Cat introduces new multi-processor tools for excavators
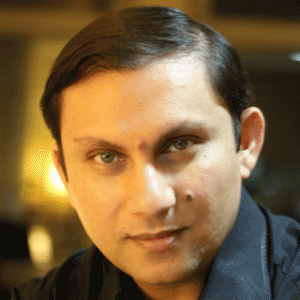
Interchangeable jaw sets and exclusive features enhance productivity, manufacturers says

Caterpillar Work Tools has expanded its range of excavator attachments with three new multi-processor models which build on the company’s demolition-technology experience with new features aimed specifically at users requiring large, flexible, purpose-built tools that can handle virtually any demolition task.
According to an announcement by the company, the MP332, MP345 and, MP365 join the MP318 and MP324 in the Cat multi-processor range. The new models are designed to be multi-processors that allow pairing a basic housing with any of up to six jaw sets, increasing jobsite versatility.
According to Cat, the design also boosts productivity with patent-pending features, such as a new jaw locking system and the Speed Booster valve. The net result is optimum performance, coupled with low owning and operating costs.
The new MP300 Series models are compact and designed with a high power to weight ratio, delivering strong cutting and crushing power, while reducing stress on the carrier. Also, the housings used for the new tools incorporate a heavy-duty rotator that provides 360-degree movement for positioning the multi-processor at an optimum angle for any demolition situation.
Explaining the operation, Cat said that when the jaws meet resistance, the integral hydraulic booster valve automatically activates. The Speed-Booster system combines a ‘speed’ and ‘booster’ valve and can therefore use a smaller cylinder diameter compared with previous models. Cat claims this nearly halves cycle time for jaw opening and closing. In addition, depending on the jaw set used, closing force is up to 19% higher, compared with previous-series models.
The configurations of the interchangeable jaw sets include Concrete Cutter (CC), Demolition (D), Pulveriser (P), Shear (S), Universal (U) and Tank Shear (TS). The jaw sets are designed to be exchanged in as few as 10 minutes using only basic tools. Larger models feature a pin capture system that retains the cylinder pin with the jaw to further enable fast, safe jaw exchanges.
According to Cat, the jaw sets have fewer welds for fewer stress points and more replaceable wear parts compared with previous designs. Also, many wear parts are pinned and can be replaced in the field, saving time and expense of moving the jaw to the shop for repair.
Cat has also designed the new models in such a way as to protect the hydraulic components and hoses. This included housing the motor in the frame. The number of greasing points has been reduced, compared with previous models, simplifying routine maintenance.