Building a Case: A tour of the equipment giant’s manufacturing base
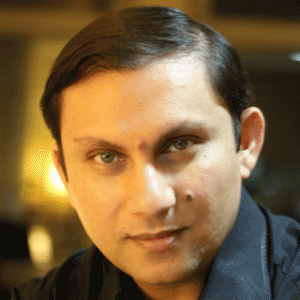
Attention to detail and a dedication to quality are key at the Case facility in Italy

For a company that has been in business for more than 170 years, certain habits are bound to stick. The trick is to ensure that those habits are the good ones – which is precisely the area where construction equipment maker Case has excelled.
Since starting production in the 1840s, the brand has gone from strength to strength and is now synonymous globally for quality and innovation in construction equipment. Supplying its products to the world from eight production facilities on four continents, the brand is recognised for both its large equipment such as excavators and wheel loaders, and, especially in the Middle East, for compact machines such as skid steer loaders and backhoe loaders.
A lot of the Case equipment available in our region is made in its Italian facilities, where it begins life at several places together. The engines, for example, are built at the FPT Industrial facility in Turin, which is owned by CNH Industrial – the umbrella groups that owns Case and its sister brands. The final assembly takes place in its plant at Lecce in southern Italy.
Taking CMME on a tour of the facility, plant manager Paolo Piccoli says: “When we talk of Case, we are talking about 174 years of history, so our brand is a really big one. This plant is big, too, with production lines for compact wheel loaders, telehandlers, backhoe loaders and wheel loaders. Starting this year it is also producing a grader model for the European market.
“Our fabrication arm produces the main components in house, such as the chassis and all the booms. The production volume is around 17 machines per day, which we can, of course, ramp up substantially according to the prevailing demand and order backlog. All models from this plant, except the compact wheel loader, are sold in the Middle East.”
Production begins with precision laser cutting of the main components, followed by welding and painting. Machining of structures, parts and components are done wherever necessary to meet the fine tolerances required for a product of the calibre that Case makes. Components are received from different suppliers and go to the four assembly lines, where a mix of experienced and young, eager hands put the machines together using the advanced engines from FPT.
Zero defects
In pursuit of a quality product, Case has invested heavily in quality processes at its Lecce plant, where a staunch belief in the benefits of World Class Manufacturing or WCM runs high, Piccoli says.
“We have made several investments to assure zero defects, which is one of the key requirements of WCM. The acceptable number for faults is zero, so we are constantly striving to gain complete control on quality,” he explains. “We started to work on WCM in 2008 and in 2014 the plant won the bronze medal, which tells you how serious we are about delivering on quality. The advantage of WCM logic is that we can see continuous improvement based on training and implement well-thought out methods to avoid errors.”
A spate of quality checks run along the production lines, with the aim of filtering out mistakes as soon as possible and to have the ability to track back to where the mistake was first made for rectification.
The plate cutting areas, the bending and shaping areas, the welding areas, the loader arm fabrication line and the front and rear frame fabrication lines, as also the frame, boom and axle painting areas, all have individual quality gates with various tests.
Thereafter, the final assembly process has its own sets of quality checks, not the least of which is a specific double check of all the tightening torques. At the end of the line, 100% of finished production units undergo functional tests and the all-important hydraulic stress tests.
“Quality gates detect errors and double check for all the torque. This is really important because the hydraulic system is the heart of our machine, so we absolutely cannot allow any problem to arrive at the end of the line and none whatsoever to our customers,” says Piccoli.
While production may be over, for many machines, an ordeal is just about to begin. Experts from the plant’s proving grounds take over next, putting random machines through rigorous steps at the on-premises test facilities and testing them to within inches of their lives. The machines are driven for hours on various kinds of terrain and made to perform repetitive tasks. Some are packed into a special chamber where they are rolled and flipped over, lifted up, turned upside down and dropped, smashed and impacted from all sides to test for operator safety in case of an accident.
While individual components and systems have already been qualified with pre-production testing in a dedicated facility with 10 individual test cells, of particular interest to Middle East customers are some extreme tests that simulate job site conditions in the region. The transmission and clutch are hooked on to a dynamometer and put through 20,000 continuous cycles of engaging and disengaging, then measured for wear. In another cell, called the climate room, the machines are run through temperatures that are first lowered to -50 degrees Celsius and then raised to 60 degrees.
In the end, Case ensures its machines can take a tough life, so that its customers have an easy one.
The heartbeat of the brand: Fiat power train plant
At the heart of a Case or CNH Industrial product, there beats an engine that bears the FPT Industrial brand.
FPT, or Fiat Power Train, is the arm of the CNH Industrial group that develops, produces and sells engines for industrial, on- and off-road vehicles, marine applications and power generation. With a large production range – six engine families with a power output from 31 to 1,000hp and gear-boxes with torque ranges from 300 to 500Nm – and with a huge focus on R&D activities, FPT Industrial is one of the biggest players in the industrial engine sector worldwide.
FPT Industrial’s 86,000sqm Turin plant is a WCM Silver-level facility, said its head of operations, Domenico Nucera. Among the group’s production sites it supplies engines to are the Case factories in Lecce and San Mauro.
“The plant is the product of a joint venture called EEA (European Engine Alliance) signed in 1996 between Iveco, CNH and Cummins. FPT was born later, in 2005, for the development and production of a new engine called NEF (New Engine Family) – a high-quality product that had to remain competitive in the market while following the new European standards on emissions.
“Today we are producing every kind of engine, including Euro VI for on-road applications and Tier 4 Final for off-road, with a total annual production capacity of 200,000 engines,” Nucera says.
The NEF engine that the plant produces is one of the most popular engines in various applications across CNH Industrial products. It is a modular, four- or six-cylinder engine used for on-road, off-road, marine and power generation purposes.
The CNH Industrial premises in Turin is also home to another important facility – the Turin Testing Center of FPT Industrial. On this site, which covers an area of 28,000sqm, 400 people work in three shifts to not only test every aspect of the engines produced by the FPT plant but also to research new technologies and develop new power trains.
WCM application: Efficiency through comfort
Working under the World Class Manufacturing (WCM) principle that an easier work environment leads to greater efficiency, Case’s Lecce production facility expends considerable thought and effort to make the work station more ergonomic for its line workers.
Automatic guided vehicles deliver specially-crafted component trolleys to every line according to the machine being assembled on that day and at that time. All components are held in neatly laid out trays on the trolleys, arranged in such a height that a worker does not need to either bend or stretch.
Hydraulic pipes and tubes are arranged in a colour-coded sequence on the tray that tell the worker where they are meant to fit and in what order. In a strictly codified process, nothing is overlooked or left to chance. Not even operational comfort for the line workers.
The end result is an error-free manufacturing process, giving the customer a faultless piece of equipment that will run to its optimum capacity from the word go and provide years of seamless service.
Sharing the brand experience: CNH Industrial Village
The people at Case are proud of their brand, as of course are the people at all other brands under the CNH Industrial umbrella. And justifiably so. They have been making heavy machinery, industrial vehicles, cars, trucks and buses in Turin for more than a century now and have produced some of the most innovative products in the world at various times in their history. With such a history and heritage, pride is natural.
To share this pride in their legacy with customers and automotive technology buffs, CNH Industrial has built an entire facility to showcase their history and heritage. The CNH Industrial Village, built on the same sprawling premises in Turin as the FPT factory, offers an immersive brand experience to visitors right adjacent to the plants where the group’s engines and equipment are being produced.
The Village, inaugurated in 2011, is a restructured area, which once housed workshops for vehicles of the historical Fiat SPA Stura complex. The facility is open to the public, and sells, supports and presents the products of Iveco, Case, New Holland and FPT Industrial. It is also the preferred venue for the group’s international product launches, meetings, events, congresses and training initiatives, often hosting events with attendance in the tens of thousands.
Spread over a total area of 74,000sqm, of which 23,000sqm is covered space, the village houses one of the most important museums of commercial vehicles in Italy, displaying collected and restored models covering more than a century of automobile production in the country.
It also has 8,000sqm of space exhibiting vehicles currently produced by the CNH Industrial group, as well as the Industrial Village Cafè and merchandise store, which are open to the public.
To make the experience even more immersive for visitors, the Village also offers technical guided visits conducted by specialised guides in several languages. Multimedia totems inside the facility also transmit the message, value and vision of the group, taking visitors through a journey of the history, brands, corporate structure and achievements of all its brands.
Every year, the Village hosts thousands of visitors from all over the world – from student groups and tourists to corporate guests, dealers and customers – giving them an insight into the CNH Industrial brands and their values.