Site Visit: ICD Brookfield Place
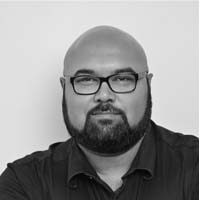
Gavin Davids joins project manager AECOM at one of the most eye-catching towers in the DIFC area
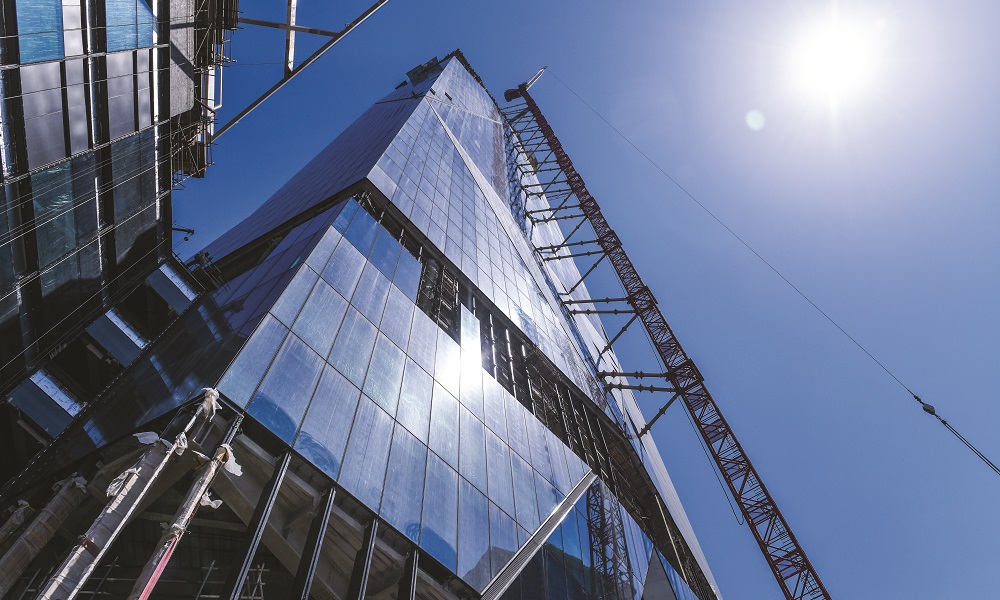
Early in 2016, at the press event announcing the launch of ICD Brookfield Place, one of the key messages hammered home about the project, which was being developed by ICD Brookfield, was that it would be a truly inspirational piece of architecture and design.
Fast-forward to April 2019 and these words to ring true, with the 53-storey tower rapidly approaching its full form on Al Sa’ada Street in the DIFC area. Designed by architect Foster + Partners, the glass office tower takes on the form of a sharp prismatic structure, with the façade appearance transforming in synchronisation with the position of the sun over the course of the day.
With the building core now topped out, Big Project ME visits the site with AECOM, the project manager, to learn about the progress being made and the processes put into place to ensure the smooth delivery of the project.
“Tenant fit-out commencement is going to be in Q2 2019, while phased completion is going to be Q4 2019,” says Alan Anderson, project director for AECOM on ICD Brookfield Place, speaking at AECOM’s site offices opposite the construction site. “The tower core has been topped out. In a few months, we’ll be finishing the steel frame at the top of the tower. That will allow us to remove TC1 crane and complete the external façade.”
As the name implies, the project client is a joint venture between the Investment Corporation of Dubai and Brookfield Properties. Furthermore, the contractor is also a joint venture, this time between Multiplex and SsangYong. In addition, the lead consultant and architect of record is BSBG, Robert Bird Group is the structural engineer, and AESG is the LEED consultant. AECOM’s MEP subdivision is the MEP designer on the project as well.
Given the number of companies involved and the complexity of the project, AECOM has been tasked with overseeing a collaborative management approach with all key stakeholders to ensure effective communication, timely turnaround of information and decisions, resolution of key issues and risks, and coordination between consultants, client and contractors.
“AECOM’s role is project management and cost management,” says Anderson. “We have two construction managers to push the works on-site and to also check on manufacturing – they go on factory visits to check on the production of various components and to make sure they’re being manufactured on time, in line with programme requirements. We have a total of 14 people here – that consists of nine on the project management side and five on the cost management side.”
As part of its role as PM, the AECOM team is tasked with senior management meetings between the client, contractor and consultants, holding Smartboard design workshops, Webex and conference calls with the team, which is split between two geographies, he explains.
“We have fortnightly progress meetings with the full project team and weekly planning meetings with the contractor and the client, whereby we scrutinise procurement, manufacturing, productivity, look-ahead programmes and monitor the progress of key milestones for the forthcoming months. Regular LEED/commissioning and MEP procurement meetings are also held, as well as ad hoc meetings as and when required, to ensure we are communicating as a team.
“In addition, Foster + Partners’ key decision-makers are based in London, as is the design director from Brookfield, so we have weekly Smartboard meetings which allows us to share the screen and comment on drawings or designs either from Dubai or London.
“We’re on target for achieving a LEED Gold rating. We also have a number of other consultants directly contracted to the client. In some projects, you have a lead consultant with subconsultants directly contracted under them. On this project, however, all of the consultants are directly contracted to the client, which makes coordination a lot more challenging. As such, we have to collaborate more,” Anderson asserts.
As part of this collaborative process, he confirms that BIM is being used on the project, with the contractor producing a fully coordinated model. Once the project is completed, the model will be handed over to the client for operation and maintenance purposes.
When it comes to operations on-site, the challenges become much more pronounced, Anderson explains, pointing out that the main service road for the project site is very narrow and right behind the hoarding separating the site from the main road.
“That has been the main access and egress point for deliveries of materials and it’s very constrained. It has been a huge challenge and the contractor has had to manage it very closely, to make sure that they’re timing deliveries and carefully plan the logistics.
“At the initial outset of the project, there wasn’t enough space for laydown of materials. That was an initial challenge for them to deal with, but as the building came up out of the ground, they’ve started to use the basements to store materials.
“The site is also very congested. You’ve got Al Fattan Currency House on one side, Gate Avenue and the Ritz-Carlton at the back, so it’s something that needs to be managed very closely, in collaboration with DIFC. They’ve got construction guidelines that we’ve got to work within as well, for safety and logistics as an example. Another key challenge has been managing and monitoring the construction noise levels around the neighbouring buildings. We make sure that we work to Dubai Municipality regulations as far as noise is concerned,” he adds.
One of the biggest challenges the project team encountered on the project was right at the beginning, with logistics, removal of soil and safety associated with the deep basement excavation.
“This project has one of the deepest basements in Dubai, so that threw up a lot of challenges. There was also a previous abandoned development here, whereby we had the previous existing piles and an existing D-wall. Some of those piles were reused on the new pile raft foundation,” Anderson explains, adding that this was achieved through engineering and testing to incorporate the existing piles into the new piled raft design and construction.
Another construction challenge is the steel structure, not very common in high-rise buildings in the region. The superstructure of ICD Brookfield Place has a central concrete core and a structural steel frame, he outlines, adding that the stability of the system includes a plant zone outrigger acting collaboratively with the external steel A frame and core.
The relative stiffness of this system was tuned such that the single steel node of the A frame was within 70 tonnes, Anderson explains. This load was chosen to match the capacity of the world’s largest luffing crane and to avoid the time-consuming complication of stand-jacking a heavier node.
“If you look at the top of the tower, the steel structure is very complex. You’ve also got an outer façade and an inner façade. This has presented very big challenges in the sequence of works. We’ve also got a plant space on Level 54, so that means that there are multiple tradesmen working in quite a confined space, obviously at a very high level of the building.
“This has presented quite a lot of challenges in terms of logistics, safety and also for the manufacturing of the façade. To overcome this, the contractor manufactured large modular frames around 14m x 6m in size, which were lifted by the crane and bolted into place. This reduces the lifting time and helps with the progress of works.”
There are an estimated 8,000 panels used in the façade, with the largest glass panel being circa 3m x 8m, while the structural steel weighs in at around 24,000 tonnes, he adds.
“There are two main facade systems – there’s the unitised system, whereby a complete unit is pre-manufactured and brought to site and then dropped in by crane and fixed to the structure. The other type is the stick system, whereby the frame, mullions and transoms are installed on-site, and then the glass is brought in and fixed to the frame.”
Finally, as Anderson brings the tour of the site to a close, he focuses on the HSE aspects of the project. Although AECOM has more of an auditing and supporting role, as per its policy and safety values it has a dedicated safety officer on the project one day a week, so that he/she can attend safety walks, manage the closure of Lifeguard observations, attend weekly safety meetings, review or audit safety documentation, investigate incidents and support the PM/project team to drive safety as the number one priority.
“We have worked closely with the lead consultant (BSBG) and the main contractor for the management of all aspects of HSE. Recently, the project team celebrated a key safety milestone in achieving 15 million worked hours without a loss time incident, which is a great achievement by the team given the complexity and logistical constraints of the project and having an average of 3,000 labourers on-site,” he says.
The AECOM Lifeguard system is implemented on-site by the consultant/contractor. Observations are uploaded via a mobile app or online and issued to the contractor, who responds with action taken to close out the observation. The AECOM safety officer reviews and closes on acceptance of the appropriate close-out action.
“Monthly Senior Safety Management meetings are held with key senior personnel from the client, BSBG, AECOM and the contractor, so as to focus on upcoming safety concerns and initiatives,” Anderson concludes.