The balancing act
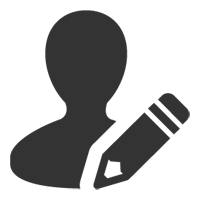
Predicted inflation of 2.7% for the construction industry in 2011 according to EC Harris

Analysts EC Harris predict inflation in the construction industry will increase 2.7% in 2011 Managing partner Nick Smith explains the opportunities and threats on the horizon
Historically, upturns are when you see the most companies going out of business when the market picks up they are left with difficult contracts, which are probably under-valued, and it’s obviously a concern.”
For 15 years Nick Smith has analysed markets in Poland, Russia, Malta and Istanbul, among others. Now a managing partner in the UAE office, Smith says the primary threat facing companies that survived the downturn, is to be left with “a half-built project and a contractor facing liquidation”.
“The first challenge is that best price isn’t always best value it’s a cliché but it’s true. Businesses need to ask themselves if a tender is economically viable.
“We all understand the expectations on price, and it can be appropriate,e but that’s not always the case and I think there are projects that have been bought now that won’t be completed,” he predicts.
“To reiterate the point, in a recovering market, the start of the upturn is the time to watch out for business failures.”
The UAE Tender Price Index 2011 compiles data on labour, material prices, overheads and tendering levels, while also monitoring perspectives from a number of contractors, interviewed by the company on a quarterly basis.
The 2011 index produced four key findings: construction inflation in the UAE is expected to increase around 2.7% in 2011; commodity prices are “considerably higher” than a year ago; competitive conditions will continue to suppress material prices and tender prices will rise by approximately 4.2% in 2012, then rising by a “steady” 5% in 2013 and 2014.
“What we have seen since 2008 is a circa 25% reduction in tender prices, something quite flat in the market and a lot of pressure on commodity prices,” Smith observes, adding: “The cost of stuff is going up; it’s as simple as that.”
[facts]
Predictions
- In 2011 competitive conditions will continue to suppress the affect of material price rises.
- Tender prices will rise by approximately 4.2% in 2012 and continue to grow around 5% in 2013 and 2014.
[/facts]
Specifically, prices of rubber, tin and nickel have increased by 61%, 48% and 31% respectively. Rebar prices are also up by 28% and copper prices are currently 24% higher than they were in January 2010; having risen 10% in the last three months alone.
EC Harris say the rise will have “a substantial impact” on the installed cost of mechanical and electrical engineering installations, and will thus result in higher sub-contractor prices for MEP installations.
On the other hand, the price of zinc has dropped 6% and cement 17%.
The base weighted index is formulated on the EC Harris cost model, representing a regional, generic building type. The study samples new building schemes in the UAE, subdividing construction costs by labour and materials.
The figures for individual schemes were averaged to produce an “indicative percentage breakdown” for the cost model, with these figures then applied to current rates, using the base date of January 2006.
“At the moment contractors are forcing prices down. They are suppressing the increase in material costs, but ultimately there will be a redress of balance to what the project should cost. Currently we are seeing a lot of projects being bought below cost-price and that could manifest problems later.”
Creating stability
Commenting on the action which could be taken to control adverse effects, Smith advises balancing the project portfolio undertaken to minimise exposure to market risks.
“It’s about that balanced portfolio of projects, the timing of projects and the ability to control prices by taking a strong position in supply markets,” he says.
Explaining that the pace of the local market accelerated both the factors leading to and the actual crash itself, Smith continues: “What is better is a range of projects and contracts so we get balanced and realistic prices, which represent the cost of the asset.
He adds: “It hasn’t historically been the market behaviour but you can only hope lessons are learnt from that.”
In terms of facilitating steady and strong growth, Smith says properly planned infrastructure projects have the capacity to re-balance both the market and industry, even more than legislation, which does not always get the right end result.
In fact, Smith says the legislation most likely to affect procurement is environmental rating systems such as Estidama, which could see declines in the use of both traditional materials and traditionally manufactured materials.
In the absence of trade legislation, Smith predicts increased public spending will sustain suppliers in the requried “balanced fashion”, thus optimising market conditions.
Conditions for success
In order to prevent artificial prices in future, Smith says balance is the key.
“I think we all hold a responsibility. There is a drive for clients to get costs down, for example contractors are keen for turnover as they have financial responsibilities so they may work on a reduced margin to retain the company size and turnover. Even from an urban planning point of view you want to balance projects so the market can sustain them, so to that effect the whole industry has a part to play.”
The index states 2011 will be a year when “positive action will create conditions for success”, but this won’t happen without caution.
“This year for sure will be a challenging year and clients will have to be prepared and organised to get the best value from their assets. They need a clear business plan around what they are trying to get from a development, a clear ROI structure and market research on that investment. Additionally early advice, structured in the right way, is critical.”
Muzammil Shaikhani, Managing Director, Rubber World Industries, talks about the impact of rising prices
The continuous increase in raw material prices has definitely left an impact on our operations. However, keeping in mind our vast experience and with highly skilled and dedicated research and design team, we are now trying to delay passing off this rise for as long as we can.
Our R&D teams work long hours to balance the formulations of our product so that we can continue to maintain the same better quality of products, while minimising the operating expenses. We are also trying to find the best ways to maximise production and simultaneously, we are aiming to devise methods on how to minimise wastage. Last but not the least, we purchase our materials from some of the best and established companies, where we have a long-term commitment of supplies from them.
We have also used the increases as an opportunity to find innovative ways to minimise the same and make ourselves leaner and better to avoid passing on the increase to our customers.
Moreover, our market share is quite substantial and our name is well known so it does not cost us much to promote our products.
We will increase our sale prices only if the raw material prices continue to increase dramatically.