Site visit exclusive: One Za’abeel, centre of the city
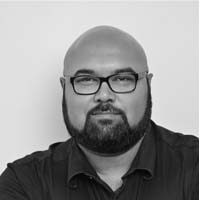
An exclusive tour of One Za’abeel, a new mixed-use development being built by Ithra Dubai

In many ways, the community of Zabeel in the eastern part of Dubai, can be considered the heart of the city, as it is adjacent to vital road links that connect it to crucial business, commercial and residential hubs such as DIFC, Dubai World Trade Centre, Dubai Mall and Sheikh Zayed Road.
Divided into two sectors – Zabeel One and Zabeel Two – the community is also home to HH Sheikh Mohammed bin Rashid Al Maktoum’s palace, as well as the famous Za’abeel Park, one of the largest in the city. As such, it’s easy to see why it holds a special place in the hearts and minds of Dubai residents, especially those living in the surrounding area.
Given its central location, it seems obvious that Zabeel should have a destination reflecting its standing within the city, and with the launch of One Za’abeel in September 2017, that is now becoming a reality.
Planned as a mixed-use development consisting of two towers linked by the world’s largest cantilever, the project is set to become an instant icon in Dubai’s skyline, given its location, scale and distinctive design. Once complete, it will feature luxury hospitality and residential elements, along with grade A office space and a high-end retail podium.
Designed by Japanese architects Nikken Sekkei, the project is being developed by Ithra Dubai, a real estate developer owned by Investment Corporation of Dubai (ICD). ALEC, a Dubai-based multi-disciplinary construction company, has been appointed as the lead contractor on the project, while WSP is operating as the structural and MEP engineer. Mace is overseeing the entire operation as project manager.
Construction on the project started in late 2017, with work progressing rapidly once ALEC was appointed to the project, starting with a 28m excavation completed in September that year. At the time of visiting the site in July 2018, the tower cores were both at Level Two, while basement levels B7, B6, B5 and B4 had been constructed.
The construction of One Za’abeel promises to be extremely complex, with the two towers having 67 and 57 storeys respectively (Tower A will be 304m high, while Tower B will be 238m high). The massive cantilever – known as The Linx – will be suspended 124m above the ground. The entire structure will rise up from a three-level podium and seven basement levels.
However, as complicated as this already sounds, perhaps the most significant engineering challenge is the enormous Al Sa’ada Bridge bisecting the site, which has been incorporated into the project design. Once construction is complete, the bridge will run between both the towers and under the span of The Linx, creating a distinctive and inspiring structure never before seen in Dubai, says Issam Galadari, director and CEO of Ithra Dubai, who sat down with Big Project ME for an exclusive interview and tour of One Za’abeel.
“The location of One Za’abeel is at the heart of Dubai. All the people that live in Dubai, they know where the World Trade Centre is, and One Za’abeel is really close to it, it’s opposite the Trade Centre and the location and connectivity is great,” he asserts.
“It’s like an island, if you look at it. It has fantastic connectivity in terms of infrastructure, it’s close to Downtown Dubai, to DIFC, it’s very central. The view from the project is great as well. You have Za’abeel Park, which is very close, and the view of the city towards the Creek, and also towards the coast, is great. And it’s right on Al Sa’ada Bridge, so the two towers, with the bridge in between, will create a great experience, even for people visiting Dubai for the first time. They’ll be coming in from the airport and they’ll see the two towers and they’ll be driving between them. It’ll be a great effect, I don’t think they’ll have another experience like this in Dubai.”
Galadari reveals that the design for the tower was influenced by the plot of land. With the bridge cutting through the land area, the design team were forced to get creative to come up with a design that would incorporate it.
“We then had the idea, about what could we really take advantage of with the existing situation? What can we create that would complement the other iconic buildings in Dubai? We’re not competing with them, not in terms of height, but this is a luxury project and it’s got to be a great project, it’s got to be iconic.
“So we decided to take advantage of the bridge and make a really beautiful, attractive and luxurious development that is at the centre of Dubai. The two towers, The Linx and the bridge in between – this is how we started. Then we engaged a number of international architects, we created a competition and then we reviewed the different ideas they had.
“It’s a beautiful model [design], but it was important to have it very simple and timeless. What we’ve come up with, we feel that we’ve got that – it’s iconic and timeless.”
Work on the project started in 2014, and one of the key elements is the residential aspect, Galadari says. As such, it was decided very early on in the design process to put the residential tower on the far side of the bridge, closer to Zabeel Park. This was a conscious decision, keeping in mind the safety of the younger residents of the tower, he explains, as there will be a pedestrian bridge connecting the residential tower to the park, creating a safe avenue for residents and their children to cross over.
“This is especially for the children, so that they don’t have to cross the roads. We created the bridge that will link from the residential tower area, so that residents can get to the park and enjoy that area. I don’t think a lot of developments have such proximity to a park, in terms of towers.
“In addition, the tower will also have its own amenities and facilities in the building or the podium, such as swimming pools, playgrounds, gyms and so on. Residents can be assured that if their kids go out of the building to the park, it’ll be safe. They don’t have to worry about them crossing roads or anything like that, as it’s a straight connection.”
This concept of connectivity is also repeated in the commercial tower, which will hold grade A commercial offices, a One and Only Urban Resort Hotel and the new headquarters of the Investment Corporation of Dubai.
The offices will be housed in the section of the tower below The Linx, while the hospitality section will run to the upper floors of the tower, though the highest levels will be reserved for the new headquarters, Galadari says. Like the residences, the office tower will also have a bridge providing easy access to the Dubai World Trade Centre.
Work on One Za’abeel is progressing according to schedule, he adds, with the targeted completion date in the latter half of 2020. He’s quick to point out that while there are always hiccups during the construction process and a lot of challenges – especially around the complexity of the structure – a large part of the credit for the smooth operations thus far is due to the main contractor on the project.
“Having ALEC as the contractor [has been very helpful]. They are one of the best contracting companies in Dubai. You can feel the quality of work even as you drive up to the site offices, with the area being so clean. When you enter the lobby of the site offices, you can feel that it’s different. It may be a simple thing, but it’s about how you handle things. If this is the site office, just imagine what the project is going to be like.
“Actually, a lot of contractors were invited to bid for the project, and eventually we landed on ALEC because they were the most attractive bid, not just in terms of the price, but also because of the quality of delivery and their past experience. I know their work personally, as they’ve done work for me in the past in my other organisations, and they’ve done quality jobs. They’ve done all types of projects – mixed-use, airports and so on. We’ve seen that they are the ones who can deliver a project to a very high standard, and according to what we expect it to be.”
Construction logistics are the main challenge, as can be expected, given that the site is an island plot surrounded by a major road network. However, ALEC tells Big Project ME that its project team worked closely with Mace to plan and operate multiple logistic models. These include just-in-time, off-site prefabrication, consolidation centres, staging zones and pre-cut materials, which all helped to reduce the known hoist cycle time.
Given the scale of the project, coordinating operations on-site was also a challenge, with ALEC having to coordinate each trade, starting with a Logistic Welcome Pack issued at the kick-off meeting. With this pack setting out the site protocols, the contractor was able embed processes early, allowing its project team to carry out daily coordination programmes with each trade contractor.
Designer coordination on the project is carried out by Mace, which then issues the Information For Construction (IFC) to ALEC. While ALEC is certainly in charge of the construction process, Galadari does add that Ithra Dubai plays an active role in overseeing progress on-site, with the developer’s CEO keen to establish and build strong partnerships between all parties.
“We have a strategy of developing projects together. We don’t work with contractors and consultants as just contractors or consultant firms, we work with them as partners. We believe strongly in partnership, and that any project you start is an adventure, and that a strong partnership between all parties is crucial.
“From my chairman through to me and through to my other colleagues, we are all involved. We don’t leave the project alone, even down to the handles on a door. We are all partners on the project, and if there are issues, or if any challenges arise, it’s discussed among us. I’m personally involved. If the contractor has any issues, he brings it to us and we discuss it with the project managers and the architects and designers, including our own ones.
“We also have weekly meetings and executive meetings as well, where all the executives of the companies are involved. We are very happy with how things are going so far, we’re working well together, and I believe that we’re all very strong as a team.”
This high level of coordination is best exemplified by the way the two towers are being built in conjunction, with ALEC explaining that the project teams are split in the same way, one for Tower A and one for Tower B, with weekly logistics planning carried out as one project site. This is because there is only one site perimeter road.
Furthermore, the bridge is monitored 24/7 for movement, while the project team coordinates closely with both Dubai Municipality and the RTA, meeting every week to ensure that the required NOCs are in place in a timely manner.
“As I’ve mentioned, we are partners with the consultants and the contractors. We are in the trenches with them and we work with them. We attend a lot of those meetings with the RTA and the municipality to understand [what the issues are]. It is a very challenging development, and nobody has done an excavation like this – seven levels below and adjacent to a live bridge.
“You can see how close it is and how deep we’ve gone. We’ve managed to work with the authorities to make sure that everything is proper and that the safety standards are in place. We have to make sure that the bridge doesn’t even move – it can’t bend or tilt,” he stresses.
“We are heavily involved with [the discussions] and we will continue to be heavily involved with them. We are partners and we want to make sure that we achieve what we’ve started, to the highest standard in the world.”
Given the location of the project, one major challenge ALEC is the movement and management of the workforce. At present, the current workforce is 3,000, but at peak that number will grow to 10,000. Manging these numbers will be quite the task for the contractor, but it says there are plans in place to ensure the smooth flow of personnel on and off the project.
The movement of men will be carried out by 10 construction hoists and three jump lifts capable of moving 5,000 men in two hours, the contractor explains to Big Project ME. When it comes to the logistics around the movement of materials and construction, floors will be pre-loaded with cut/prefabricated materials during the night shift, so that the day shift can install them.
The façade will be unitised on both towers, loaded onto cassette units and lifted onto loading platforms, to be installed by monorail cranes during the day. This streamlined approach to delivery and installation of materials will help speed up operations on-site.
One of Galadari’s biggest concerns is the welfare of the workers on-site. He asserts that it is part of Ithra Dubai’s mandate to have health and safety as the first item on its agenda, no matter the scale or prestige of the project.
“This is emphasised from the kick-off meeting we have when we engage our consultant, and when the contractor comes on board with us. We make sure that the safety of people on-site is the number one focus for us – they are the ones that should be at the top of the agenda for any company.
“It doesn’t matter what position they are, we are all human beings and we have to make sure that we look after each other, one way or another. I’m very strong on that point, about looking after all of these labour forces. They deserve the respect of everybody as they are the people building the country, they are the people who built Dubai and I value what they do,” he states strongly.
“If there’s anything that we don’t feel is proper, then we’re ready to stop the work, no matter the number of days it takes, so as to make sure that safety is number one.”
With regard to construction technology, ALEC says single-deck jump-form rigs have been used to construct the cores, while a sliding screen system protects the outer perimeter of each tower over three floors. This aids production by removing the risk of falls and falling materials. Furthermore, jump lifts will be used to remove the construction hoists early on, to allow the façade to be completed.
In addition, 10 tower cranes are being used currently on the project, including a Favco M2480D with an operational capacity of 110t, four 100t mobile cranes and one 50t mobile crane. Additionally, eight concrete pumps were used to cast the 16,100m3 of concrete for the foundation of Tower A, which was completed in 72 hours, the contractor says.
“We are using the latest technology that is available to us in construction. ALEC is one of the best contracting companies, and we have discussed this with them. We are using BIM in our project, it’s being used very efficiently,” Galadari adds. He also reveals that One Za’abeel will be targeting LEED Gold certification, going well beyond the standards and regulations set by Dubai Municipality.
“From that aspect, we’re going beyond what the requirement is. I’m very happy that we’ve pushed for it and hopefully we’ll get LEED certification at the end of the project, as that’s our target. We have a LEED consultant working with us, looking at all the small items in development, helping us make sure we achieve that certification.”
Finally, he points out that although construction on The Linx is still some time away, the project team has already begun mapping out the engineering and construction that will go into putting it into place. Once complete, the cantilever – set to be the world’s largest – will float 124m above the ground and run for 210m, offering several hospitality options to visitors, guests and residents.
“A lot of people ask about The Linx. They wonder what it is, some of them even ask if it’s just a bridge between the two towers. It’s not – in fact, it’s going to be a surprise for everybody. It is part of the hospitality offering, special venues will be there, signature restaurants will be there.
“The location is great, it’ll be over Al Sa’ada Bridge and it’ll have a great view. It’s a location that I think is stunning and unique, with views of Zabeel Park and the city. We have created all the comforts for people to come and live in this unique development,” Galadari says in conclusion.