower emissions levels. The result was a savings of up to $25,000 per year per unit.