Project profile: Arab Academy of Science, Technology and Maritime Transport (AASTMT)
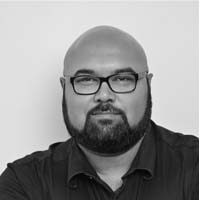
How HPBS helped build the Arab Academy of Science, Technology and Marine Transport campus in Khorfakkan, Sharjah within 120 days
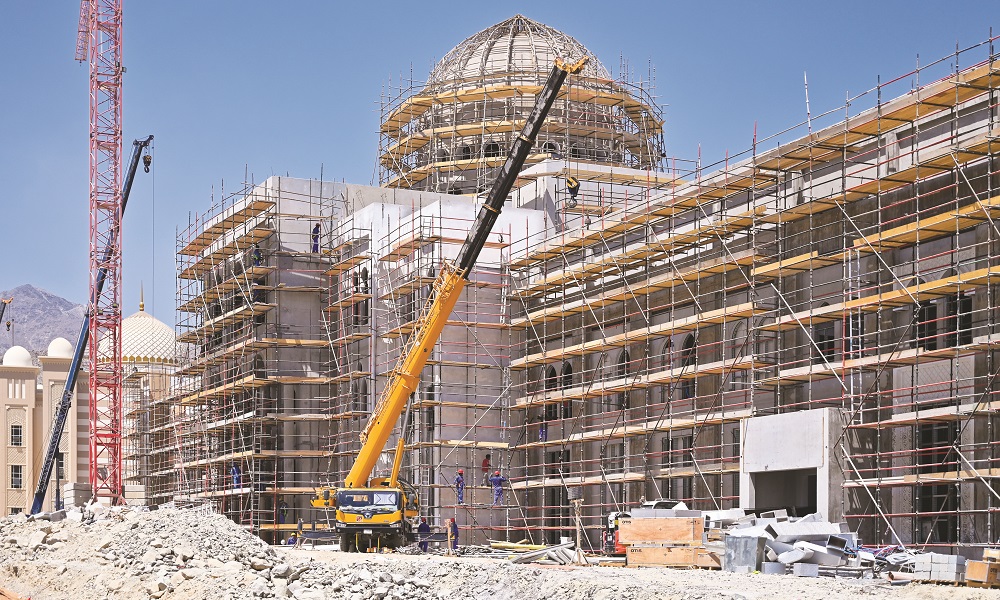
July 2018 saw the issuing of an Emiri decree by HH Sheikh Dr Sultan bin Muhammad Al Qasimi, Supreme Council Member and Ruler of Sharjah, which established the Arab Academy of Science, Technology and Maritime Transport (AASTMT) in the Emirate of Sharjah.
The decree stipulated the establishment of an academic institution in the east coast city of Khorfakkan, part of Sharjah. According to an MoU signed between the Sharjah Government and AASTMT, the new branch will qualify graduates specialised in various maritime transport sciences and technologies, in addition to international transport, logistics and maritime law. State-of-the art specialised education programmes will also be provided, a statement from AASTMT adds.
A regional university operated by the Arab League, the AASTMT runs programmes in marine transportation, business and engineering. As per a news report by WAM, the new branch will grant students bachelor degrees in applied and theoretical sciences.
Once the decree was issued, work on the development of the campus in Khorfakkan began rapidly, with the MoU stating that the government of Sharjah will provide an appropriate plot of land and the necessary educational and administrative buildings, equipping them to the latest international standards. For its part, AASTMT will deliver the curricula, teaching materials and educational tools, as well as qualified academic, administrative and technical staff.
Also, part of the MoU was an agreed start date of September 2019, which meant the entire campus needed to be built from scratch and ready for operations within 120 days. This short timeframe didn’t leave the main contractor, UNEC, with many options when it came to getting the project built in time. Therefore, the UAE contractor turned to its long-time partner and supporter on several other projects to help get the job done – HPBS, a subsidiary of ASGC and one of the leading precast companies in the UAE.
“To be honest, for us it was a sudden move. When we talked about the project at first, we considered it impossible to be done. To finish this volume of cubic metres of concrete within three months – we’re talking about 22,000 cubic metres – at the first meeting, we said ‘This cannot happen, it’s impossible’,” relates Bashar Abou-Mayaleh, managing director of HPBS. “However, we have a very good relationship with the main contractor, UNEC, a business partnership if I may say. We have completed three projects with them, and we currently have another three running. That’s how good our relationship with them is.
“Without even tendering the project or asking for quotations, they came to us directly and said, We know that you are the only precast company that can do this job. We know we can’t do it cast in-situ, which is the conventional method of concreting and doing buildings and structures.
“[Because of this relationship], we kept digging into it. It was very challenging. Half the people present at the table for that initial meeting were fascinated by the model itself – they were saying that this could not be done in precast. But we kept talking about it, discussing it, and after a few days of studying the preliminary drawings – this was a design and build project by us as well – we redesigned the buildings themselves,” he reveals.
While the architecture and concepts were kept the same, the structural elements were changed. Abou-Mayaleh explains that larger, thicker elements of the design were taken out, with lightweight and sustainable parts replacing them.
“The preliminary drawings for the project contained some parts that could not be installed. They could not be lifted by our cranes, and it would not be feasible to bring in a 200- or 500-tonne crane for the project. Instead, we thought about how we could optimise the project, and that’s how the value engineering started. All the teams shared their comments, we discussed it in a big workshop, including the production, design and transport limitations, then we started the project.”
As Abou-Mayaleh explains, HPBS approached the project as a design and build contract, given the amount of rework required in order to ensure the company’s factory and production lines could create the precast segments as per the client’s requirements. The initial drawings revealed several complexities in the design, with cladding over panels, several arches and intricate designs, he says.
“There are a lot of complexities, which resulted in the draft of one drawing for this project taking about 20 times longer than what a draftsman would normally take for an average drawing. The details are unbelievable,” he says, highlighting the arches as one example, explaining that on this project, they’re so complex, they have different radiuses.
“For this to be implemented through design and into production was something new for us. These types of arches, you cannot do them in steel moulds, so we had to use a mix between materials for some of the moulds.
“We needed to have everything in place for this design. For the structural stability to be there, it’s not easy to do when you have to make everything lighter and with all these different shapes. Everything has to be 100% in place, and you have to think about details like the connections, which have to be hidden. For other projects, you might not care as much, because you can carry out repairs and modifications, but for this one, everything had to be perfect. Everything required much more steel and much more reinforcement. I think it was about 40% to 60% more than a normal reinforcement would require.
“This resulted in huge problems for us in production. More reinforcement meant more headaches, not only in terms of productivity but also of pouring the concrete and the vibrations that result in lower quality, which is something that’s forbidden for this project. Our design team faced a lot of these issues and really did a good job on this project,” he asserts.
In many ways, the success of HPBS on this project was down to the extensive use of construction technology on the project, Abou-Mayaleh says. Due to the high quality and speed demanded for the project, the company had to use all its technological resources. Not only did this include the use of physical assets, such as an automated Avermann system and a fabrication truck, but it also included the extensive use of BIM throughout the design process.
As Bahaa Ibrahim, GM – Technical, explains, the two main challenges the team faced were around design and time. In addition to the buildings being extremely ornate and complex, there were also a large number of them – 12 in total – with each one distinctly designed.
“This project actually belongs to the Sharjah government and most of the buildings are related to the Arabic/Islamic style with many arches and huge openings and domes. The floor height is huge, up to seven metres, so everything really was very difficult.
“And we had several buildings, and we’re talking about difficulty in design for each one of them, as each building is unique. There were design difficulties, untypical elements, and a huge number of elements. Everything was big – the concrete dimensions were huge for each one of them, and at the same time there was a time limitation. We started work in April and had to finish everything before September. Not only that, but we had other commitments and other clients and projects to consider.
“It was also Ramadan and 50% of the working hours were not there – it was half-day mostly, and most of the people on-site were fasting. We had to deal with all these difficulties, but we had the full BIM process in the design department,” says Ibrahim.
“We are using REVIT; we have 3D models for each and every building. We could not resolve the design issues we talked about if we didn’t have this facility in the design department. When you have arches, door and window openings and other decorative elements coming in just in one piece, how can one person work on a 2D platform to imagine and realise this?
“The BIM process in the design department helped us a lot to imagine and reduce or eliminate the mistakes. When you have a fast-track job with difficult design, you can end up with several mistakes, which can be a disaster for the work on-site. By using Revit and applying our full BIM procedures, you can say that we eliminated mistakes and that there was a 99% accuracy rate.”
Another major challenge for the HPBS team was that they were the only party involved with the project that used a BIM platform. With the other stakeholders working in a more traditional way, the team had to transfer everything from 3D to 2D in order to communicate with the other project teams, which was a time-consuming process that hindered the pace of progress.
“For every job, you should have coordination between all aspects – architectural, structural, electro-mechanical, steel structure, etc. If you have all these stakeholders, they have to coordinate and sit together before any work is done. That was another issue because we had a shortage of time and we had to proceed.
“At the same time, the client sometimes made changes; while we’re going so fast on-site, we don’t even have time to review the drawings. You have to make sure everything is very accurate and correct from the beginning. [On a project like this], you don’t have time to change or to listen to someone who wants to change something, but how do you say no to the client? Irrespective of where the issue comes from, the client’s side or our side, it needs to be rectified. That means you have to stop everything, re-do it and then continue,” he says.
However, despite this drawback, Bashar Abou-Mayaleh praises the level of coordination and collaboration the various project stakeholders showed, with every member of the project displaying flexibility and adaptability in the face of tremendous odds.
“To be honest, UNEC trusted us a lot. They trusted our design team to even handle the coordination with the MEP. We pushed everyone involved with the project because we felt like this was our own project. Our design team pushed the MEP subcontractor, for example. They brought them to our headquarters, taught them how the REVIT system and BIM models work, so that we could all be in sync. This also saved time that we didn’t have. The project was really a learning experience for all of us.
“It’s a fast-track project, and I can tell you that UNEC was fully supportive. Whatever we asked, they would try and accommodate and facilitate our requests. Many items were finalised after the project started – whether it was our scope or their scope, they were supportive and collaborative,” he asserts to Big Project ME.
This cooperation extended to UNEC providing space for HPBS to establish a stockyard on-site, for the precast manufacturer to create a laydown area that stored the cast elements to be installed, as well as the necessary equipment needed for the project, such as their cranes. In addition, a deployment plan was drawn up and executed for all the materials, machine and manpower used on the project, with the HPBS logistical team playing a crucial role in making sure the requirements of the project didn’t exceed the fleet’s limitations, Abou-Mayaleh adds.
“We had some special trailers for those elements that reached 23m, while there were a lot of hollow-core elements spanning 18m and 550mm thickness. We are the first company to create this, and we even made some modifications to the machines themselves [to create them]. We have become pioneers in the industry in terms of creating this 550mm thickness,” he states.
“We also had a fabrication truck equipped with many new equipment, which was especially for this project due to it having many elements with curves – round columns, arches and so on. We even bought a rolling machine for this project, and the return on investment for this machine was reached and covered within 45 days, due to the complexity of the elements.”
With the AATSMT campus now due to be handed over and the university scheduled to commence classes imminently, Abou-Mayaleh can look back on a job well done by his team at HPBS. He proudly states that he believes this project is one of the most important ever done in the company’s history, given the scale, complexities and timeframes that had to be contended with.
“We are very happy we have succeeded in this project, and I’m proud of our fabrication teams. When you look at the moulds themselves, they’re pieces of art, honestly. It’s the best marketing campaign that we have done – and not just for us, we have really elevated the precast industry with this project.
“The timelines and the complexities that have been tackled demonstrate HPBS’ capabilities to take on really complex projects and turn them around within the required timeframes and budgets, and to provide any support that we can give to developers in terms of design and build, with the technology that we have,” he concludes.
Key project highlights:
- A total of 6,279 elements used
- Total area – 71,350sqm
- Total duration of project – 120 working days
- Some relatively complex elements produced in our factory for the project – dome walls, round column, minaret, curved wall, U-shape wall from mould face, and double recess wall
- An average of 6.23 tons of elements produced
- HPBS produced an average daily of 127m3 to meet project requirements
- HPBS produced an average daily of 50 elements to meet project requirements
- Total number of buildings – 12
- Date of handover – September 2019
- Date of inauguration – October 2019