Taking Flight: An interview with the region’s only drone provider for the construction industry
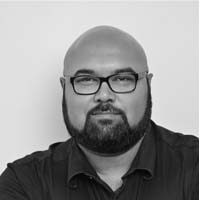
Drone technology can do so much more than just surveying sites as Gavin Davids finds out while speaking to Rabih Bou Rached, CEO of FEDS Drone-Powered Solution

As the use of drones becomes increasingly prevalent in the modern world, it comes as no surprise that forward-thinking construction companies and professionals are exploring ways to deploy the technology across project sites.
While drones are already being used to survey landscapes and monitor progress, experts predict that the usage of drones in construction will result in significant changes within the industry. Some of these changes are already happening, with drones providing more information and communication to stakeholders, resulting in projects that are better managed and delivered.
The data generated by drones will be key to this evolution, with construction professional able to access detailed insights to create reliable, detailed, and complex design models that provide a holistic view of the projects they are working on.
Before the development and deployment of aerial drones, the traditional method of gathering site data was carried out by sending out operators to physical walk across the site, or by using manned aerial vehicles, such as helicopters. For obvious reasons, both these methods were impractical.
Now, however, drones in construction are giving contractors the ability to receive up-to-date images, in real time, as often as they like. This not only allows them to monitor any issues, track progress and manage the site better, but it also allows them to improve many other aspects of the jobsite, such as labour deployment, material wastage, and creating an overall return on investment through the detailed analysis of the data.
Rabih Bou Rached, chief executive officer of FEDS Drone-Powered Solutions, has long been an evangelist for drone technology in construction. As the head of the Middle East’s only drone-powered solutions provider, he is well placed to gauge how ready the regional industry is for the technology, and he tells Big Project ME that he expects construction sites of the near future to be powered by drones.
“When we talk about the construction sphere, we’ve never had this bird’s eye view of a construction site. Drones bring a layer that previously didn’t exist, and the cost savings have been proven, with regards to how much they can help contractors.
“While drones can be involved in the complete lifecycle of a project – surveying before construction begins, during the construction to monitor progress – but there are applications that can be missed. Once a sensor is flying over a site, the data can be used for so many things – not just monitoring from the owner’s point of view, which is to see progress. From an EPC point of view, a project point of view, a safety point of view, it’s completely different what monitoring means, and for each department, we can bring them something different,” he explains, adding that drones can even help in inventory tracking by measuring and counting materials and equipment.
Rashid points that drones are essentially just robots with propellers, and that like all robots, they can be built and programmed to carry out certain automated tasks.
“Basically, the way we see it is that there will be drones all over the site – drones with robotic arms doing welding, instead of having scaffolding and people climbing up (into dangerous spots).
You can have drones that monitor, others that bring the equipment, do the heavy lifting, welding, inspecting and so on,” he says.
Of course, there are currently limitations on the technology due to some components being too heavy or complicated, while in terms of artificial intelligence, the technology is not yet advanced enough, but Rashid asserts that drone technology is getting to the point where their deployment on site is a commonplace sight.
In the present, however, he says that there are still plenty of ways that drones can be utilised on projects, pointing out that drones can be leveraged in four different ways to improve BIM output:
• Easy Data Collection: As the point cloud that drones generate is very dense, leading to highly detailed and precise 3D models. When a LiDAR sensor is used, this precision is further amplified, giving users incredible 3D models.
• Aerial Data: Record-keeping can be a time consuming and tedious job, especially when it is carried out via ground-level data and images. Drones alleviate the tedium by providing an ariel view and making the collection of data easier. Furthermore, the work can be minimised by analysing high-resolution imagery to determine the characteristics of objects. Finally, the measurements of objects can be pulled from the collected images instantaneously, thereby drastically reducing the amount of time record-keeping can take.
• Controllable and easily repeatable, with high accuracy: Consistency is critical to the construction process and by using drones, contractors can capture the site in the exact same manner, every time. This ensures data integrity over periods of time.
• Integrate Drone Data into existing cloud infrastructure: Drone data can be easily integrated into any cloud infrastructure and will enable project stakeholders to seamlessly collaborate and create a system where data flows smoothly into the BIM software.
“A drone gives you an extra layer, one that (ground-based) BIM does not have. The sensors could be carried on the drone, or the drone data itself could be integrated into the model. BIM is usually part of a huge construction software, and a point cloud point of view or digitalisation point of view, is just one layer that the drone can provide. From a holistic construction site point of view, a drone can add more information that can be used in parallel with BIM data,” Rabih continues.
“Right now, construction companies ask us ‘how can we fly drones and save money’? The link there is overlaying the blueprints to the as built and catching mistakes early,” he says, citing examples where clients had made mistakes during the build and encroached too far or built to too short, resulting in them having to demolish and build again at an increased cost.
He points out that drones and the data collected from them can actually help avoid these types of costly mistakes, while the database library that is built along the way can help contractors build more efficiently, effectively, and with less mistakes or changes.
“You’re digitising the whole process – there are historical records for every villa, every shopping mall, every building that a contractor builds. You can enter this data into an Artificial Intelligence model, and it can improve the efficiency of how you do things in the future. With more data, you can then figure out (how to save money in different ways).
“This can’t be guessed – only the data will know these things. Not every site is going to have problems where data can catch mistakes early, but every site can use data to improve their processes in the future. The more buildings they have, the more the data can be revisited. No one has had this data before – they have had plans and blueprints and so on, but no one has had this holistic view of everything that’s going on. I can easily imagine feeding this data into an AI that can tell you immediately where you can or could have saved, say 30% cost or time, on a particular product or component.”
When it comes to Artificial Intelligence, Rashid is adamant that the drones industry needs to improve its capabilities as drones today can only sense and avoid obstacles, despite the technology existing to allow them to do far more.
“They can see something and know that they shouldn’t touch it and will move, but the technology exists so that if we digitise something, the drone will follow the point cloud manipulation or flight control. What we want is a drone that’s smart enough to recognise and react like a human would. You can train a drone to react to a screwdriver or a pole, but what happens if there’s something that it doesn’t’ recognise? We haven’t reached the point where a drone can do all of this automatically.
“In five years? Perhaps, but I can certainly imagine a future where instead of a roll of blueprints that you put in front of a client, you’ll have all of this data combined where you can walk through a building and see everything. Your blueprints will not only be in 3D, but they’ll be in virtual reality and people can actually visit and interact with them. When you combine all of these technologies, you can do amazing things.”