Suit up! How robotic exoskeletons could transform construction
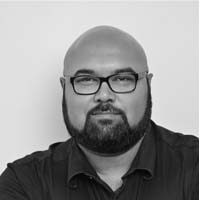
Will building workers of the future wear high-tech suits?
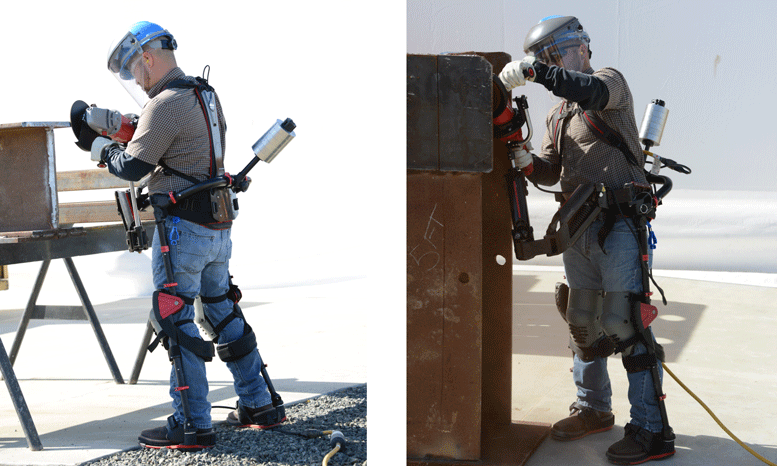
Science-fiction fans know the concept of a powered exoskeleton being used in an industrial setting is nothing new. Legendary film-maker James Cameron riffed on the concept back in 1986, when he had Ellen Ripley take on the titular villain using a ‘power loader exo-suit’ in the climax of the classic film Aliens.
While we’re still a while away from having a suit intricate and robust enough to take on a terrifying Alien Queen, manufacturers and developers are looking closely at how to develop exoskeletons that allow construction and industrial workers to perform tasks beyond their current physical capabilities.
One of the first to enter this fascinating field is Ekso Bionics, a Richmond, California-based company that claims to have pioneered the field of robotic exoskeletons that “augment human strength, endurance and mobility”.
Having begun life working on projects for the US military out of the University of California – Berkeley, Ekso Bionics was heavily involved in developing what it called a Human Universal Load Carrier, HULC for short. However, it soon became apparent that a university environment wasn’t the right place to move forward as a company, and as a result Berkeley Exo-works was formed in 2005, explains Tom Mastaler, business development – Industrial at Ekso Bionics, during a Skype interview with Big Project ME.
“We were really looking at continuing our mass-military applications, but those tend to be very far-out types of projects that are very futuristic. They’re not going to lead to any commercial business. So, based on the successes that they were having, the company ventured off into the medical space, and there was a natural fit for taking the technology-focused solutions that were being brought to bear by military projects and putting them to a very practical use.”
The company began by creating powered exoskeletons for spinal cord injuries. That is a fairly limited market, but it turned out to be a very good one, as customers were highly motivated and willing to experiment with the suits during their rehab periods, giving the design and build team a lot of valuable data and feedback.
“Based on that, the company began to ask, ‘What would be next?’ By marrying some of the military software programming and the medical units, we were able to come up with what we called a Variable Assist Exoskeleton. What that allows us to do is expand into stroke patients, in terms of rehab. As you can imagine, in a number of cases stroke patients can fully recover, but in most cases they recover to some extent and become ambulatory again. What the Variable Assist system does is that it’s able to tune each of the joints of the exoskeleton to the amount of power that the person has lost.
“We tune it with the physiotherapist and we’re then able to measure, in real time, whether or not we’ve tuned it correctly, and the amount of loss that they’ve had. More importantly, we’re able to tailor it up or down a bit to challenge the patient, so that we can have more rigorous or arduous therapy, or tune it back during the session. That in turn allows us to have much faster results in bringing the ambulatory environment back to us. So that’s really key.”
With the first medical exoskeleton launched in 2012, Ekso Bionics now has about 125 units out in the field today, evenly distributed between North America and Europe, Mastaler says. But from 2013 on, the company began looking at powered exoskeletons for outdoor use, much like those that would be used in the military, for troops that have to carry heavy packs and still be able to move quickly.
As such, Mastaler recounts how they looked at naval shipyards, where a lot of dirty, dangerous and demanding work needed to be carried out. These initial explorations convinced the Ekso Bionics team that they could expand the reach of the exoskeleton beyond shipyards and into the construction and industrial landscape.
“What we discovered was that we didn’t actually need a semi-powered exoskeleton, because we have, through some of our own technology – that we’ve patented – the ability to take a weight from around a person’s torso down to ground. Therefore, they’re not actually strapped in or carrying the additional weight of a tool or a mechanism that’s holding a tool,” says Mastaler.
“We refined that a bit further in 2014, and really started talking to potential customers. A lot of them had already heard about us and they understand a lot more about exoskeletons today. We were getting a lot of phone calls, and as we looked into that, we tuned an exoskeleton to what we called an Advanced Prototype.”
Around this time, the company began speaking to construction firms about the possibilities of their exoskeletons. Like most companies that look to introduce new technology into the construction industry, they were met with initial reluctance and hesitation.
“We started going out and talking to large construction companies. The reason that’s important is because whenever you’re introducing a new technology into a new environment, especially in an industry like construction, there’s a lot of hesitancy to be the first on board. What we discovered during the investigations was that the large companies were more sophisticated and could help us get not just the launch of the product, but also the adoption of the product as an everyday tool for workers.”
Ekso Bionics started to work with these construction firms, tuning the exoskeleton into applications that have heavy-duty cycles, can carry heavy weights and can operate in the kind of unstructured, confined environment found on construction sites. To do so, the team went back to the results they had obtained from their military projects, knowing that those could be trusted, given the high standards and specifications required by military clients.
“We looked inside the ergonomics associated with them, and what they liked and disliked. We also looked at the medical space. Even though a person with a spinal cord injury has no feeling, you can still tell based on the straps that they have to wear over their shoulders. You can tell by the sores that they might be developing – because there are rubbing points on the exoskeleton – and a lot of the things that we had solved already in these two spaces, we brought into the industrial space,” says Mastaler.
Made of lightweight aluminium, the exoskeleton is adjustable to different sizing requirements, which means it can be used for multiple applications or workers. A lot of attention was also paid to form-fitting, as workers have to walk to and from work and up and down stairs, and the suit needs to be able to accommodate those movements.
“They’re not always going to be using the tools that we’re providing, so how can they use a different tool [on the exoskeleton], or if they don’t need to use a different tool, how can they continue to wear the exoskeleton for the short period that they might be doing something different, in a way that doesn’t make it cumbersome?
“We’re still working through it, as a matter of fact. The advanced prototypes have now gone into field testing. We have sites in the United States and in Europe. We’ve really just started the process of training a company in how to put a worker in an exoskeleton. We’ll be able to watch them work and take their feedback on what we did well, and also what we didn’t do as well as we’d hoped to do.”
The next phase of development will be redesigning a production-available cycle of the unit. That is pencilled in for late this year or early next year, according to Mastaler. “While we do that, we’ll continue to go back into the field, because it’s most important to us that the worker is comfortable and that we’re providing a tool that assists and doesn’t detract from how a worker does their job.”
At the moment, for the construction industry, Ekso Bionics is focusing on developing a completely non-powered suit consisting of a chassis which runs from the ground up through to the hips, and has a harness and a back-plate.
“The chassis is what directs all the weight down to the ground. Off that chassis, we can either put in what we call support arms, where if a worker is doing something where they need the dexterity of their hands, or if their arms are in an upward motion, then they can work all day, without feeling fatigued in their arms and their shoulders.
“The other application is to be able to take a power or a hydraulic tool – something that has to be held in place – and we have a balance arm, which is basically a spring-offset arm that’s attached to the chassis and sits in front of the worker. That allows the tool to become weightless, and now the worker becomes more of an artist than a weight-lifter.”
With the current set-ups available, the suits can comfortably take tools in the 15-20kg range, while some field tests have revealed that they can go up to as much as 35kg. In addition, the field tests have shown tremendous results when it comes to increased productivity and performance, as Mastaler explains.
“We’ve seen workers who might be using chipping tools or hammers to demolish something. They might do five to seven minutes of work, and then take a five-minute break to recover, followed by another five to seven minutes of work. As you can imagine, over the course of a day, those five to seven minutes get shorter and shorter as fatigue takes over.
“The longest we’ve actually done [with the suit], before we stopped the work, was continuously doing chipping work with a demolition hammer for 40 minutes. If you take five times that, and you look at the breaks in between, then you’re tripling your productivity, without the fatigue factor. In fact, at the end of 40 minutes, the worker asked us why we had stopped him from working!
“Other workers responded that in the morning when they’re fresh and start their work, they feel fine, but over the course of the day, it becomes harder for them to hold tools steady, and they notice more defects that quality inspectors uncover, and don’t do as much work. So in their instances, it’s a two to three times increase in productivity.”
While increasing productivity of the workforce is obviously a major attraction for any contractor, Mastaler is keen to play up other aspects of the exoskeleton. Key construction jobs often require skilled labour, and in an industry where there is an increasing gap between new, incoming workers and those at the end of their careers, finding ways to increase the longevity of an existing skilled worker is becoming crucial.
“Large construction companies understand that they’re looking for productivity; however, they’re also stressed these days with skilled workers in key jobs. They’re extremely stressed with adding new workers to their workforce, because the younger generations coming along are not as interested at wanting to be in construction-centred trades.
“There’s a gap that’s forming, where new workers coming into the space are declining, while the number of workers at the end of their careers are going to expand. You need to do something different to what you’re doing today, because otherwise you’re going to run into the hard, arduous type of work that has to be done by skilled workers, which they’re not capable of doing any longer.
“Companies are coming back to us and telling us that these fatigue factor and saving concerns are adding up to larger savings for them as a business. Where they’re coming from is that the fatigue that occurs during the day, the defects that have to be fixed, the lost time, the accumulation of injuries over time – at the end of the day, the companies cannot get their workers to do as much as they think they can get out of them.
The revenue side of it can also be expanded by having workers stay on a job site longer, and not have as many injuries. So while productivity will always be a key measure, I believe that it’ll start to become a low bar to get over, while the high bar will be on the fatigue side.”
Of course, the Middle East is an entirely different market to the US and Europe. However, Mastaler reckons that Ekso Bionics’ business plan will allow it to succeed in a market where early adoption levels aren’t necessarily the highest.
“We’ve basically built our business model around our Round One applications being successful. We’ve targeted six major applications that we’ve found. Whether it’s in the metal side of industrial construction or the concrete side, it’s fairly balanced between the two. It allows us to access large construction sites, which you have in Dubai, as well oil refineries, where metal is prevalent pretty much everywhere.
“As we’ve looked at these applications, we’ve talked to customers about how workers perform, but also how they fit into a segment that is the most demanding, heavy-duty cycle, but also the most dangerous type of safety environment. That market alone is enough to support exoskeletons, and we believe that it’s a foothold in the market that gives us options.
“The Round Two applications, which are lift-and-carry, that’s probably the most prevalent activity on a construction site. So you would think that there would be many more workers that would be eligible for exoskeletons in that type of an environment. In addition, we’re talking about factories, warehouses and logistic centres, because that’s what they do.
“Now that’s a fairly large market. We’ve seen in our research, between North America and Europe, there’s probably nine to 10 million construction workers. We’re targeting less than a percent of that market with our exoskeletons. And we believe that will be financially successful. I would say that our biggest worry is that we’re wrong and that the market is going to be larger. Then how do we keep up with the market?”
Coming to the Middle East market itself, Mastaler says companies here will be looking closely at productivity, as well as lower-cost units, given the lower wage rates here. As a result, Ekso Bionics will adapt their business plan accordingly and offer their products to factories and logistics firms, who will have workers doing similar jobs in the lift-and-carry sector.
While he says pricing hasn’t been confirmed yet, Mastaler is quick to assert that the company is looking at the production design and working to come up with figures that balance out the manufacturing costs, taking into consideration the after-market services they will also have to offer.
“As we’re pursuing that, and getting clients in, then we’re able to look at it from our own business perspective, what level of margins are we willing to go into the market with and grow into with, and how we go forwards,” he concludes.