Keeping it wheel
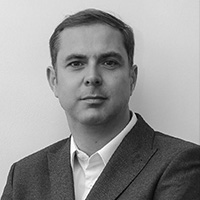
Wheel loaders are the workhorses of construction sites but how can best look after your prized heavy weight? Ideally an operator of a wheel loader will not wait for scheduled check-ups and do preventative maintenance on their machines every day of operation. However in a world where time is one of your biggest costs, is […]
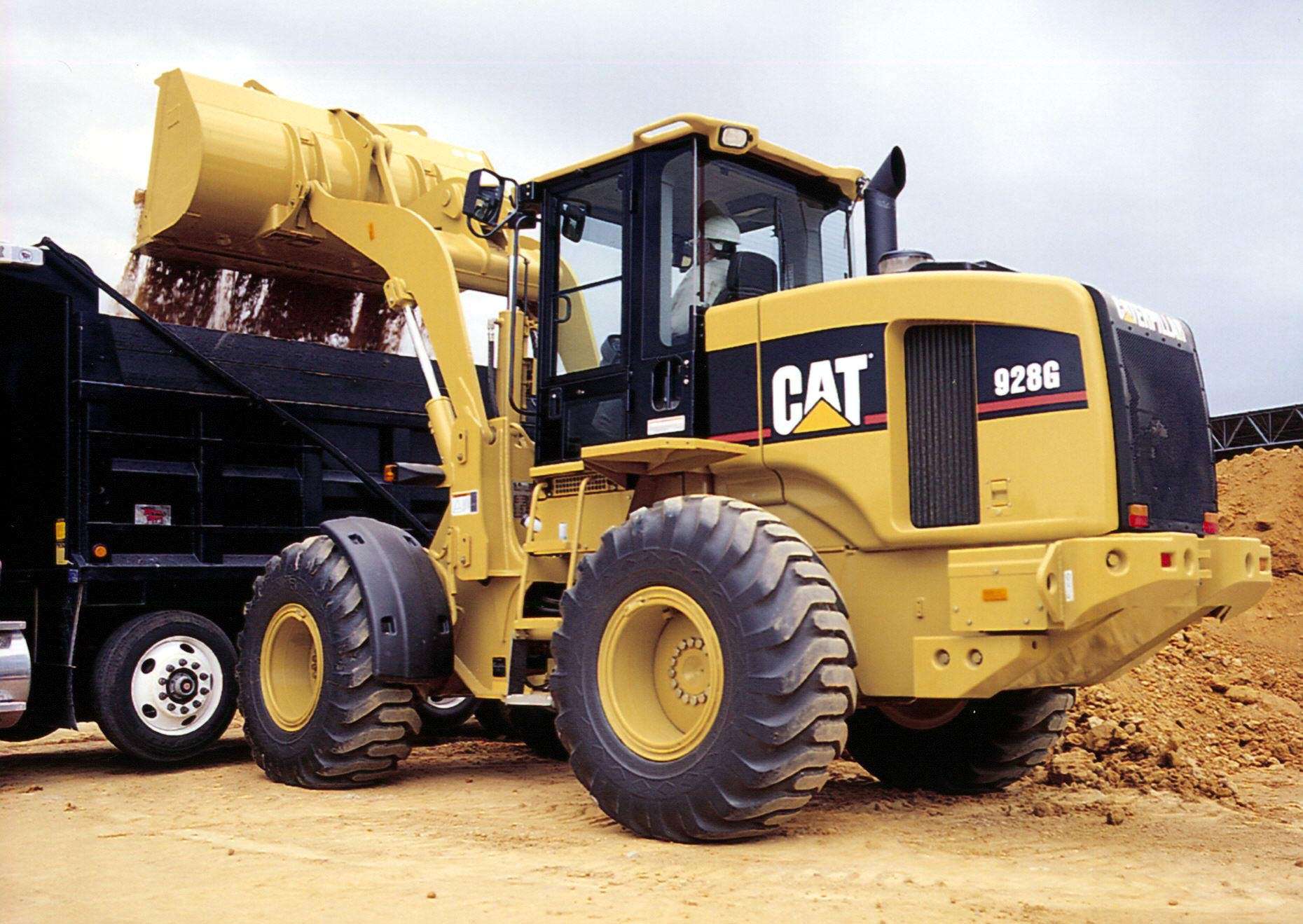
Wheel loaders are the workhorses of construction sites but how can best look after your prized heavy weight?
Ideally an operator of a wheel loader will not wait for scheduled check-ups and do preventative maintenance on their machines every day of operation. However in a world where time is one of your biggest costs, is it possible to keep that dust and dirt under control while finding the extra time to keep tires, fluid levels and grease in tip top condition?
Well, unfortunately, the region’s poor maintenance and break down record suggests that not enough people are spending those extra few minutes that would save money and time later on down the line. The net result, inevitably, is that not enough is being done.
The good news is that OEMs and distributors are able to send on information on recommended maintenance practices particularly as it is paramount to the well being of the product. Extensive testing is performed on various components to determine maintenance intervals and filter requirements, and that data is also readily available.
Thankfully for wheel loaders it is straightforward to set up a simple daily maintenance routine and be implemented. Ideally, the routine should be performed by the operator at the start of the day. The first place to start is a check of the fluid levels of the hydraulic oil, engine oil and fuel. It should then end with a walk-around of the machine.
Obviously not all machines are designed the same way but they will certain tasks can be completed and implemented in the same way. So consult the operator’s manual for a machine’s own specifications, even if the differences may on sight seem negligible.
The owner’s manual should be the plant manager’s or operator’s best friend. Encourage anyone with responsibility to look at it, as it is such a useful source of information. If you don’t consult the manual, you can miss out on changes that have been made to the maintenance schedule since the last time you purchased a new machine.
Much like car manufacturers post tyre pressure information on doors, major OEMs tend to place stickers onto the cabin, chassis or parts to highlight the service interval information.
Machines are constantly being updated so it is worthwhile ensuring that even with a new machine that looks like a minor upgrade, that operators revise or advised about changes. Take engines for example, moving from Tier II to Tier III units on wheel loaders saw changes to fluid requirements, and typically saw manufacturers increasing fluid change intervals. Missing out on these changes could also mean missing out on savings, especially as the fluids don’t have to be as changed as frequently.
Of course there are other scenarios that could mean that operators are missing vital information critical to the machine’s safe operation. Intervals are designed to provide the most productive and efficient longevity of the machine – and they could prevent major breakdowns.
This is especially pertinent in the Middle East where dust and sand environments can infiltrate filters and stop air and oil flowing unimpeded in the machine. Ideally you want your filters to be clear of any clogs and dirt to ensure the best performance from the engine. As clean filter reduces fuel consumption, manufacturers are introducing reversible fans that will clean debris from coolers and stop overheating, even in the most extreme of conditions.
Engines may be fitted with bypass valves that ensure fluids reach those hard to reach spots despite clogged filters but if you’re not following a proper maintenance schedule you’ll be spreading gritty fluid over critical parts. Ultimately this will lead to component and possibly engine failure through wear and tear.
Going beyond the recommended interval schedules will prevent your big expensive four-wheeler being able to do its job properly. It is easy to get complacent about oil levels particularly when the first time you become aware of a problem will be a warning light. By the time it has got that far then you have lost any of those critical savings you were after. Fluids have special additives that can break down and lose protective qualities in certain conditions. Always stay inside the manufacturer’s suggestions of hours for oil changes.
Most OEMs will recommend lubricants that can be sourced from the local dealers. While you may have a preferred dealer that may not supply the brand on the list, check that your not endangering your warranty on the machine. If something goes wrong through component damage that is attributable to the oil you have been using then you run the risk of having to take on the costs of major repairs even on low hour machines.
Operating wheel loaders in extremely harsh environments, or in multiple shifts, means you will need to adjust the maintenance schedule. Take advice from your dealer, or if you’re buying a used machine directly from another operator, on how these adjustments should be made.
Wheel loaders are frequently deployed on heavy construction jobs, demolition and waste treatment and all of which are liable to shorten a loader’s life in operation if proper maintenance is not performed. Always ensure the machine matches the operation and weight of material being handled.
Also take into account conditions and the types of loads to ensure that the machine is operated according to the task in hand. Furthermore operators should avoid the temptation to minimise the amount of changes in attachments and should always have the right tools for the job. When possible different buckets should be used for debris, sand and stone. Likewise tyre pressure should be adjusted to suit the environment and checked constantly to ensure efficient and safe operation.
For instance if one tyre’s pressure is lower than another, a bucket or ground-engaging tool won’t be level. If you are low on one side you are also putting more torque on one side, straining the machines moving parts and brakes.
Taking care of your wheel loader will add longevity and should it be a consideration, value when it comes time to trade it in or sell it. Proper maintenance can add 15% to 20% to the value of the machine at trade-in.
Ultimately the best way for operation to be successful is to let operators feel respect for their machinery. Make sure they take care of handling the machine. The rule of thumb for wheel loaders is to come to a complete stop before shifting gears. Always remember, operators are the biggest threat to the machine and they can damage wheels, axles and transmissions.