Doka on formwork

Concrete formwork manufacturer Doka is responding to changing market trends and consumer demand with the introduction of new products and services Doka, a manufacturer of concrete formwork, produces up to 14 million metres of timber formwork beams and 2.4million square metres of three-ply formwork sheets annually. In addition, around 75,000 tonnes of metal is processed […]
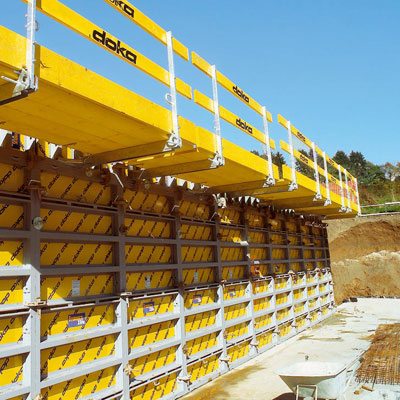
Concrete formwork manufacturer Doka is responding to changing market trends and consumer demand with the introduction of new products and services
Doka, a manufacturer of concrete formwork, produces up to 14 million metres of timber formwork beams and 2.4million square metres of three-ply formwork sheets annually.
In addition, around 75,000 tonnes of metal is processed into formwork components every year. Most Doka products are manufactured in the company’s central plant at Anstetten, Austria and in a new facility at nearby St Martin.
However, the company brought its 130 years’ experience in formwork to the Middle East with its first subsidiary in Kuwait in 1977, and later established Doka Gulf in Dubai and Doka Establishment in Saudi Arabia, Bahrain, Lebanon, Qatar and most recently in Oman.
“Since its establishment in the Middle East, Doka has been able to work closely with clients and became a valuable partner for the local contractors in their quest to keep up with the phenomenal growth rate and continuous evolution of the construction industry,” says Doka marketing manager – Middle East Agata Orlowska.
Projects in the region that Doka has partnered with include Burj Khalifa, Marina 101, U-Bora Towers and Dancing Towers in Dubai, Capital Gate and Sowwah Square in Abu Dhabi, Dubai Towers in Qatar, and King Saud University and Riyadh Ring Road in Saudi Arabia. In the face of increased competition, the company has focused on customer relationship building and enhancing its service offerings.
“Construction companies have been affected by a mood of uncertainty, making them cautious when it comes to investing in new formwork equipment. This is where our rental parks come in, enabling us to offer contractors an alternative to purchasing their formwork,” says Orlowska.
“We have also made intensive efforts to optimise our costs and business processes. This means we now have modern technologies and a highly cost-saving product range that gives customers measurable benefits – more relevant than ever in the present economic climate,” she adds. A trend toward shorter times for completion due to increasing pressure to reduce costs has led Doka to introduce new products, such as load-bearing tower ‘Staxo 40’ formwork and ‘Frami Xlife’ framed formwork. Staxo 40 is a highly cost-effective shoring system. The system offers patented solutions such as tower-to tower walkway openings, which make for safe and speedy work on the scaffold and underneath the superstructure; key to more productivity on the build.
With innovative new ergonomics, Doka developers succeeded in matching lightweight design with rigidity and high load-bearing capability, according to Orlowska. In combination with the ergonomic frame geometry, the lightweight Staxo 40 towers are quick and easy to erect and disassemble by hand. The hand-operated framed formwork, Frami, is tailored for use on smaller areas.
“Frami delivers perfect forming performance even where no crane is available; the panels are lightweight and can be easily erected by hand. It enables quick vertical forming and is commonly and often used in the fields of residential construction,” explains Orlowska. “Its Xlife sheet enables extremely high numbers of repeat uses ensuring long service life and cost efficiency,” she adds.
Furthermore, the company has identified opportunities in social infrastructure and transport infrastructure and is focusing on Qatar, Saudi Arabia and Oman in 2010.