How to reduce construction costs and manage price fluctuations
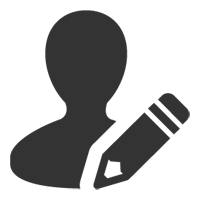
Hill International?s vice president David Rupp and project controls manager Lloyd Bruce Grant offer advice on reducing construction costs and managing price fluctuations in a changing market
Changing materials prices can cause major challenges for the construction industry when identifying costs, but pre-construction preparation and smart project management could reduce risks.
Firms should start by identifying priced worldwide commodities such as metals and cements, identify MEP systems from worldwide suppliers, research local materials markets and outline any special materials required, such as marble or ceramics, according to the firm’s international vice president David Rupp and project controls manager Lloyd Bruce Grant.
The next step is to identify costs by comparing similar projects, researching the market and looking at your own company’s historic data.
“These are great ways to compare, track and see how costs are moving, particularly when monitoring steel price fluctuations. However, it can be tough collecting quality cost historic data and if this is not generated internally you will need to buy it from consultants. It’s important to have this information or you are operating in a fog,” observes Grant.
“You should also ask employees with international experience to compare local and global markets, and utilise clients’, contractors’ and sub contractors’ databases and knowledge bases. Contractors in particular can offer sound advice, which is why it is useful to bring them onboard early.”
Furthermore, Hill International recommends keeping track of changes in real estate demands, construction laws and even expenses such as fuel prices, which can all affect costs.
Lowering costs
Once costs have been identified and you have an idea of where material costs are heading, you are in a position to redesign the project and cut the scope, if needed.
It is recommended to carry out valueChanging materials prices can cause major challenges for the construction industry when identifying costs, but pre-construction preparation and smart project management could reduce risks.
Firms should start by identifying priced worldwide commodities such as metals and cements, identify MEP systems from worldwide suppliers, research local materials markets and outline any special materials required, such as marble or ceramics, according to the firm’s international vice president David Rupp and project controls manager Lloyd Bruce Grant.
The next step is to identify costs by comparing similar projects, researching the market and looking at your own company’s historic data.
“These are great ways to compare, track and see how costs are moving, particularly when monitoring steel price fluctuations. However, it can be tough collecting quality cost historic data and if this is not generated internally you will need to buy it from consultants. It’s important to have this information or you are operating in a fog,” observes Grant.
marketengineering during the design stage to avoid the risk of additional costs and growth delays through over engineering.
“An over-engineering and cost analysis review is absolutely essential so you don’t have to overdesign to compensate for poor quality control during the construction process,” explains Rupp.
Part of this involves improving construction-quality programmes and generally being aware of the lifecycle of the building and components within it.
Furthermore, owner requirements should be clearly outlined in contracts and the contract method should promote flexibility and change.
“It’s a two-way street. As the market changes, the client may wish to go back to contractors and renegotiate, a good relationship will help to achieve this.”
In addition, team dynamics are critical to managing costs.
“There has to be a working relationship between the contractor and designer, and all technical skills must be available on site.
TOP 1O TIPS
• Identify priced worldwide commodities and MEP systems from global suppliers
• Research the availability of and demand for local materials
• Outline any special materials required for the project, such as marble or ceramics
• Compare similar projects and look at your own company’s historic data
• Utilise clients’, contractors’ and sub contractors’ databases
• Keep track of changes in real estate demands and in construction laws
• Carry out value engineering during the design stage
• Improve and implement construction-quality programmes
• Contract methods should promote flexibility and change
• Decisions should start on day one of the project