Riyadh Metro carriages on track at Alstom plant in Poland
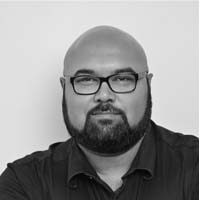
Big Project ME visits the Katowice plant in Krakow, where the rail transportation giant is building the carriages that will run along Lines 4, 5 and 6 of the Riyadh Metro
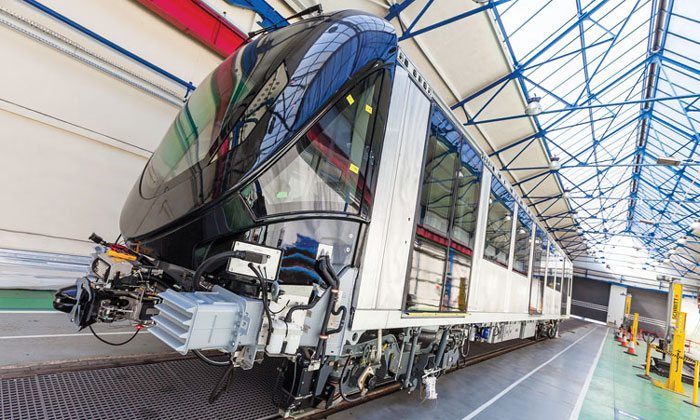
In November 2015, French multinational rail transport solutions provider Alstom announced that it had begun production on the trains from the Riyadh Metro project, with work commencing at its Katowice plant in Poland.
The rail giant was tasked with manufacturing all 69 of the Riyadh Metro trainsets as part of a $6.2 billion contract awarded to the FAST Consortium by Saudi Arabia’s Arriyadh Development Authority (ADA) for the design and construction of Lines 4, 5 and 6 of the network. Together, the three lines have a total length of 64.5km, which will include 30km of viaduct. 29 stations and two depots will also form part of the $22.5 billion network.
Alstom’s share of the contract is $1.3 billion. With the company scheduled to deliver the first three trainsets to the ADA in 2017, work at the Katowice plant is in full swing, as Big Project ME discovered during a recent trip to Poland to check on the progress.
Employing more than 1,000 people, the plant is one of Alstom’s largest train manufacturing sites in the world. Every step of trainset production is carried out at the plant, including the final static and dynamic tests.
IN PICTURES: Riyadh Metro carriages roll off production line at Alstom plant
Production on trains for all three lines is currently underway, with five sets completed at the time of Big Project’s visit. The first trainset was completed in January, leaving the Katowice plant for Saudi Arabia via the port of Hamburg. Two of the trainsets are undergoing dynamic testing in France, while a fourth has been sent to the Rail Tec Arsenal climatic test chamber in Vienna, Austria. A second trainset was scheduled to be delivered to Riyadh in February. At present, there are eight Metro trainsets in the production phase, with the complete order – along with infrastructure – scheduled to handed over by the end of 2018.
When production is at full pace, the facility will be turning out five trainsets a month off the assembly line, Alstom says. The sets are Metropolis automated aluminium two-car systems, each one 36m long and capable of accommodating up to 231 passengers. The trains are all 100% motorised, allowing them to run on tracks with a slope gradient of up to 6%, while on the flat, they are designed to run at a top speed of 90km/h on a standard-gauge track.
Alstom is one of three Metro suppliers working on the Riyadh Metro project, and one of the key factors is that the trainsets being supplied have to be specifically designed for the conditions they’ll be operating in. Each trainset will feature a powerful air-conditioning system, adaptable to the extreme heat found at the peak of summer in Riyadh.
Furthermore, as the first ever public transport system in the Saudi Arabian capital, the manufacturer is installing specific features to enhance the passenger experience, says Samir Karroum, Middle East and Africa vice president of systems and infrastructure at Alstom.
Platform screen doors are being installed to ensure safety and fluidity, he explains, adding that the Metro trainsets will feature an advanced passenger information system that delivers real-time information through screens and loudspeakers. This will allow passengers to orient themselves more easily, while allowing smooth people flow.
The interiors of the trains have also been designed for comfort and usability, with each carriage containing high-comfort seating and layouts specified by ADA. These will incorporate design elements that echo Riyadh’s architecture and history, with handrails shaped in the style of palm trees and seating covers that replicate patterns found in traditional houses.
Each train will have three classes – first, family and single class. These will be separated by glass partitions, while the exteriors will be colour-coded according to the lines they are running on. Line 4 will be yellow, Line 5 green and Line 6 purple.
Alstom will be supplying its Urbalis signalling systems for the automatic train control and power supply, along with its Hesop braking energy recovery system, designed to “deliver the best energy efficiency and reduced infrastructure cost”.
“Hesop’s novelty lies in its specific single convertor with dynamic regulation, which optimises the power required for traction and captures more than 99% of recoverable energy during braking mode,” Alstom says.
IN PICTURES: Riyadh Metro carriages roll off production line at Alstom plant
Pierre Delpierre, Metro product director for Alstom, says that because the trainsets are driverless, the system can be accelerated in an easier manner than it would with additional drivers being called, a process that takes hours, especially in cases of bad weather. Additionally, the system is eco-friendly, as it shortens the distance and time between trains due to being able to programme them for maximum efficiency.
Alstom will also deploy Appotrack, a mechanised solution that allows installation of tracks three or four times faster than using normal methods. This not only reduces logistical challenges, but also cuts down on CO2 emissions, noise, dust and waste, while also limiting the disturbance to traffic.
While Alstom and the consortium have been tasked with delivering the Riyadh Metro, the Arriyadh Development Authority has also been heavily involved with the project. Khalid Alhazani, director, Architectural Project Programme and Public Affairs, the man tasked with leading the project for ADA, says one of the key elements of the project is educating and informing Riyadh’s residents about the benefits of using the Metro.
“This is the first Metro project in the Kingdom. People in Riyadh don’t have experience in using public transportation,” he says, speaking during a presentation to media. “But at some point, they will have to use it. With the bus and Metro, they won’t need a car! It will take time for people to get used to using public transportation, but we’ve planned everything in detail to make it easier for them to use.”
The Riyadh Metro project is set to be one of the world’s largest urban transport projects, aiming to lift more than three million commuters off roads, to reduce the city’s massive traffic congestion problem.
“We are on schedule. We have reached 48% completion, and we believe that the Metro will start operating by early 2019, with no delays,” Alhazani says, adding that the six lines will cover 176km across the city, with 85 stations. Walkways are being designed along the lines, with landscaping and public rest areas built into the routes. 25 car parks will also be built, so that residents can use their cars to reach their nearest station before switching to the public transport network.
The Metro, along with a 24-line bus network, is part of the King Abdulaziz Project for Riyadh Public Transport. It aims to meet the demands of the city’s growing population, estimated to jump from six million to more than eight million by 2030. At present, around nine million trips are made daily in the city, causing major congestion and air pollution issues. By implementing the new public transport system, the Kingdom hopes to reduce car trips by 803 million per year. This will save more than 620 litres of fuel per person annually and more than $185 million in air pollution costs per year.
“We are visiting retail outlets, offices and homes to introduce the project and tell them about the detours during construction. People appreciate this because they then understand that this project will improve their lives for the future,” he concludes.
IN PICTURES: Riyadh Metro carriages roll off production line at Alstom plant